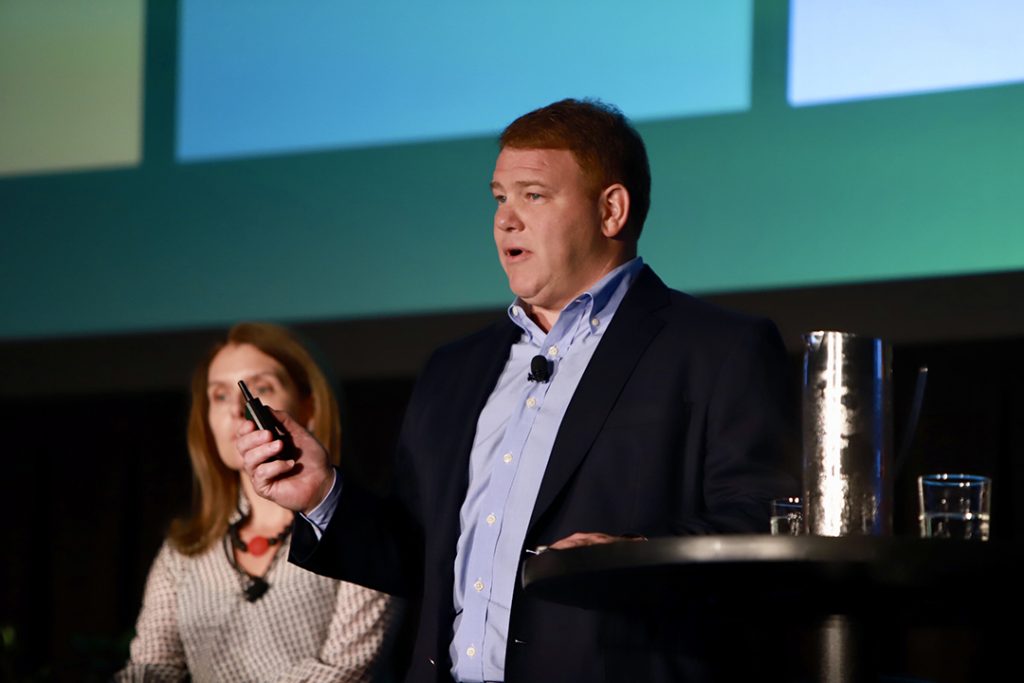
Scott Montgomery of RePower spoke recently at the Resource Recycling Conference and Trade Show. | Resource Recycling Conference/Brian Adams Photography
The leader of mixed-waste processor RePower South recently spoke on why recovering recyclables from the trash stream is a good option in certain cases.
RePower South launched in 2013, licensing technology that creates a solid fuel from waste materials. The company has been working to advance several projects in the Southeast U.S. Now, the company has two major projects underway, in Montgomery, Ala. and Berkeley County, S.C.
During the 2019 Resource Recycling Conference and Trade Show in New Orleans last week, company CEO Scott Montgomery shared a detailed description of the processes employed in both communities. He also elaborated on the role of mixed-waste processing alongside the recycling industry.
“We’re not the silver bullet by any means,” Montgomery said. “I think that we’re just one of many companies trying new things to increase recycling.”
Process fits the bill
RePower’s technology was developed as a way to get more material out of the waste stream, Montgomery said.
The communities in which RePower operates were in positions that made the business model a good fit, Montgomery explained.
Berkeley County, for instance, was “never going to do single-stream,” Montgomery said. The county had studied adding curbside collection of recyclables, he said, but as a partly rural county that is experiencing significant population growth, officials determined the cost of recycling collection would be too high.
“We’re set up at their landfill. The haulers bring everything to us. The difference is we process it and try to get as much out of it as we can,” Montgomery said.
In Montgomery, the former Infinitus Renewable Energy Park (IREP) mixed-waste facility had trouble making its business model pencil out, and the facility eventually closed. The plant was taken over by the city, which put out a bid for a new operator to start running it again. Proposals came in to reopen the facility as either mixed-waste processing plant or a single-stream MRF.
“The only person that came to the table for single-stream required the city to put in multiple millions of dollars, which they were not willing to do,” Montgomery said. RePower offered to put its own capital into the facility. The bid was ultimately accepted.
