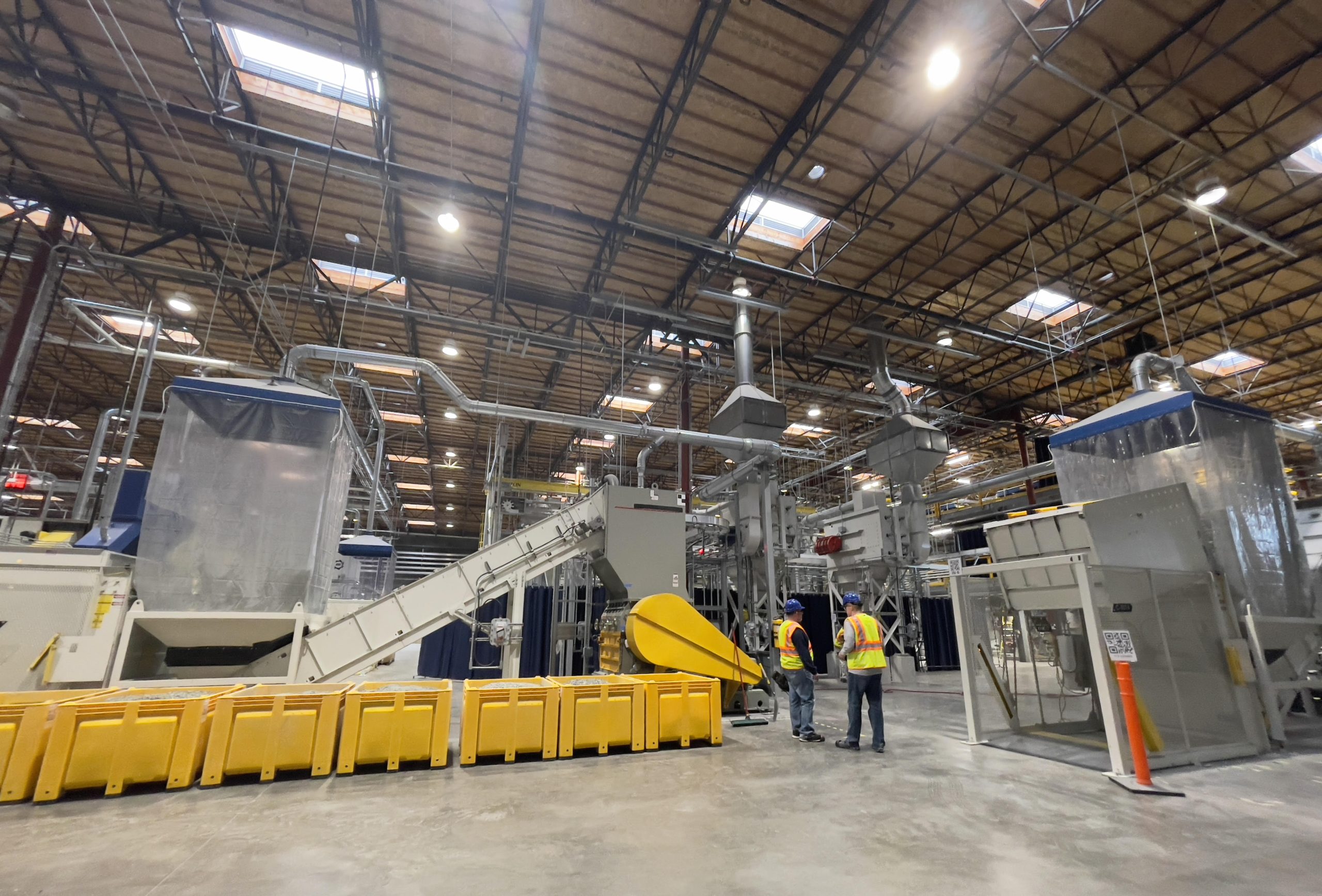
Camston Wrather’s aggregation sites currently handle about 25 million pounds of material each year, a number the company aims to triple by 2024. | Courtesy of Camston Wrather
Camston Wrather, a company with a unique process for extracting metals from printed circuit boards, announced it is planning to grow and expand aggressively across the U.S., after years of keeping a relatively low profile.
Based in the San Diego-area city of Carlsbad, Calif., Camston Wrather specializes in intermediate processing of printed circuit boards (PCBs), with its system producing a precious metals-rich fraction, a fraction with various other valuable metals, and a fraction of polymers that can be recycled.
