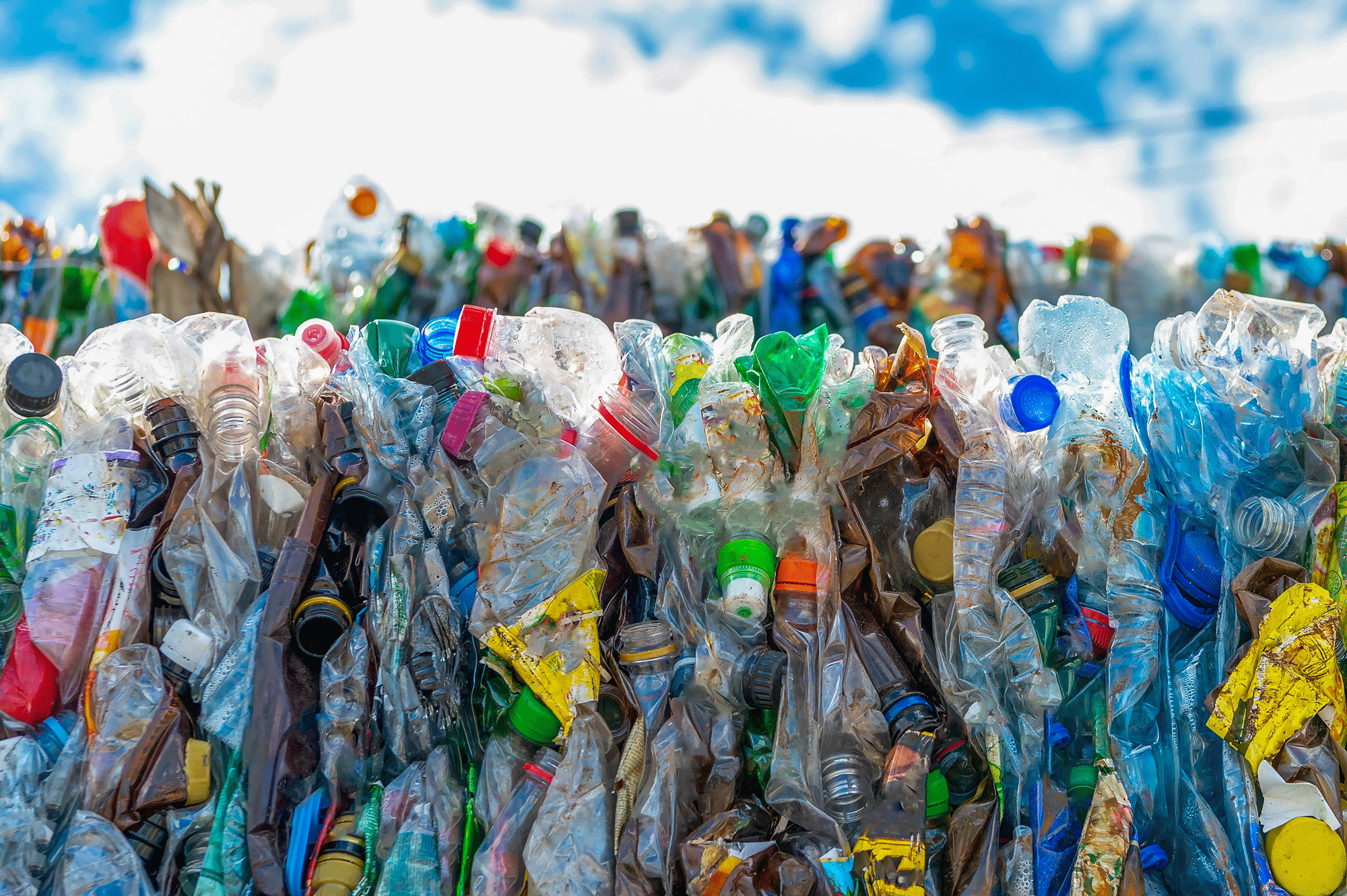
Evgenii Panov/Shutterstock.
This article appeared in the December 2024 issue of Resource Recycling. Subscribe today for access to all print content.
Even without the major hurricanes or before the election season, 2024 was a year of change for the recycling sector, with new players coming to the fore, old players building out their footprints and an ever-clearer view of the industry’s shortfalls and successes.
Nonprofits, communities and multibillion-dollar corporations alike consolidated, partnered and tested new ways to recycle materials and to explain the recycling system to its users. Extended producer responsibility, the right to repair and other policy ideas advanced on some fronts but not others. And on a global scale, companies and nations grappled with the reality of omnipresent plastics.
