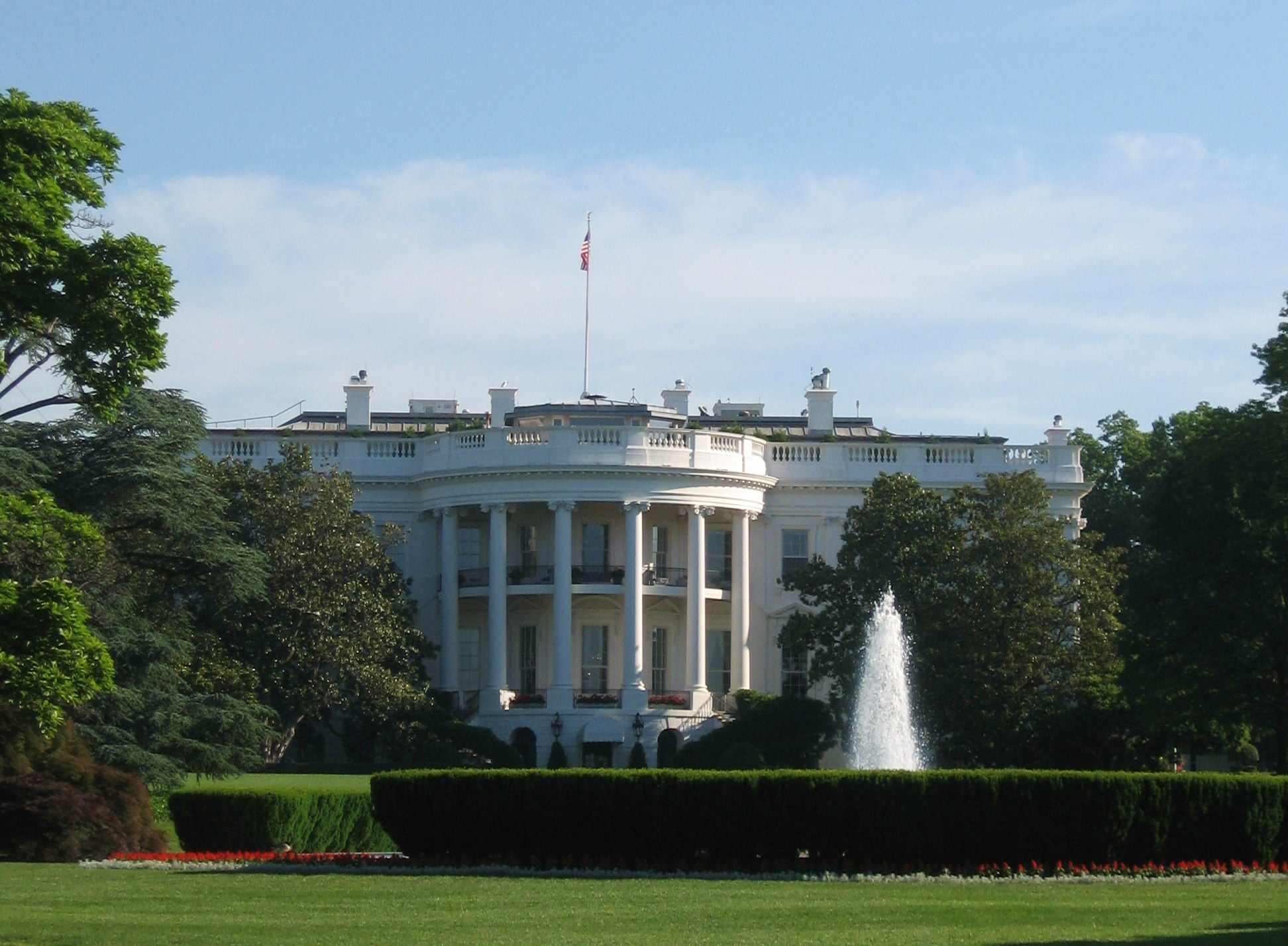
Donald Trump’s return to the White House will likely bring far-reaching changes to the recycling system, experts say. | Dan Holtmeyer/Resource Recycling Inc.
This article appeared in the December 2024 issue of Resource Recycling. Subscribe today for access to all print content.
The clear victory of Republicans across the branches of U.S. government could affect the municipal recycling world in a number of ways. It’s early, but some signs from the past — and some recent analysis from industry observers — offer a glimpse of what’s to come.
In the Nov. 5 general election, President-elect Donald Trump received 312 electoral votes to Kamala Harris’s 226, Republicans won control of the U.S. Senate with 53 seats to Democrats’ 47, and Republicans have secured a majority of U.S. House seats. The trifecta gives the party broad power to enact its policies.
