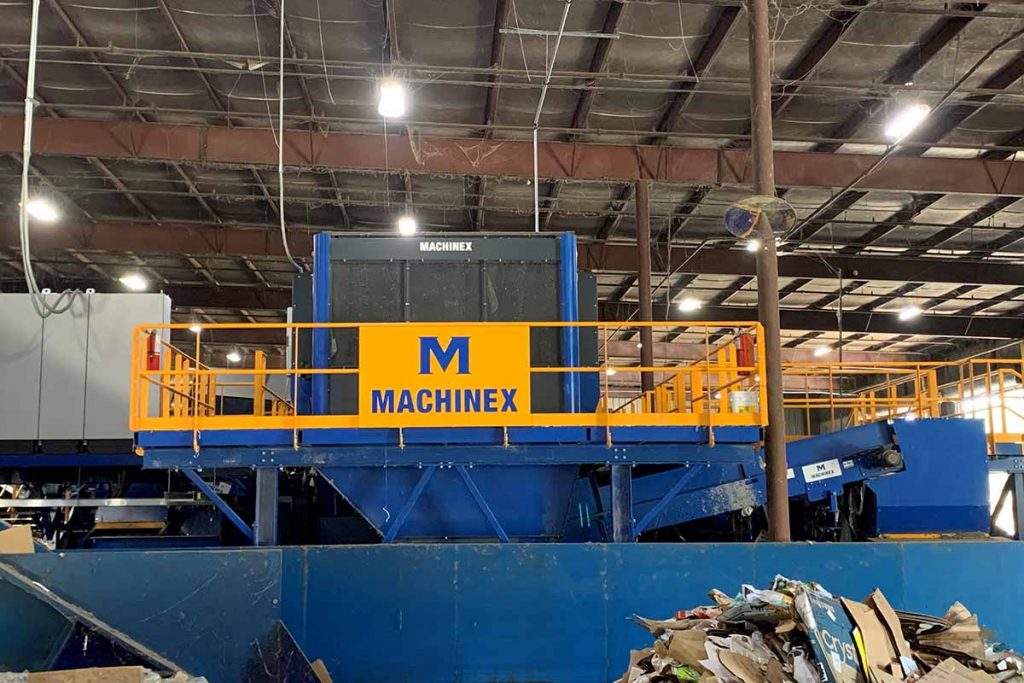
Recycling equipment manufacturer Machinex provided improved sorting technologies for two Pratt single-stream MRFs. | Courtesy of Machinex
Pratt Industries may be primarily focused on recycling fiber into cardboard boxes, but with higher scrap plastics prices, the company also saw a business opportunity in boosting PET and HDPE bottle sorting.
The 100% recycled cardboard manufacturing giant last year upgraded two of its materials recovery facilities (MRFs), which sort and bale curbside recyclables either for consumption by Pratt mills or for sale to other recycling companies.
The upgrades occurred at Pratt MRFs in Duncan, S.C. and Fayetteville, N.C. and were each “multi-million-dollar investments,” that improved the company’s ability to recover PET and HDPE, said Kurt Schmitz, senior vice president of Pratt Recycling.
Pratt’s recycling division supplies bales of recovered cardboard and paper to its network of mills, which are located in Conyers, Ga., New York City; Valparaiso, Ind.; Shreveport, La. and Wapakoneta, Ohio. A privately held company, Pratt is also working to build a paper mill in Henderson, Ky.
Duncan, S.C. improvements
Recycling equipment manufacturer Machinex provided improved sorting technologies for both of the single-stream MRFs.
In Duncan, Pratt’s MRF sorts about 15,000 tons of recyclables per year from the city of Greenville and surrounding areas. For the upgrade, Machinex added a MACH Ballistic separator, which sorts two-dimensional objects, such as paper and cardboard, from 3D ones, such as plastic containers, while also removing fines. That ballistic separator replaced an older rubber disc screen.
The Quebec-based company also equipped the facility with MACH Hyspec optical sorters to sort fiber and PET/HDPE, according to a Machinex press release. That retrofit took place in June 2021.
Schmitz said prior to the installation of the optical sorters all PET and HDPE were manually sorted.
Fayetteville, N.C. project
Later in the summer, Machinex retrofitted Pratt’s Fayetteville MRF, which sorts up to 20,000 tons per year from Fayetteville and surrounding areas. Machinex installed a MACH Ballistic separator, two MACH Hyspec optical sorters and a quality control station.
Schmitz explained that the ballistic separator replaced two bounce belts, improving sorting effectiveness and throughput. Bounce belts are eight-foot-wide conveyor belts with agitating hammers underneath. Like ballistic separators, they’re designed to separate 2D from 3D materials.
Schmitz said one optical sorter was installed behind the ballistic separator on the 2D fraction. That optical is removing contaminants from the paper stream. The other optical sorter is a dual-eject system that’s targeting both PET and HDPE. Before the optical sorters were installed, all containers were manually picked, he said.
“Good commodity prices and improved recovery rates from residue were the driving factors to install the optics,” he said.
Additionally, a QC station was added after the eddy current separator to improve the quality of used beverage can (UBC) bales so Pratt can achieve a higher aluminum grade and fetch a better price, he said.
That project began in July and was completed in August 2021.
A version of this story appeared in Plastics Recycling Update on April 26.
More stories about MRFs
- Recycling facility fires expected to reach new high
- Haulers feel effects of lower recycled commodity prices
- WM report suggests 2025 goal is out of reach