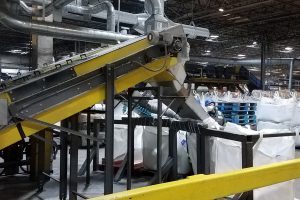
Part of URT’s CRT glass processing system in Janesville, Wis.
One of the country’s largest e-scrap companies is recycling CRT glass into a marketable product that could reduce the processor’s dependence on erratic downstream markets for leaded material.
The company developed technology to process both leaded and unleaded CRT glass into a fine powder used to produce frit. Frit is a key ingredient in compounding enamels and ceramic glazes.
URT has been making the product at its Janesville, Wis. headquarters since early 2018. The company is putting the finishing touches on a glass-to-frit-product system at its Dover, N.H. facility as well. The systems will consume much of the glass handled by the company.
“This is one of the game changers for URT, and really for the industry and our customers as well,” said Jeff Gloyd, URT’s vice president of sales and marketing.
URT’s CRT news comes amid shifting markets for leaded glass processing. In October, Spanish company Camacho Recycling announced it was suspending its acceptance of CRT glass from North America and Europe. According to Camacho, which also processes glass into a product for tile manufacturing, the action came in response to permitting requirements from government authorities. URT and many other e-scrap companies used to send glass to Camacho.
Meanwhile, the winding down of a once-promising North American CRT outlet has reached its conclusion. Nulife Glass, which operated a furnace in New York State to separate lead from glass, recently finished cleaning up its former Virginia site. The company closed and began cleanups in 2017 amid conflicts with state environmental authorities.
Meeting tile maker specifications
About 18 months ago, URT was approached by a tile industry supplier about making a product from CRT glass to offset manufacturers’ use of silica and lead for frit. With guidance from the supplier and relying on the company’s own CRT processing expertise, URT started to implement its first system, in Janesville, during the first quarter of 2018, Gloyd said.
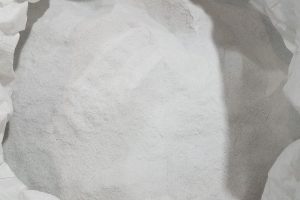
The final product used in making frit for tiles.
To create the powder in Janesville, URT size-reduces funnel and panel glass and mixes in a proprietary chemical. One of the bigger challenges in setting up the line was ferrous contamination. The iron content will result in yellow discolorations in white or clear tiles. URT adjusted the magnets on its line until it could remove the ferrous metal, Gloyd said.
URT already uses CRT processing equipment, including technology to separate leaded from unleaded glass. So installing a new system to create a new product was something of a quick add-on, Gloyd said. He estimated URT’s capital costs to meet specifications for the tile industry were between $300,000 and $800,000.
Staff at URT’s Dover, N.H. site are working to refine a system installed in December to ensure the powder meets tile manufacturer specifications. Product shipments should begin anytime, he said. URT has been shipping the product from Janesville since the second quarter of 2018, Gloyd said.
Each system allows URT to produce about one load, or roughly 20 tons, per shift. With Janesville operating on two shifts and Dover on one, the company will be able to produce about 60 tons per day.
There is a key difference between the Janesville and Dover systems: In Wisconsin, URT is processing both leaded and unleaded glass into the powder, but in New Hampshire, it is processing only funnel glass, where the substantial majority of lead is found, into the frit ingredient. The heavy metal is beneficial to the tile-making process in the high-heat furnaces. URT decided to use strictly funnel glass in the New Hampshire frit product upon the request from tile makers for higher lead content, Gloyd said.
The Wisconsin and Dover systems will consume glass handled at those sites. A smaller URT location in Texas is sending separated funnel glass to Janesville for processing into frit product. Because of the distances involved, however, URT’s Oregon facility is still sending leaded glass to a smelter, he said. URT doesn’t currently have active plans to install frit product systems in Texas or Oregon, he said.
In addition to providing a use for glass coming off of URT’s demanufacturing lines, the systems allow the company to process bare CRT tubes or broken glass from other customers, as well.
‘Owning our own destiny’
The value of the frit product itself isn’t a game-changer, Gloyd said, though he noted URT thinks it’ll provide a savings over separating and sending glass to a smelter or Camacho.
The big value is in lessening company risk by reducing usage of sometimes unreliable downstream outlets, a benefit he describes as “owning our own destiny.” Gloyd cited limited and inconsistent smelter demand in North America, as well as Camacho’s dispute with regulators.
Gloyd also emphasized the risk-reduction value of turning a waste containing lead into a saleable product.
“Anytime you can own your destiny – anytime you can turn something that’s a waste into something that’s not a waste – the value is immeasurable,” Gloyd said.
URT’s frit ingredient buyers – as well as those it’s still pursuing – are located in North America, South America and Europe, Gloyd said. He said Camacho’s disruption was a result of a decision by Spain’s environmental department.
“That could happen in any other country. But the tile industry, itself, exists internationally in multiple locations. Our relationships are outside of a single country,” he said.
He sees an almost unending appetite for the frit product, which is cheaper for tile manufacturers than the lead, silica and other fluxes they otherwise use.
“I don’t think there would be a limit to our ability to move the material,” he said. “As long as we’re processing glass and churning out a quality product, we will have a downstream to sell the product to.”
Photos courtesy of URT.
More stories about CRTs
New shredder installed
Processor URT has installed an additional shredding and separation system. The move is a response to the evolving e-scrap stream and, more immediately, the desire to reduce freight costs.
During the third quarter of 2018, URT installed the system at its Fort Worth, Texas location. The company already uses advanced shredding and separation systems at its Janesville, Wis. and Clackamas, Ore. locations.
The Texas equipment shreds material to two-inch-minus pieces before removing ferrous and non-ferrous metals with a magnet and eddy current separator, said Jeff Gloyd, company vice president of sales and marketing. Then, manual sorters remove circuit boards. What’s left is a mixed board-copper-plastic stream sent to Janesville for further shredding and sorting, he said.
The equipment has reduced the number of shipments URT has to make from Texas to Wisconsin, driving cost savings. Shredding materials and pulling metals out allows URT to send denser loads weighing up to twice as much as unprocessed equipment, he said.
Gloyd noted the stream of scrap electronics is morphing, with a growing prevalence of small, lightweight devices containing batteries. The evolution necessitates smaller facilities that use shredding and sorting equipment and are staffed with fewer people, he said.