For recycling stakeholders, some of the impacts will be general: Tariffs, tax cuts and other economic policies would undoubtedly filter down to affect the recycling sector, as with virtually every other industry. Those policies could be similar to those proposed and enacted during Trump’s 2017-2021 administration.
For instance, Trump has said he’ll impose tariffs on Canada, China and Mexico, the country’s three largest trading partners. That policy hearkens back to the Trump administration’s previous trade war with China, which affected recycling in the form of increased costs for machinery components and basic facility needs like baling wire, on top of the tariffs’ broader impact on the economy.
President Joseph Biden later kept and expanded some of those tariffs, but not on the level of the measures Trump has proposed. Industry groups such as the Recycled Materials Association already shared an analysis suggesting the new tariffs Trump has described would “negatively impact the U.S. economy.” And retailers like Walmart have said publicly that prices will likely go up with new tariffs, according to Forbes and other outlets.
Meanwhile, the tax cuts of 2017 were lauded at the time by industry groups representing recycling interests, and among new tax proposals, the Trump administration is expected to extend the cuts, some of which were set to end at the end of 2025.
In some ways, the lack of federal recycling policy could insulate the plastics and chemicals sector from major policy impacts.
“U.S. states have been the traditional leaders in passing policies to improve recycling and reduce plastic pollution,” said Kate Bailey, chief policy officer with the Association of Plastic Recyclers, in a written statement. “We expect that to continue and to be strong for many years to come because polls show there is widespread support to improve recycling and reduce plastic waste. APR’s policy focus has been at the state level, and we will continue to prioritize working with state legislatures to improve recycling collection and increase the use of recycled plastics in place of virgin feedstocks.”
APR owns Resource Recycling, Inc., publisher of this magazine.
“Spending public funds for the sake of sustainability, rather than efficiency, is most likely in the past,” said Bailey Robin, cofounder and CEO of recycled commodity trading platform Matium. He added that it would be important to see how tariffs may affect the industry.
Similarly, in a presentation at Pack Expo before the election, Rebecca Marquez, director of custom research at PMMI: Association for Packaging and Processing Technologies, said the trade association did not anticipate any federal packaging extended producer responsibility legislation because the U.S. is too fragmented, so it will likely remain state responsibilities.
The Plastics Industry Association — along with the Recycled Materials Association, Radius Recycling, Eastman and Dow — was among more than 600 business leaders that signed a Nov. 5 letter from the National Association of Manufacturers pledging to work with whomever was elected.
Meanwhile, the Aluminum Association, U.S. Chamber of Commerce, American Beverage Association, The Recycling Partnership, World Wildlife Fund and dozens of other industry and advocacy organizations on Nov. 19 urged Congress to pass two bipartisan recycling bills before the end of the year — before the new federal government arrives, though the groups didn’t note this explicitly.
The Recycling Infrastructure Accessibility Act and the Recycling and Composting Accountability Act would enhance federal recycling and composting data and provide more grants, particularly to underserved areas. They’ve easily passed the narrowly Democratic Senate but not the narrowly Republican House.
“More recycling is good both for the planet and for the broader manufacturing economy,” the organizations wrote to Congressional leaders in both chambers. “Together, these bipartisan bills would advance the nation’s recycling capabilities, support a robust and circular economy, and help secure critical domestic supply chains.”
Industry stakeholders may be anticipating less interest in recycling-related legislation in the upcoming legislative landscape, said David Biderman, a waste and recycling consultant and former trade association president.
“The clock is running out on the 118th Congress, plus the results of the November elections will usher in an administration far less concerned about recycling than the Biden Administration,” Biderman said. “The Republican-led House and Senate that will convene in January 2025 will have many higher priorities than this legislation.”
Potential EPA impacts
Recycling policy is largely set at the state and local level, and programs are mostly overseen by municipal governments. But the federal government does plenty of work collecting data and facilitating conversations to advance materials recovery.
Those efforts are always subject to change when there are leadership transitions in Washington. The early efforts of the prior Trump administration to significantly reduce the EPA’s budget offer clues about what could be coming down the line.
Back in early 2017, the Trump administration proposed cutting EPA’s budget by 31%, prompting fears among recycling stakeholders that the agency’s longstanding Sustainable Materials Management work could grind to a halt. Recycling lobbyists sought to defend the programs, noting both their economic and environmental benefits. In the end, after working its way through the U.S. House and Senate — both of which were Republican-controlled — the budget was revised to remove many of the drastic cuts.
One longtime recycling industry stakeholder told Resource Recycling that the state-level emphasis could become even more pronounced amid the new political environment.
“Should residential recycling not be a priority at the federal level, one way it can prosper is for states to grab the bull by the horn and legislate it through mandates such as EPR or container deposit laws,” said Myles Cohen, founder of Circular Ventures and previously president of Pratt Recycling.