Like re-reading an old diary, we’re spending a few pages looking back at some of the year’s biggest news and trends to help make sense of where everything landed — and to get a glimpse of what might come next.
Unmasking fire hazards
The year began with a January report from the National Waste and Recycling Association and RRS estimating that more than 5,000 fires occur annually at recycling facilities, many likely linked to wayward lithium-ion batteries inside recycling streams that can incinerate everything around them when crushed or damaged.
“Basically they’re like a flower spinner you’d see on the Fourth of July, but they’re heavier and they’re burning at about 700-plus degrees,” said Matt Tracy, site superintendent for the Metro South transfer station outside Portland, Oregon, during a February forum hosted by the Association of Oregon Recyclers.
The study found that the rate of catastrophic losses rose by 41% over the last five years, and the cost to insure facilities has followed suit, rising to as much as 50 times previous costs.
Facilities like Tracy’s across the country have adopted several tactics for dealing with and preventing these fires, including burying the batteries in CellBlockEX, a dry medium made from recycled glass and specifically designed to extinguish or suppress lithium-ion battery fires, and enlisting FireRover, the remote fire monitoring and suppression system.
This year the federal government awarded hundreds of millions of dollars toward lithium-ion battery processing operations to boost their capacity. And multiple technology companies have also turned to the X-ray band of the electromagnetic spectrum, aiming to pierce through MRFs’ incoming boxes and bottles to flag misplaced batteries and other hazards before they catch fire.
A young company called BinIt in January announced that it had received $6.4 million in seed financing for its imaging system combining cameras, X-rays and artificial intelligence, for instance. In the spring, Call2Recycle and Electronic Distributors International installed a similar battery-sorting system in Ontario, one of four of its type in the world. And Battery Detection Solutions spoke with Resource Recycling in November about its own X-ray scanner, which could eventually be adapted from MRFs to collection trucks.
“The only way to eliminate the chance of a fire is to make sure the batteries can’t get in,” said Rich Cisek, Battery Detection Solutions’ founder and CEO. “Even if some magic battery comes out tomorrow where people are like, ‘Hey, look, it doesn’t catch on fire anymore when you shred it,’ we’re still going to have a decade and a half of risk around the stuff.”
State policy changes
Minnesota in May became the fifth U.S. state to pass extended producer responsibility for packaging, joining the ranks of California, Colorado, Maine and Oregon. It created a framework for manufacturers to contribute to increased recycling of their products over time and passed along party lines, with Democrats in favor.
“The burden of managing this ever-growing deluge of packaging waste currently falls on local governments — and taxpayers,” State Rep. Sydney Jordan, who sponsored the original bill, said in a written statement at the time. “Today’s bill takes steps to ensure the producers of this waste are paying their fair share.”
The success followed several months of negotiation and collaboration among a wide variety of industry stakeholders, including nonprofit MRF Eureka Recycling and Ameripen, an industry group representing packaging producers that hadn’t supported such a policy until Minnesota’s final version.
Other narrower EPR policies also passed this year, including for textiles in California and electric vehicle batteries in New Jersey, both firsts in the U.S. And work continued on previously passed EPR bills, with California, Colorado, Maine and others deciding annual recycling targets, producer responsibility organizations and other details. EPR attempts were unsuccessful, meanwhile, in still other states, including Michigan and New York.
On the e-scrap side, Oregon and Colorado both passed right-to-repair legislation last spring, require electronics manufacturers to allow independent repair shops and consumers access to the parts, tools and documentation needed to fix devices. While Oregon and Colorado were the fourth and fifth states to do so, respectively, they were the first to ban the use of software to ensure a device will only operate with specific individual parts, or parts pairing, which can interfere with third-party repairs or with device functionality afterward.
On the international stage
The U.N.’s Intergovernmental Negotiating Committee on Plastic Pollution assembled global leaders multiple times this year to hash out a global treaty on the subject, with the fifth meeting set for Nov. 25 through Dec. 1 in South Korea.
INC-5 would be the last chance the delegates have to meet the deadline of having treaty text ready to present to a Conference of Parties by the end of 2024, a finish line that was set in a March 2022 vote. Delegates have broadly agreed on the need for mandates on product design, composition, performance and EPR, though there have been disputes over production caps and other areas.
