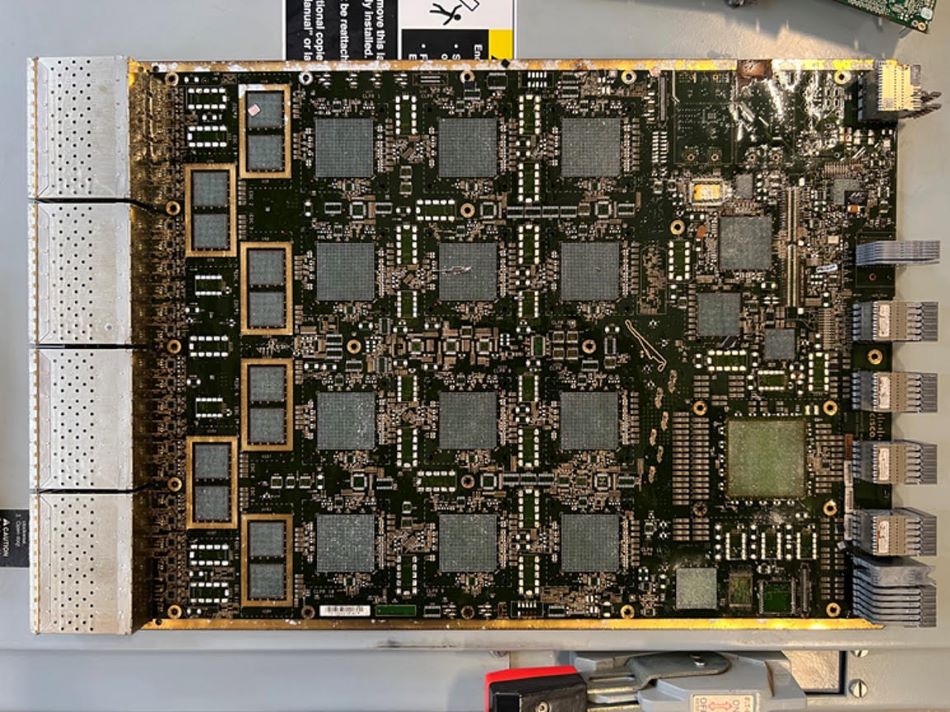
IC Recovery uses a heated oil to loosen chips from circuit boards without damaging the chips. This photo shows a circuit board with the chips removed. | Courtesy of IC Recovery
Over a decade ago, Greene Lyon Group first developed a thermofluid process for removing chips from circuit boards so the chips could be reused. “That was back in 2012; there was no chip shortage,” said Dale Johnson, CEO of Greene Lyon Group.
Fast-forward to the pandemic-era economy, with its widespread supply chain kinks, and it became an ideal time to commercialize the technology through a new company division, IC Recovery, he explained.
IC Recovery is employing a “recovery as a service” business model, through which companies, including OEMs and ITAD firms, pay a fee to have IC Recovery gently remove higher-value chips from printed circuit boards en masse. Those chips are certified to be in working order before they’re returned to the client, who can then reuse or sell them.
This approach produces chips that are cheaper and have a drastically smaller greenhouse gas (GHG) footprint than new chips, and they can be delivered in a fraction of the time, Johnson explained.
“The two factors that create pain for someone are the cost of the chip and the time that you need to get it, and we can address both of those,” said Johnson, who is also president and CEO of IC Recovery, which was formed in early 2022.
How the technology works
Headquartered in Beverly, Mass., IC Recovery has a light processing and demonstration line in a 3,000-square-foot space in Berlin, Conn., which is where the division’s engineering, design and fabrication partner companies are located, Johnson said.
IC Recovery’s process, which is protected by patents, trade secrets and its branded Chip-Renew, immerses circuit boards in a tank with an oil heated to a consistent but adjustable temperature. The oil won’t damage electronic components or absorb contaminants, so it can be reused. There will, however, be evaporation losses over time and, eventually, the oil will degrade, at which point it must be shipped out for treatment, Johnson explained.
The fluid loosens the chips from the tops and bottoms of the boards in about five minutes, he said. Staff then manually separate the chips destined for retinning/reballing, testing and certification, and reuse. The non-targeted chips are recycled. The stripped boards very rarely have any gold content, but IC Recovery can send them to a smelter for beneficial use because of their high British Thermal Unit (BTU) content, he said.
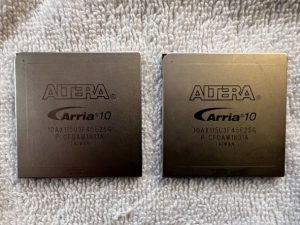
Some examples of the high-value computer chips that can been recovered by IC Recovery’s technology. | Courtesy of IC Recovery
IC Recovery’s current beta system can process 5,000 boards per month on one shift, Johnson said. The company plans to install a gamma system in February that will include more automation and will at least double processing capacity.
Benefits for clients
Johnson said IC Recovery was asked to recover chips from high-end telecom boards. The chips would have cost between $7,000 and $10,000 to manufacture, and the lead time would have been about 42 weeks, he said.
IC Recovery was able to recover the chips for the client at “a really small fraction of the original cost, and we did it within six weeks,” he said.
Of course, it’s not always cost effective to use the process. IC Recovery focuses on higher-value chips, such as higher-priced CPUs and GPUs, rather than memory chips, which aren’t generally as valuable, he said. IC Recovery has a cost-price matrix to help clients determine whether it’s worth recovering a chip for reuse/resale versus simply recycling it and buying a new one.
Lauren Roman, business strategy consultant for IC Recovery, pointed out that the service makes financial sense when dealing with larger volumes of a particular kind of chip, as opposed to only a handful of different types.
“If there’s some volume there, then the economics play out,” she said.
Economics aside, Johnson pointed to other values of reuse, such as environmental benefits. IC Recovery commissioned a study that estimated chips recovered from his company’s process have 97% fewer GHG emissions than newly fabricating chips. He pointed to a Harvard study that found “chip manufacturing, as opposed to hardware use and energy consumption, accounts for most of the carbon output attributable to hardware systems.”
“Chips typically have a useful life well beyond that of the equipment they’re originally in,” Johnson said. “So disposing of populated circuit boards in the typical fashion of smelting them for precious metals destroys many years of valuable remaining chip life.”
He also pointed out national security benefits from the technology. Some government electronics, including pieces of older military hardware, rely on legacy chips that are manufactured overseas.
The CHIPS and Science Act of 2022, which was passed by Congress and signed by President Biden last summer, includes $2 billion in incentives for domestic manufacturing of legacy chips used in automobiles and defense systems, according to a White House fact sheet.
“The equipment that we recover the chips from is already in the U.S.,” he said. “Those chips are already domestically sourced.”