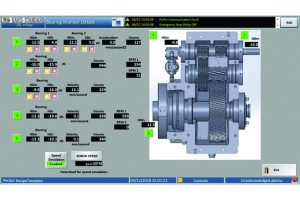
A sample of the Activ-Check screen.
Installing the right equipment is half the battle, but optimizing it for smooth performance is also crucial to success.
Pawcatuck, Conn.-based extrusion and conversion equipment producer Davis-Standard last year introduced its DS Activ-Check system for continuous extruder monitoring. This system, which can be integrated with a variety of lines, collects information on equipment operation with an eye toward early prevention of machinery problems.
“Machine operators are alerted to issues before they happen, reducing unplanned downtime while also collecting valuable data,” Davis-Standard stated in a release.
The Activ-Check monitors the extruder’s lubrication, motor characteristics, drive power unit, reducer, and barrel heating and cooling, according to the company.
Information is collected with several different instruments. Vibration sensors on the extruder reducer indicate the performance of the gears, bearings and lubrication system, the company explained. Additional temperature and vibration sensors take stock of the motor operation.
Details on the status of these components are shared with the operator via overview screens.
“Having the capability to monitor extrusion line variables such as mechanical and electrical system conditions is essential in order to bring products to market faster and minimize unplanned downtime,” said John Clemens, director of extrusion controls for the company, in a release. “This technology will also allow customers to address a pending condition that could become a more serious issue in the future. All of this is valuable and much-needed knowledge to strengthen existing extrusion and converting processes.”
To receive the latest news and analysis about plastics recycling technologies, sign up now for our free monthly Plastics Recycling Update: Technology Edition e-newsletter.
More stories about technology
- Industry nuance is key in adopting emerging technology
- Google, Dow partner on AI to identify recyclables
- Food-grade PP recovery primed for growth