Next year will also herald wide-ranging impacts from another global agreement, the Basel Convention, which controls the international trade of a wide array of electronics and their contents, such as plastics. The U.S. is one of the few countries that is not party to the convention, meaning that starting Jan. 1, U.S. e-scrap companies will no longer be able to export their output to virtually any overseas buyers. It’s a huge change that IT asset disposition companies have spent the year figuring out how to handle.
“It really has become the de facto agreement for the circular economy,” said Paul Hagen, an attorney with Beveridge & Diamond and a longtime Basel expert, speaking during a panel at the ISRI2024 conference in Las Vegas in April.
Aiming high, and adjusting
Disappointment was another theme of 2024, with Unilever, Colgate-Palmolive, PepsiCo and other major consumer goods makers announcing they’d fall short of their 2025 goals for recycled content usage and other measures.
Post-consumer resin production needs to increase as much as fivefold to meet those goals, according to a report this summer from RaboResearch, part of the Dutch financial services company Rabobank.
Bloomberg’s latest edition of its Circular Economy Company Ranking, an annual publication tracking corporate sustainability pledges, in October found widespread “difficulties in sourcing sustainable feedstock and materials, and a lack of infrastructure for sorting and recycling — all against the backdrop of rising costs.”
As a result, brands likely will shift their focus more broadly to carbon emissions targets rather than putting plastic usage under the microscope, RaboResearch wrote. And Bloomberg noted that, in lieu of adequate mechanical recycling capacity, many firms are banking on chemical recycling.
Chemical recycling questions
Chemical recycling goes beyond conventional mechanical recycling, breaking post-consumer plastics down into their basic molecular components for remanufacture, as opposed to physically chopping them into flakes for melting.
The technology started the year on a defensive footing, with The Recycling Partnership in February calling for more evidence of its benefits to people and the environment. Maine passed legislation classifying it as solid waste processing rather than recycling in March, and the National Recycling Coalition proposed a similar draft policy in the summer.
“Recycling has always evolved and changed,” and chemical recycling is just another innovation “responding to the reality that some … plastics in the current packaging stream are difficult or unable to be recycled mechanically,” TRP said in a position statement on its website. “Change is good, but it needs to be planet-positive, transparent, and measurable.”
Petrochemical companies have nonetheless poured hundreds of millions of dollars into chemical recycling technologies, calling it a game-changer that can solve the plastic problem. Eastman early this year announced plans to build its second chemical recycling facility in Longview, Texas, for example, with up to $375 million from the U.S. Department of Energy, though the election has raised questions over that support.
Energy giant ExxonMobil recently announced it would triple its U.S. chemical recycling capacity in Texas. Shortly after that announcement, Cyclyx, which supplies plastic scrap to mechanical recyclers as well as chemical recyclers such as ExxonMobil and LyondellBasell, announced it would proceed with its second plastic processing center in Texas, too.
Skepticism around chemical recycling’s promise continues to dog the industry, however. A November report from Zero Waste Europe, based in Belgium, called it “partial recycling” and said successful commercialization “will require huge financial and regulatory support and time.”
A clearer view going forward
The past year brought a slew of studies and reports that, taken together, helped fill in the map of the recycling landscape across the country.
Three-fourths of recyclables are lost at the household level, even though 73% of all U.S. households have recycling access, according to a January study from TRP that estimated the residential recycling rate is 21%. The “State of Recycling: Present and Future of Residential Recycling in the U.S” report pointed to a lack of access to recycling services and a lack of education and communication as major culprits.
TRP and GreenBlue in September followed up with new online data highlighting recycling program acceptance rates for 50 different material types across the country, using local recycling program data that represents nearly all of the U.S. population. They aim to update the U.S. Community Recycling Program Acceptance Data twice yearly.
As Resource Recycling reported in January, a study from Eunomia Research and Consulting also found that nine of the 10 states with the highest recycling rates have deposit return systems. Deposit states account for 27% of the U.S. population, according to the study, but provide more than half of all aluminum cans, glass bottles and PET bottles recycled in the country. Other studies this year found deposit recycling rates are falling slightly in those states as well, which some observers said meant the systems need bigger deposits and other changes.
Among several material-specific studies, a revised methodology from the American Forest & Paper Association put the 2023 recycling rate for paper at 65-69% and cardboard at 71-76%. That’s significantly lower than previous AF&PA reports and more in line with estimates from Bloomberg Intelligence and Circular Ventures, which disputed AF&PA’s figures for years — including in these pages.
Marissa Heffernan, Antoinette Smith and Colin Staub contributed to this report.