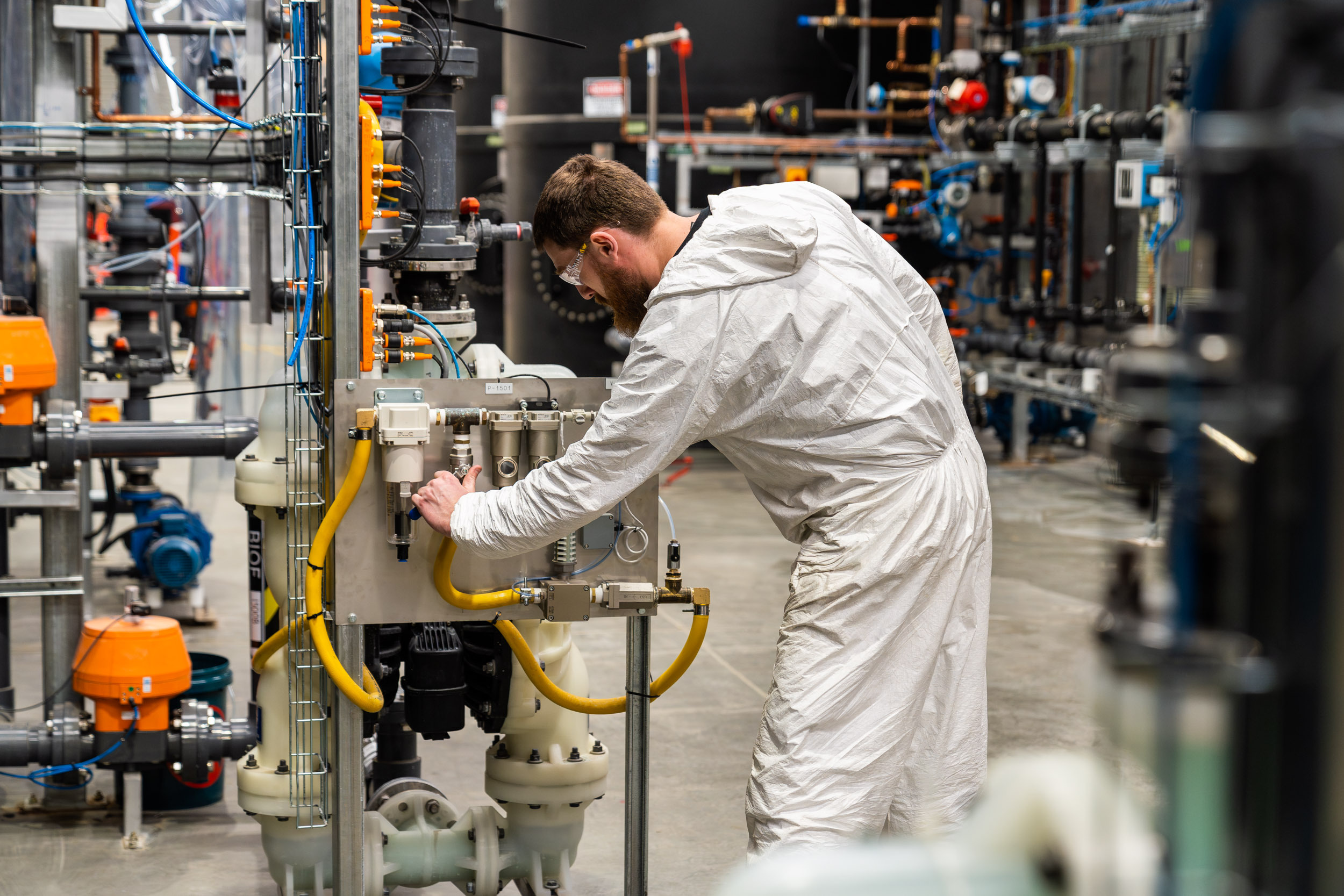
Mint’s Australian processing plant is the company’s first commercial-scale operation, and it’s now bringing that hydrometallurgical processing technology to North America. | Courtesy of Mint Innovation
After several years commercializing its technology, Australia-based hydrometallurgical processing company Mint Innovation is getting ready to build its first U.S. facility, which will provide an outlet for various grades of circuit boards.
