Experts predict large-format lithium-ion batteries will show up more regularly in the waste stream in the coming years as their use grows in vehicles. A Canadian company is looking at the trend as an opportunity.
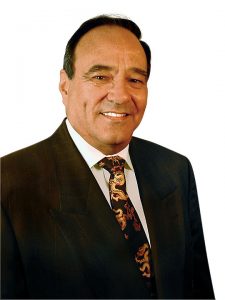
Larry Reaugh, American Manganese
British Columbia-based American Manganese is employing hydrometallurgy in response to the need for end-of-life management as well as supply of metals for battery manufacturing. Although the batteries are still in the early stages of entering the waste stream, their sheer value and predicted growth has the company convinced there’s already a critical mass.
In an interview, a leader from the company said its process targets the “cathode” section of large-format lithium-ion products. That portion of the battery contains manganese, cobalt and other metals.
“It’s the most valuable part of the battery. This one singular item probably represents 25 to 30 percent of the value of the battery,” said Larry Reaugh, president and CEO of American Manganese, in an interview with Resource Recycling.
The electric vehicle battery stream is anticipated to grow exponentially in the coming years, as electric car sales continue to increase and countries including China set goals for electric vehicle usage.
But even now, Reaugh said there is enough of a stream for EV battery recycling to be profitable. He estimated there were roughly 280,000 spent EV batteries entering the waste stream globally in 2015.
Still, the stream holds challenges. In a recent interview with Resource Recycling sister publication E-Scrap News, a battery recycling expert described challenges in identifying and separating the batteries. He also noted barriers to making battery recycling pencil out financially.
A $5 million pilot plant
American Manganese, which is publicly traded, is looking to scale up its proprietary hydrometallurgical process and create a pilot plant, which would be the model for a portable processing solution. The pilot plant will cost about $5 million, Reaugh said. He said a commercial plant is about two years down the line.
Reaugh said a plant using his company’s technology could have a throughput of up to 20 tons per day, a very small volume in mining terms, and could be “very lucrative.” Although disassembly will require more operating space, the processing plants he plans to build and sell would be relatively small due to the concentrated cathode feedstock.
Reaugh has a mining background, and his company picked up a low-grade manganese mining property in Arizona several years ago. The goal was to develop a technical solution to produce manganese metal. But, Reaugh said, “the price defeated us,” and his company hasn’t moved forward with the Arizona project.
Instead, American Manganese began focusing on a different possible application for the same technology: targeting cathode materials from lithium-ion batteries.
Cathodes vary in material makeup. Battery chemistries include lithium cobalt, lithium nickel manganese cobalt, lithium manganese, lithium nickel cobalt aluminum and more. End-of-life recovery does not currently focus on isolating those various materials, Reaugh said.
“Right now, they’re being burned. You get some cobalt out, 40 to 60 percent, and the rest of it, aluminum, manganese, all goes into slag, which is a waste product,” he said. “That’s not a solution.”
American Manganese is employing a process that allows recovery of all those different battery chemistries, Reaugh said. Its technique is a hydrometallurgical process similar to what is found in a mining circuit, he explained. It uses thickeners, tanks and pumps, to separate the metals contained in the cathode.
The process has extracted 92 percent of the lithium, and Reaugh said he anticipates it can reach 100 percent lithium recovery if the metal is cycled through the process multiple times.
“We’ve been able to get out 100 percent of the cathode materials,” he explained. “It’s been extremely successful.”
The company has filed for a U.S. patent for the technology.
“We’ll eventually file in China and Europe and any other country that’s going to be leaning heavily into the lithium-ion battery space, and I think everybody is eventually,” he said.
A 1,000-pound lithium cobalt battery has about $6,000 worth of cathode material within it, Reaugh said. A similar-sized nickel manganese cobalt battery has about $3,500 worth, and lower-end nickel cobalt aluminum battery has $1,600 to $1,700 worth in it.
“Those are big numbers,” Reaugh said, noting his processing cost will be around 25 to 30 cents per pound, plus a battery disassembly cost that is not certain yet. “There’s a lot of profit in it.”
Cobalt is currently priced at $27.67 per pound.
More stories about challenging materials
- Facing increasing volumes, Ridwell tweaks textile recycling
- Nebraska city to accept paper cups in curbside bins
- A hot topic for recyclers: Battery-related fires