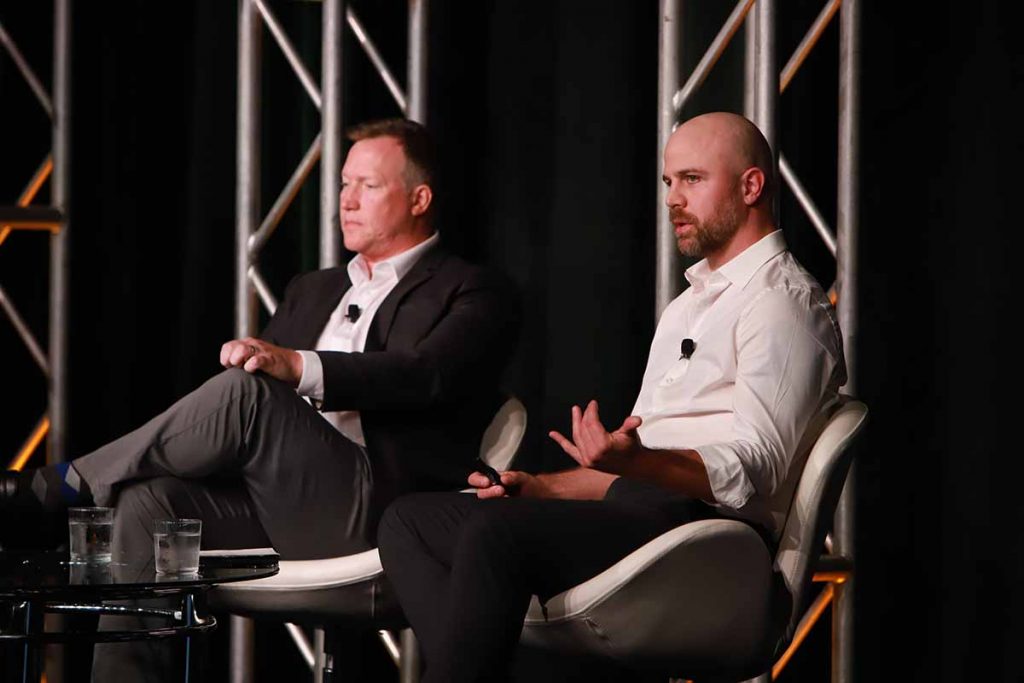
A session at the E-Scrap Conference featured evTerra’s Jeff Gloyd, left, and Chris Kaasmann of GreenChip. | Big Wave Productions/Resource Recycling, Inc.
When a lithium-ion battery fire breaks out in a recycling facility, the brain’s emotional centers often lead employees to grab extinguishers filled with fire suppression chemicals, but what they actually need is water.
That’s why training programs should give staff a full understanding of the chemical reactions at play, said Bo Bodo, director of learning and development at battery recycling company Li-Cycle.
“Give them the why behind the what and your training programs will be much more effective,” he said.
He was one of dozens of speakers at the 2022 E-Scrap Conference, which drew over 1,000 electronics recycling and reuse professionals to New Orleans last week. Discussions covered not only the intricacies of the electronics recycling and reuse businesses but a wealth of other topics of interest to the wider recycling world, including battery safety, extended producer responsibility programs, domestic investments in recycling capacity, international trade regulations and more.
Markets and ESG explored
In addition to robust discussions about fire safety in a workshop organized by the Institute of Scrap Recycling Industries (ISRI), the event explored investments in domestic metals recycling capacity, which in some ways parallels what the curbside recycling world is seeing in terms of domestic investments in OCC and paper recycling capacity.
Currently, most e-scrap materials containing precious metals are exported for recycling at Asian or European smelters, but companies are planning to bring more secondary smelting capacity to U.S. shores. Representatives from companies planning projects in Georgia spoke at the event about the market drivers they’re seeing, including the need to reduce greenhouse gas (GHG) emissions.
Similar to the push for more recycled content in packaging, electronics companies are working to increase recycled content in their products.
Jeff Gloyd, who is president of electronics recycling company evTerra, noted that brand owners want to use recycled content in their products to meet their environmental, social and governance (ESG) goals, but “it comes down to the financial conversation or it’s not going to happen.” If an OEM is putting 40% recycled resin in a printer, for instance, that’s because the company has conducted a study that shows it will sell more printers as a result, he said.
Therefore, the recycling industry needs to develop accessible, cost-effective solutions to supply that recycled material, he said. Chris Kaasmann, vice president of compliance at electronics recycling company GreenChip, noted that “there’s many different ways to track sustainability, so listening to what they want and putting that into tools that are accessible to them is super important.”
EPR programs adapting to changes
Waste reduction, the first of the three “Rs,” is naturally a key part of the electronics recycling industry because repaired/refurbished electronics are more valuable than commodities.
During a workshop titled “What Right to Repair Means for Recyclers,” Ryan Laber, vice president of business development at electronics processor Cascade Asset Management, predicted that the circular economy will continue to be a growing focus for the industry.
“There’s money to be made,” Laber said. “There’s a lot of equipment that can be repaired.”
Used electronics can also help bridge the digital divide in the U.S. and overseas.
During a workshop outlining the details of the R2 standard for electronics reuse and recycling, Patty McKenzie, outreach director at Sustainable Electronics Recycling International (SERI), noted that certification “supports a circular economy, but more than that, it enriches lives and livelihoods because it provides affordable products to people who need them.”
Other sessions touched on state extended producer responsibility (EPR) programs, which are just now coming on-line in the U.S. for printed paper and packaging but have been around for many years for electronics.
Still, a changing end-of-life stream for electronics, particularly fewer of the bulky cathode-ray tube TVs, means states are looking to overhaul their years-old EPR programs.
Patrick Santelli, senior compliance program manager for stewardship company Electronic Manufacturers Recycling Management Co. (MRM), noted that decreasing CRT weights are making it more challenging for OEMs to hit weight targets. The trend also means increased costs for OEMs without corresponding increases to recycling rates.
He and others also discussed changes to state programs aimed toward ensuring consumers in urban and rural areas alike have access to e-scrap drop-off opportunities. For example, convenience standards have been put in place in Illinois and South Carolina in place of weight-based targets. Through the convenience standards approach, the state mandates a certain number of e-scrap drop-off locations and collection events in different areas based on municipal jurisdictions and populations. That way, brand owners can’t meet their goals solely by funding e-scrap recycling in urban areas, leaving rural HHW programs struggling to find cost-effective recycling solutions for their residents.
“I think as weight starts to become more scarce, I think it’s likely to see a greater adoption of convenience standards,” Santelli said.
A version of this story appeared in E-Scrap News on September 19.
More stories about challenging materials
- Facing increasing volumes, Ridwell tweaks textile recycling
- Nebraska city to accept paper cups in curbside bins
- A hot topic for recyclers: Battery-related fires