Will Barker, CEO and co-founder, launched the company in 2016 with a goal to recover gold and other metals from waste streams or mining residues, not through smelting but through the use of various solvents.
“Very quickly, we realized that applied quite nicely to e-waste in particular and so started scaling the technology with that in mind,” Barker said.
It began proving out its concept with a pilot plant, which raised the capital to fund a demonstration plant in Auckland, New Zealand, that opened in 2019. That, in turn, raised enough capital to build a commercial prototype plant in Sydney, Australia, which completed construction and was commissioned last year.
Mint has been ramping up production there throughout 2024, currently at 3,000 metric tons per year of capacity, and now it’s gearing up for North America.
“We’ve learned a lot of lessons needed to start deploying that elsewhere,” Barker said. “And we are now ready to pull the trigger on the next deployment, which is going to be the U.S. in the not-too-distant future.”
Process produces ‘low-carbon metals’
Mint employs a hydrometallurgical process with a solvent that can go into a dissolved metal solution and act as a sort of sponge, Barker said, to selectively concentrate gold from waste streams that contain many different metals.
“The whole point of the technology is that we are able to downscale to the size where we can actually deploy regionally,” Barker said. He envisions small Mint facilities capable of serving a region of 300 to 600 miles, providing a small-footprint alternative to shipping materials out of the country for commodity recovery.
“What that enables is you’re able to serve businesses locally, you’re able to return metals back into the local economy, so proper, actual circularity,” Barker said. “And you’re able to compete with the smelters in a transparent and local way.”
Mint’s hydrometallurgical process would take in the same materials that would otherwise go for smelting. It dissolves the metals, uses a patented biotechnology to recover the gold and other precious metals, and uses conventional electrochemical processing to recover copper, tin, silver and other base metals.
At its current plant in Sydney, Mint sells the output metals locally. Barker noted one selling point for Mint’s metals is that they are processed with low-carbon technology.
“There is potential for selling them at a premium,” he said. “Our vision is that they are truly circular, so they are going back into the same electronics from whence they came. We’re working with a number of OEMs as to how to get them back into their supply chains.”
Multiple US facilities planned in near future
Barker anticipates building multiple U.S. plants that are similar or slightly larger in scale compared to the Sydney facility, at 4,000 or 5,000 tons per year, since “it’s a bigger market,” he said.
Barker likened the appearance of a Mint facility to a microbrewery, with various holding tanks, pumps, pipes and filter presses throughout. A 4,000-ton-per-year plant will be housed in a roughly 50,000- to 60,000-square-foot warehouse, he said. That small footprint is important given the company’s goal to do local processing.
“The waste streams are produced in urban environments, so we want to slide our plants into those same urban environments and recover the value locally,” he said. “That means you basically have to slide it into an existing warehouse in a city.”
Location details are not finalized yet, but he floated the possibility of building three to five U.S. facilities “in the near term.” Barker said he hopes to announce the first U.S. location before the end of this year, to develop that facility throughout next year, and to have it be operational by the end of 2025.
As part of the growth strategy, Mint in August hired Jason Price as chief operating officer. Price brings significant experience in the e-scrap and ITAD sectors, previously holding positions at Sims and Synergy Electronics Recycling, as well as at Camston Wrather, a company also working on hydrometallurgical e-scrap metals recovery.
In an interview, Price said several points about Mint’s process drew him to the company, including the traceability inherent to Mint’s technology. The company processes circuit boards in 3,000- to 4,000-pound batches, he explained, and Mint can trace the gold from those boards to that specific batch.
“So if a manufacturer says, ‘Here’s X number of boards,’ that gold from that particular batch can go back to that company,” he said.
Mint will not be dismantling devices itself and instead will be looking to buy circuit boards from e-scrap firms. The company can take in a variety of board grades but will shy away from the lower-grade boards found in TVs, for example.
“P4 motherboard and above is where we want to be on the precious metals, the gold content,” Price said. “We can take in any level above that.”