The technology is a mechanical process that involves water, and it does not use high heat, pressure or acids, the company’s CEO, Dirk Wray, told E-Scrap News ahead of Camston Wrather’s official ribbon-cutting in April.
“We reuse everything and we have markets for everything,” he said. “We have no nasties here. That’s what really makes us very unique.”
Developing the technology
Originally founded in 2014 by Mark Evans, who is now deceased, and Aaron Kamenash, who remains the company’s chief innovation officer, Camston Wrather has its roots in the chemistry used to extract precious metals from mining tailings without using chemicals such as cyanide. After some time, they shifted their R&D focus to PCBs, developing the intellectual property that’s now been commercialized, Wray said.
There is no person named “Camston Wrather” associated with the company. “Wrather” refers to the last name of an early financier for Walt Disney (when he was younger, Evans worked for Disney, so he knew a lot about the company’s early history), and “Camston” is completely made up, Wray said. The goal was to create a company name that didn’t sound overly technical.
Wray said the metals recovery technology used at the 115,000-square-foot Carlsbad facility was developed in house. The front end of the shredding system is fairly standard, with size reduction, magnetic and optical sorting equipment, Wray said.
But instead of shipping the shredded PCBs to a smelter, Camston Wrather uses its own trade secret-protected process to liberate the metals (the company is working to write and submit applications for patents to cover portions of what’s currently secret intellectual property).
The metals outputs, which have a sand-like consistency, are shipped to refiners to produce pure metals. One output of Camston Wrather’s process is a concentrate with gold, silver and palladium, and the other has a mix of metals, including copper, nickel, tin, rare earths and more. The process works particularly well on mid- and high-grade boards.
“Our concentrates are quite a bit more refined than a smelter’s are,” Wray noted.
He said the company’s process, which is underwritten by the VERRA methodology for calculating environmental impact, generates voluntary carbon credits. Wray emphasized the data could help publicly traded companies as the U.S. Securities and Exchange Commission (SEC) looks to require auditors sign off on their greenhouse gas generation metrics.
Plans for Midwest, East Coast plants
In addition to its “green smelter” in Carlsbad, which has been operational since late last year, Camston Wrather has seven aggregation sites in the following states: three in Florida, one in Pennsylvania, one in Arizona, one in Missouri and one in Texas. Total company square footage is less than half a million, and the company currently has about 325 employees.
Some of the aggregation facilities also provide ITAD services for clients, Wray said. Camston Wrather in 2019 acquired its wholly owned ITAD and recycling subsidiary, Stream Recycling Solutions (SRS), which has a presence in facilities in Tampa, Fla.; Plant City, Fla.; Fort Lauderdale, Fla.; Carlsbad; St. Louis; and Phoenix. SRS has a strategic partnership with Texas Recovery Systems, which has R2-certified locations in Texas and Pennsylvania, for downstream disposal needs, according to a Camston Wrather spokesperson.
Also pointing to Camston Wrather’s data destruction abilities and device resale business, Wray emphasized the ability to provide a range of services for clients. “I think the future is walk into a major company’s door and be able to provide a full service that’s transparent,” Wray said.
In 2023, Wray estimates, the aggregation sites will handle about 25 million pounds of material, with plans to triple that in 2024.
Circuit boards are shipped to Carlsbad, which processes about 20 million pounds of PCBs a year working 14 hours a day, five days a week, Wray said. A ribbon-cutting at the Carlsbad facility is planned for next month.
That plant has also seen recent upgrades. On March 1, Boston-based Schneider Electric announced that it would be providing its EcoStruxure Power and Process solutions and services to the plant, helping to increase efficiency and decrease energy consumption. “The integrated solution provides greater visibility into their electrical system with power management, unified control, and the flexibility to easily scale, replicate and adjust as their operations grow,” according to a press release.
Meanwhile, Camston Wrather is considering installing more metals separation lines across the U.S. Demand from a Fortune 500 company is leading the company to look at installing Midwest and East Coast plants, Wray said.
He expects that in two years, Camston Wrather will have at least two more PCB processing lines, and in three years, it will have four more.
“Circularity is really becoming a real thing in this industry, and we’re happy to be part of it,” Wray said.
More stories about metals
- Australian metals company rebrands, builds Texas plant
- Project brings rare earth recovery into e-scrap facility
- Company debuts battery-containing device shredder