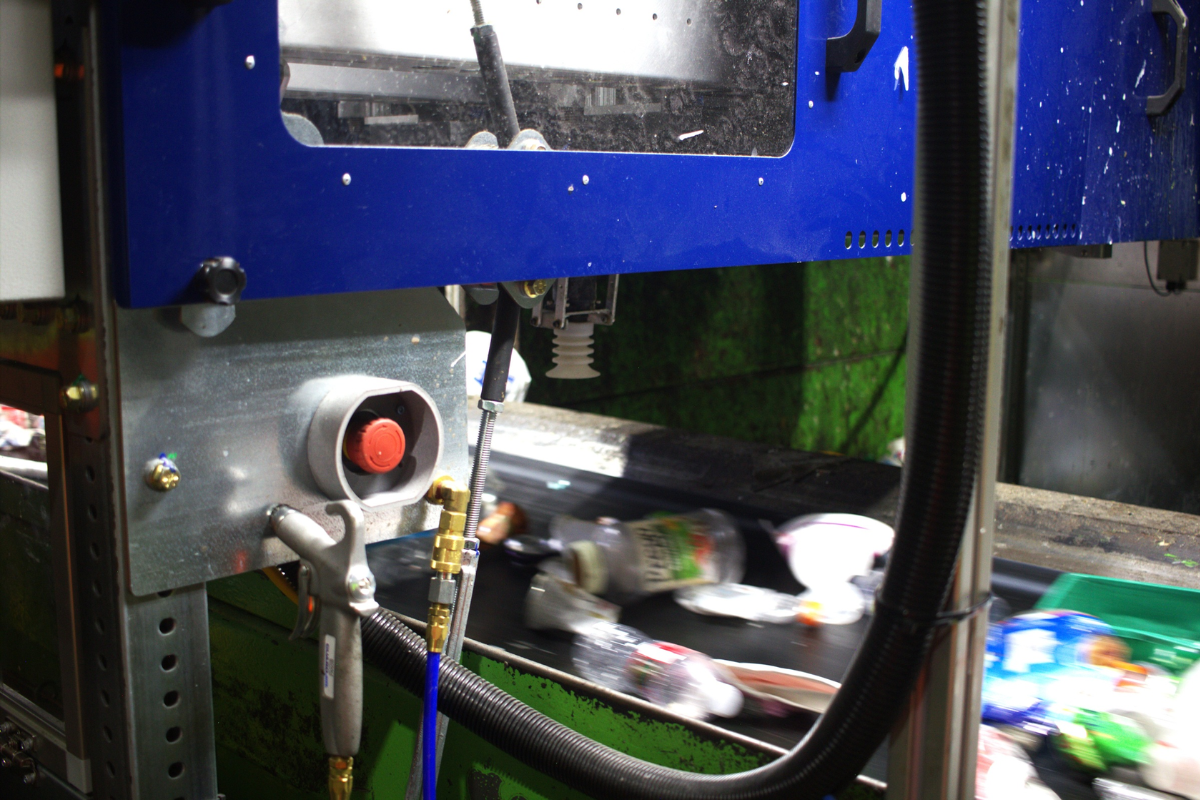
A Glacier robot positioned on the sorting line at Seattle’s King County MRF. | Photo by Colin Staub
A Seattle-area sorting facility operated by Recology has installed imaging and sorting equipment supplied by Glacier, adding another major MRF to the company’s two-dozen customers. Glacier also announced it has raised additional capital that CEO Rebecca Hu-Thrams said will help the company grow further and faster.
Glacier and Recology, both San Francisco-based companies, on April 28 announced the developments and hosted a demonstration event at the Seattle facility, a 300-tons-per-day MRF that opened in 2014.
Glacier has so far installed four robots at the MRF, where they’ve sorted for a combined 2,800 hours and diverted 14 tons of recyclables during their initial start-up period. One key area for the robots is on the plastic sort line, where they’re targeting HDPE containers.
