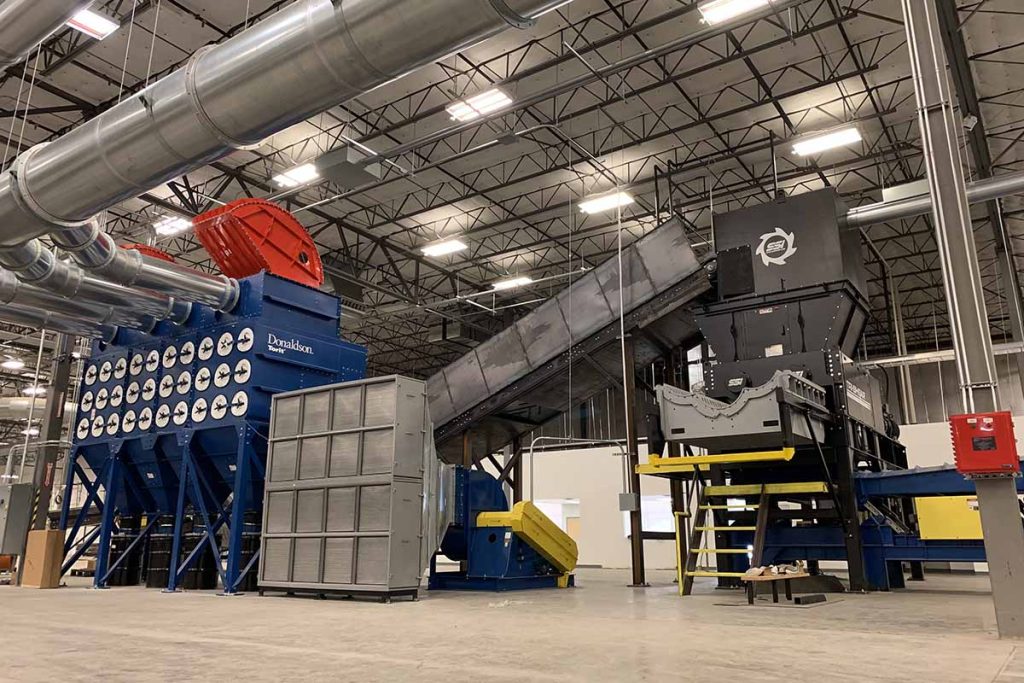
URT installed a new shredding and separation system at its newly occupied 198,000-square-foot facility in Fort Worth. | Courtesy of Universal Recycling Technologies (URT)
Universal Recycling Technologies has invested nearly $7 million in a processing facility that will greatly expand the company’s commodities recovery and electronics refurbishment capabilities.
URT recently opened a 198,000-square-foot leased space in Fort Worth, Texas, replacing a 66,000-square-foot facility in the same city. Among the improvements is a new shredding and separation system.
“The sortation equipment is top of the line and reduces labor required to sort material, and we’re getting very high-quality outputs on the circuit boards, the aluminum, the steel, the plastic,” said Ray Zielke, URT’s vice president of sales and marketing.
In addition to an advanced shredding and separation system, the new Fort Worth facility sports improved CRT dismantling stations and an optimized electronics refurbishment and resale setup.
The Fort Worth facility is one of four for URT, which is based in Janesville, Wis. and has additional facilities in Janesville; Clackamas, Ore.; and Dover, N.H.
Ken Thomas, president of URT, told E-Scrap News the company began moving into the new Fort Worth space around June. Utility company delays in acquiring electrical transformer equipment – a widespread problem – delayed the opening by several months.
URT bought and installed a new SSI T140 shredder, magnetic sorting belt, Javelin eddy current separator and TOMRA optical sorter. The company also moved its old two-shaft shredder to the new plant, where the equipment is now recycling solar panels.
The new shredding and sorting line has a capacity of about 17,000 pounds per hour, Thomas said. In comparison, the old line was processing about 30,000 pounds per day, and it had an undersized eddy current separator and no sorter.
In setting up the new equipment, URT put a lot of focus on removing plastic film from other e-plastics in the stream of shredded flat-panel displays, Thomas said. That separation increases the value of the e-plastics.
The T140 shredder also has a screen, ensuring overly large fractions remain in the shredder until they’re size-reduced to the proper size, Thomas said.
URT is a major outlet for CRT glass, which it processes into a powder used in ceramic tile manufacturing. The new facility continues to recycle leaded glass into the powder. But Thomas noted that the CRT demanufacturing stations now have conveyors that carry metals removed from CRT displays – steel bands and shadow masks – straight to the shredder.