RePower has 25-year agreements with both communities. In both cases, there was no requirement for the community to commit money to the project. And RePower has profit-share agreements in both cases.
“It doesn’t work for every community, I’m sure of that,” Montgomery said, noting that RePower has bid on several projects that it ultimately did not get selected for.
The RePower model, extracting recyclables out of the trash stream where recycling collection is not offered, differs from mixed-waste facilities in some other locations. For example, a mixed-waste MRF in San Leandro, Calif. is designed to sort the trash stream from communities that already have curbside recycling; the mixed-waste operation acts as a last chance to recover any remaining recyclables that made it to the trash. A similar facility is being planned in Santa Barbara County, Calif.
How it works
RePower takes in municipal solid waste at its facilities and performs a number of processing steps to extract recyclable materials from that stream.
The process recovers steel, aluminum, PET, colored and natural HDPE, PP and certain fiber grades. Paper and plastics that are not recoverable for recycling are processed for use as dry fuel. Other materials, such as “inerts” and green waste, head for disposal.
RePower diverts about 15% of material in the waste stream for recycling, Montgomery said, and the company recovers another 35% of the stream for fuel.
“If somebody has a profitable, or at least a break-even solution for the organics, we’re all ears,” Montgomery said. “Because that’s a big part of what goes back to the landfill.”
Both Berkeley County and Montgomery, Ala. run their own landfills, although that’s not a requirement for the RePower model, Montgomery said.
The Alabama facility had a good amount of mixed waste processing equipment in place when RePower took over, but the company made some significant modifications. The company added a fuel conversion system and a shredder on the front end to cut down on materials that would jam the sorting line.
The Alabama plant can process 120,000 tons per year. That plant started up in January and is now processing 100,000 tons per year, Montgomery said, or about 42 tons per hour. There are 60 employees, and it relies more on manual sorting than the South Carolina site.
The Berkeley, S.C. facility is running at about 50 tons per hour and has 45 employees. RePower raised $12 million in equity and sold $43 million in bonds to finance the project.
It’s a bit different from the Alabama site, particularly the equipment. In addition to numerous optical sorters, the South Carolina plant has nine robots performing quality control, meaning the facility has fewer employees. Montgomery said he’d like to have robots in the pre-sort area as well, given the potential danger in that part of the facility, but that technology is still on the way.
“We wanted as much technology as we could, because we could afford to when we financed it with a 25-year contract,” he said.
The quality control robots have the ability to “learn” from mistakes and improve their sorting abilities accordingly.
Both the Alabama and South Carolina sites have a rocket mill, which is a system that prepares material for conversion into fuel.
“It pulverizes, shreds and also dries the paper and plastics that can’t be recycled, and that’s what we bale up as our fuel and sell to cement mills,” Montgomery said.
Commodity sales
RePower isn’t recovering mixed paper, although Montgomery said he’d like to because it would increase diversion, potentially allowing the company to hit 65 to 70% recovery. But the company sells OCC, plastics, aluminum and steel just like any other recycling facility.
“I won’t say we haven’t had any rejects, but now that we’ve gotten our quality up, now that we’ve been running for a couple months, we’re selling everything and it’s going well,” he said. “If the mixed-paper market would come back we could certainly do that, [but] to add the people for the quality control just doesn’t make economic sense right now, so our diversion is less because of that.”
The fuel product, which is essentially shredded and dried paper and plastic, is baled and shrink-wrapped for storage outdoors. RePower sells it to cement mills, which can generally use the fuel easily. The biggest fuel concern is making sure no PVC gets into the fuel. The chlorine content is detrimental to the material being used for fuel. To combat this, RePower is particularly careful to remove PVC using the optical sorters. Other solid recovered fuel producers, including BioHiTech Global, take similar steps to avoid PVC in their streams.
“What we didn’t realize is that there’s so much chlorine and salt in the organics, and in the mixed waste processing that’s been a challenge to clean it up,” Montgomery said. “But it just took us a couple months and we’ve gotten there.”
The fuel burns at 9,500 to 10,000 BTUs, making it “not too far off from coal,” Montgomery said. It’s also relatively clean-burning compared with coal, he added.