Trump announced he plans to nominate former Rep. Lee Zeldin of New York as EPA administrator. Zeldin served in the House of Representatives from 2015 through 2023 and has been an outspoken Trump ally over the years.
“Lee, with a very strong legal background, has been a true fighter for America First policies,” Trump wrote in a statement on social media, noting that Zeldin “will ensure fair and swift deregulatory decisions that will be enacted in a way to unleash the power of American businesses, while at the same time maintaining the highest environmental standards, including the cleanest air and water on the planet.”
Zeldin voted in line with the League of Conservation Voters 14% of the time, according to the organization, indicating relatively low support for pro-environment measures. A couple of exceptions were the votes he cast to increase regulation on PFAS.
Grants in jeopardy
Although Trump has not specified plans regarding recycling, Trump said in a September speech to the Economic Club of New York that he would “rescind all unspent funds” from the Inflation Reduction Act, which has helped greenlight such projects as Eastman’s second U.S. chemical recycling plant in Longview, Texas.
“Eastman is already under award contract with the DOE for our project in Texas,” said spokesperson Kristin Parker. “We are working together closely and don’t believe the change in White House leadership will impact our award.”
In March, the project was awarded up to $375 million in funding and was to begin negotiations with the U.S. Department of Energy. During negotiations, the Office of Clean Energy Demonstrations, which administers the Industrial Demonstrations program that selected Eastman, and the recipient finalize the project scope and the proposed budget. “The complexity of the project, the selectee’s responses, and OCED’s reviews will all impact the negotiation timeline,” according to the office’s website.
“When it comes to the reliability of the grants, well, we’re in a new political world, so I’m not going to predict what happens,” Eastman CEO Mark Costa said in a Nov. 21 investor call. Eastman’s investments help work toward reshoring U.S. production and building a local economy, which is “in line with the current agenda of the incoming administration.”
Costa added that programs funded by the IRA and the 2022 CHIPS and Science Act, which incentivizes U.S. manufacturing especially for semiconductor chips, “are incredibly important for our national security.”
In an August letter to House Speaker Mike Johnson, 18 Republican lawmakers said, “As Members of the House Republican Conference, we write to urge you to prioritize business and market certainty as you consider efforts that repeal or reform the Inflation Reduction Act.”
They continued: “Prematurely repealing energy tax credits, particularly those which were used to justify investments that already broke ground, would undermine private investments and stop development that is already ongoing. A full repeal would create a worst-case scenario where we would have spent billions of taxpayer dollars and received next to nothing in return.”
Treaties could be tabled
Recycling stakeholders should anticipate the U.S. pulling back from involvement in global regulatory efforts, according to law firm Beveridge & Diamond.
“Prepare for the withdrawal of engagement on international environmental and waste treaties, as the Trump administration prioritizes domestic development, tariffs (and potential restrictions on imported goods), and increased exports of domestic natural resources,” the firm recently wrote. “This includes the United States’ withdrawal from the Paris Agreement and implications to ongoing international conversations around global emissions reductions and the regulation of plastics.”
While the analysis didn’t mention the treaty by name, the implications would likely extend to the Basel Convention, which regulates the movement of hazardous waste materials around the world, and in recent years has expanded to cover shipments of mixed scrap plastic. The convention will expand its regulation of end-of-life electronics beginning next year.
The U.S. remains one of the only non-party countries to the Basel Convention, and that fact has increasingly shut U.S. companies out of the global trade of recycled materials. Non-party countries are prohibited from trading materials that are regulated under the convention with party countries.
The Beveridge & Diamond analysis touched on the U.N.’s in-development global treaty on plastics, which the U.S. has engaged with. Notably, the U.S. this year pivoted on key controversial components on the draft treaty to support plastics production limits. The abrupt shift from previous opposition to such measures garnered a strong reaction from the plastics industry and cautious optimism from environmental groups.
In a Nov. 15 media briefing held by Break Free From Plastics, Sarah Martik with the Center for Coalfield Justice, said members of the U.S. delegation “confirmed they were not supporting” such caps anymore and “instead will rely on market signals and individual countries’ signals to set these caps and timelines for us.”
Meanwhile, back in the U.S., one industry association says the federal shift could affect the landscape of voluntary industry commitments as well. In a statement, the U.S. Plastics Pact said its work to achieve recycling targets occurs “independent of shifting federal policies.” But the group noted “critical gaps remain at the federal level that limit our ability to fully achieve these targets, regardless of the administration in power.”
The Pact added it doesn’t anticipate building up federal plastics recycling policies will be a priority for the next administration, but it emphasized that “plastics recycling is a bipartisan issue, and we remain committed to advancing the conversation within the supply chain.”
Marissa Heffernan and Dan Holtmeyer contributed to this story.