The newly occupied building, which is fully climate controlled, also has 15,000 square feet dedicated to refurbishment, he said. In the old plant, equipment that staff deemed refurbishable was boxed up and carried into open-air offices for processing.
“Now we have a good flow setup at the ITAD area – conveyor systems and areas for the chip harvest or pulling out motherboards or wiping hard drives,” Thomas said. “We have actual stations set up that are in line with production.”
Thomas said the total capital investment of the new plant, not including the lease commitment, was nearly $7 million.
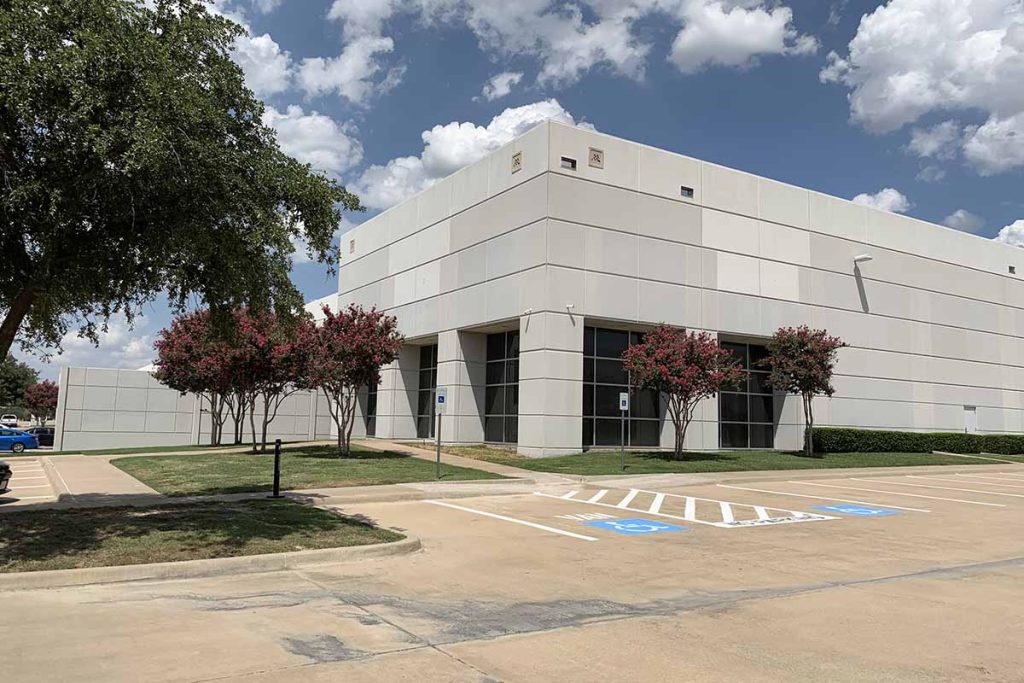
URT is initially looking at processing about 30,000 pounds per day of solar panels. | Courtesy of Universal Recycling Technologies (URT)
Pursuing solar panel, e-plastics opportunities
Thomas and Zielke said URT is now using the old shredding system in a solar panel recycling line. Thomas said there was demand among URT’s existing customer base to responsibly recycle their end-of-life solar panels.
Zielke said URT is initially looking at processing about 30,000 pounds per day of solar panels. He said he couldn’t disclose exactly how URT will recycle the panels, but he noted that it won’t mimic industry-standard processes. “[We’re] going to have a different approach than anyone else that we know in the market,” Zielke said.
Overall, Thomas said, the new facility and equipment helps URT overcome the size constraints presented by the old plant. “The Texas market is big enough to support this investment,” he said.
The new space and capabilities also allow URT to perform recycling steps on computer peripherals that, previously, the company relied on downstream companies to handle.
“It’s just a matter of keeping our own destiny in our own hands,” Thomas said. “Processing it in-house just takes a lot of that cost out, the transportation cost, the margins that the downstreams justifiably want.”
More investments are planned. A couple of years ago, URT installed an e-plastics sorting system at its Janesville headquarters plant, allowing the company to improve the quality of plastic fractions and recover any metals that would otherwise be lost to the e-plastic downstreams.
Zielke also said URT plans to install a similar float-sink system at the Fort Worth plant.
“That is a primary goal for 2023,” he said, “because URT is trying to generate and create a plastic product that’s able to stay domestic and hopefully eliminate our need to move those plastics overseas.”
More stories about processors
- New ITAD firm launches, acquiring two processors
- Makor ERP to incorporate ESG reporting into platform
- Australian metals company rebrands, builds Texas plant