Recology CEO Sal Coniglio told Resource Recycling the company’s facilities were designed anywhere from 10 to 30 years ago, when the waste stream looked much different. In many cases, they weren’t built to have people safely in areas where manual sorters would be beneficial, he noted, but the facilities still need to remove that contamination.
“Robots have been great for us to position them where it’s harder to get people,” Coniglio said. “It’s been key for us to bring in technology to make a safer environment to capture those additional opportunities.”
The company has been trying out several of the sorting robots on the market, and it has several different makes of robot installed at its San Francisco MRF, Coniglio added. That’s where it first deployed the Glacier model, and it also installed a Glacier unit at its Santa Rosa, California, MRF.
Coniglio said Glacier’s approach of working with the company to figure out what it was trying to solve with the robotics appealed to Recology. He said he also just likes the design of the robot.
“I think their approach, the way the robot attaches to the line, I thought that was a very innovative style,” he said. Glacier’s robots require just 3 feet of conveyor space, making them a fairly compact option to add almost anywhere in a MRF. Glacier says it provides a way for MRFs to improve capture without going through a full retrofit.
The company plans to install two more Glacier robots, bringing the total to six.
Continuing to scale up
Glacier launched in 2019, when tech industry founders Hu-Thrams and Areeb Malik saw dual opportunities in customer demand – from the U.S. recycling industry effects of China’s National Sword policies – and in rapidly advancing technology.
A year ago, the company received capital from funders including Amazon’s New Climate Pledge Fund, bringing the company’s total funding at that point to $13 million. And with this week’s announcement of an additional $16 million in funding, the company plans to continue on its growth trajectory.
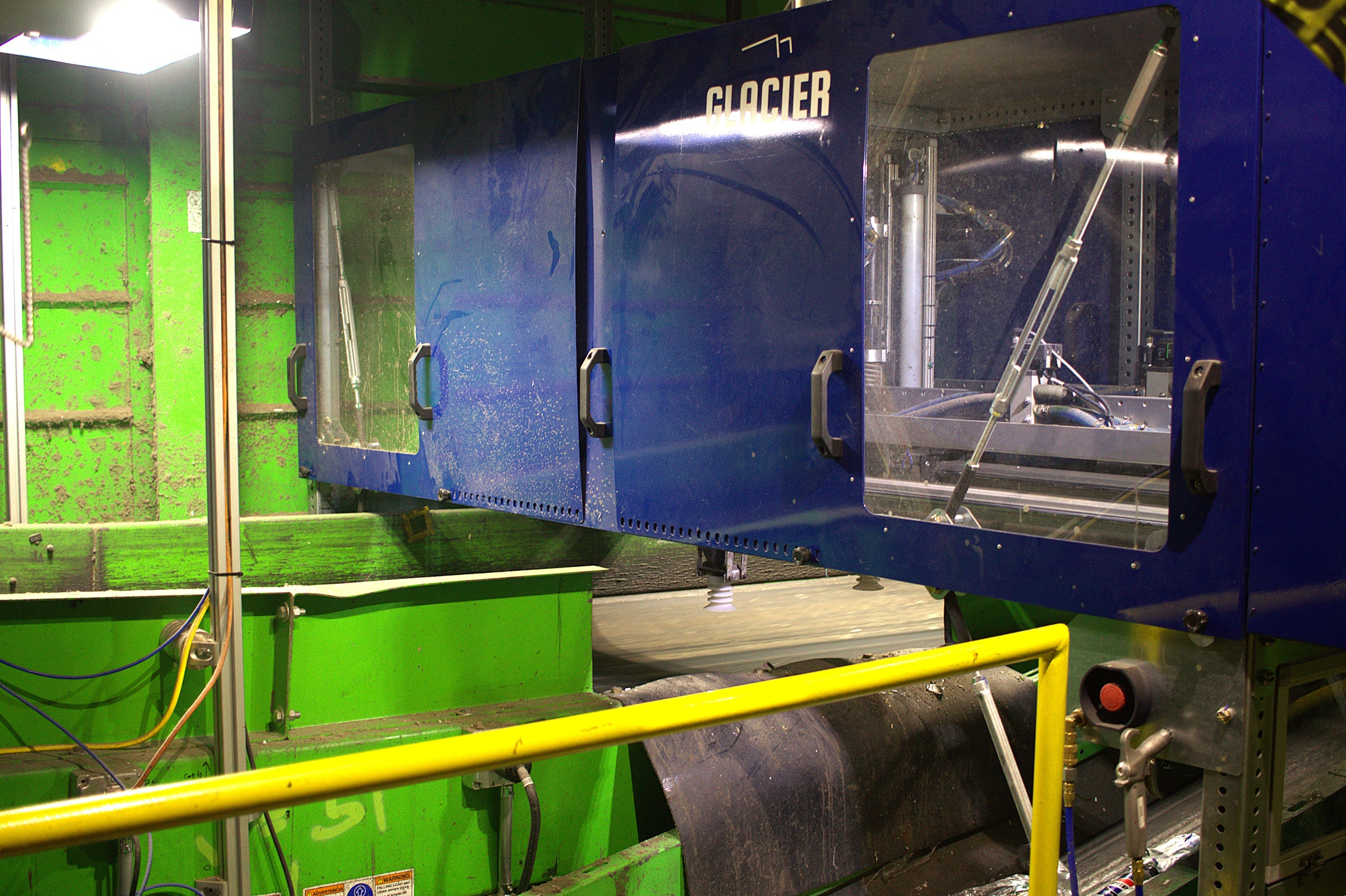
Glacier’s sorting robotics in on a conveyor line at the Recology King County MRF in Seattle. | Photo by Colin Staub
Over the past year, Glacier has upped its manufacturing capacity eightfold, Hu-Thrams said, an expansion that is directly tied to demand in the market.
The company’s sorting and analytics equipment is currently installed in two-dozen customers’ MRFs around the country, she said. Besides the Seattle MRF, that includes MRFs in the San Francisco Bay Area, Phoenix, Detroit, Minneapolis and Chicago, of all sizes and conditions, she added.
