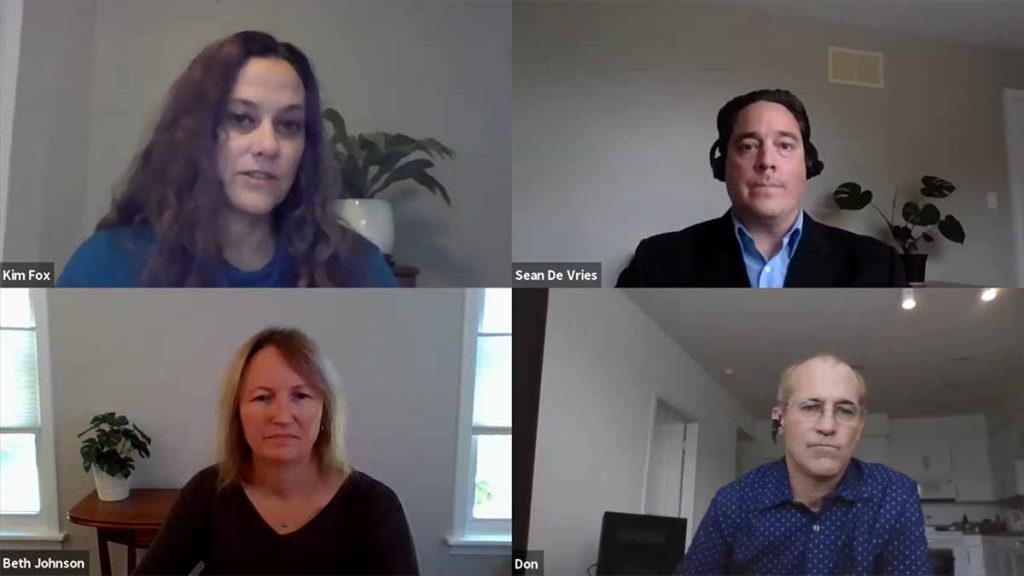
(Clockwise from top left) Kim Fox of Lenovo, Sean De Vries of Sustainable Electronics Recycling International (SERI), Don Hennen of RLG, and Beth Johnson of Dell.
Two electronics manufacturers and a reverse logistics contractor recently described what they look for in recycling vendors. They also discussed how audits have changed during the pandemic – and why some changes may be here to stay.
Dell, Lenovo and the Reverse Logistics Group (RLG) Americas shared their insights during a virtual session that was part of this month’s E-Scrap and E-Reuse 2021 conference (in addition to a live event held in Chicago, the conference offered attendees virtual presentations and discussions delivered via the conference app).
As part of operating takeback programs and receiving end-of-life devices through other channels, the OEMs must select recycling vendors to handle that material. Beth Johnson of Dell, Kim Fox of Lenovo and Don Hennen of RLG laid out the traits they look for in recycling vendors. Although not an OEM, RLG is hired by manufacturers to handle end-of-life or otherwise unwanted IT equipment, and the company works with a network of providers to perform that service.
The session was moderated by Sean De Vries of Sustainable Electronics Recycling International (SERI), which administers the R2 standard.
Selecting competent service providers is vital because the contractor’s performance reflects on the OEM as whole, the speakers explained.
“Our customers expect Lenovo to be ethical, compliant and transparent, and we expect the same of our service partners,” said Fox, who serves as advisory engineer for Lenovo. “Our ITAD partners need to have the same ethics and values as Lenovo to protect our customers and our relationship with our customers.”
Finding a match
Lenovo and Dell both emphasized that their internal policy and performance standards are key to processor selection.
Dell uses a screening process to identify a good match in a recycling vendor, Johnson explained. The company will look for ISO certification and industry certifications such as e-Stewards and R2.
The company will also select vendors based on the scope of services that company provides, and how well it matches up with Dell’s needs. Equally important is the vendor’s method of carrying out those services.
“Their asset disposition, how they handle the data sanitization, data destruction, logistics, physical movement of material, as well as their refurbishment and parts harvesting activities, all of this is very important in our environmental partner selection,” said Johnson, who is Dell’s regulatory senior principal engineer.
Fox of Lenovo echoed similar traits the company values in finding processors to work with.
“When selecting partners we look at alignment with our values, compliance to our standard, their capabilities, certifications, geographical footprint, compliance history,” Fox said. “There’s a whole set of business practices we look at.”
When RLG is considering a processing company to work with, the organization is similarly looking for alignment with its values, as well as the values of RLG’s OEM clients.
“We want to see a culture of innovation which prioritizes reuse first and then recovery,” said Hennen, director of operations for RLG. He added that RLG is looking for “transparency in the downstream chain, and the ability to manage that downstream network not just at the first tier, but all the way to end of life or the first point of reuse.”
How to audit from afar
Once a vendor passes the initial screening process, the OEMs must check and verify that the processor is maintaining compliance. That’s where auditing comes into play, with auditors visiting each partner facility and observing to ensure the vendor’s performance is up to par.
When COVID-19 hit, that whole process was disrupted, and it continues to be today. But from the beginning, one point was clear.
“The audits can’t stop,” said Johnson of Dell. “We have a responsibility to our company to protect our brand, to honor our customer commitments, we have contracts that say we’ll handle your assets and ensure these services are met, in spite of a pandemic.”
Still, in order to maintain health and safety protocols that came about with COVID-19, auditing couldn’t take place in person as it had before.
“We definitely had to change on the fly when the pandemic hit,” said Hennen. “Obviously we switched to virtual, but what we did is we did a lot more discovery upfront.”
RLG’s auditors carried out a lot of the back-and-forth information sharing, particularly checking documentation, in advance of the audit, Hennen explained. That allowed the auditors to focus solely on the virtual walkthrough of the facility on the day of the audit, observing processing operations and uncovering items for later discussion.
Although a definite change, the pandemic shift has worked out well for RLG’s auditing process, Hennen said. It eliminates the potential to rush through certain points of the auditing process due to travel schedules, for example.
De Vries of SERI added that his organization also shifted to remote auditing, and it has found some positive results as well. SERI has found new ways to save audit time and audit costs, he explained.
None of the speakers anticipated a fully virtual audit process in the future, however.
“I don’t think it’s a secret that we all think on-site audits provide the best way to assess risk and evaluation,” said Fox of Lenovo. “But we have seen great results and I’m certain our auditing program will take some lessons from the past year and a half, and we’ll probably create some kind of new hybrid program where we’re taking the best of the old and the new.”
Johnson said there were some learning curves on using technology during audits early on, but for Dell, “what we’ve found is that there are probably more benefits than there were challenges. Challenges could be overcome.”
She added that the remote audit system opens the door for a broader pool of auditors. For Dell, which operates internationally, that meant an auditor in the U.S. could conduct a virtual audit of a partner facility in Europe, she explained.
This article has been updated with the correct company name for Reverse Logistics Group (RLG) Americas.
More stories about OEMs
- Texas passes right-to-repair for consumer electronics
- Oregon shares E-Cycles modernization timeline
- New EPEAT criteria set to take effect in November