“We’ve proven that whether you’re a massive MRF that has recently gone through an upgrade or a single site with equipment that’s 20 years old, we can install successfully and improve your operations,” Hu-Thrams said.
Beyond its geographical customer footprint, Glacier has been investing in its AI visioning and data analytics model. The system captures and identifies materials as they move on the conveyor line, enabling the robotic sorter to grab target materials but also allowing for higher-level data analysis.
“A lot of our investment has already been funneled into making our AI model detect more things, detect better, detect more in real time,” Hu-Thrams said. “Now, we’re really taking that jump to translate this incredible data set of 3 billion proprietary waste images into a tool that can create actionable insights.”
The analysis can help MRF operators tweak their operations in a few ways, and it doesn’t always lead to installing robots. Hu-Thrams described a MRF in the Midwest that installed a Glacier camera on its residue line, where it showed the facility was losing 350 tons of recoverable material per year.
Most of the lost recyclables were from the PET line, and by calculating the estimated $130,000 value of lost recoverable material, the MRF operator could see it made economic sense to position a manual sorter on the PET line.
Glacier also works with MRF operators on a more holistic look at material flow through the facility, starting at the front end with bale composition audits and contamination studies. Sometimes MRF operators will place cameras before and after key pieces of sorting equipment to see how each step is performing.
In one case, a MRF customer used Glacier’s imaging equipment on a day when the facility was processing a typical stream of recyclables. All its equipment was up and running, the sorting shift was fully staffed. Using that as the baseline performance, the MRF operator made slight modifications – changing the angle of disc screens, for example – and was able to see the real-time results.
“That’s the type of real-time feedback that a lot of our customers find to be really powerful and maybe something they haven’t been able to easily measure before,” Hu-Thrams said. “MRF operators, our customers, they oftentimes don’t have the luxury to sit down with a 100,000-row spreadsheet and do their own data analysis to see what’s going on.”