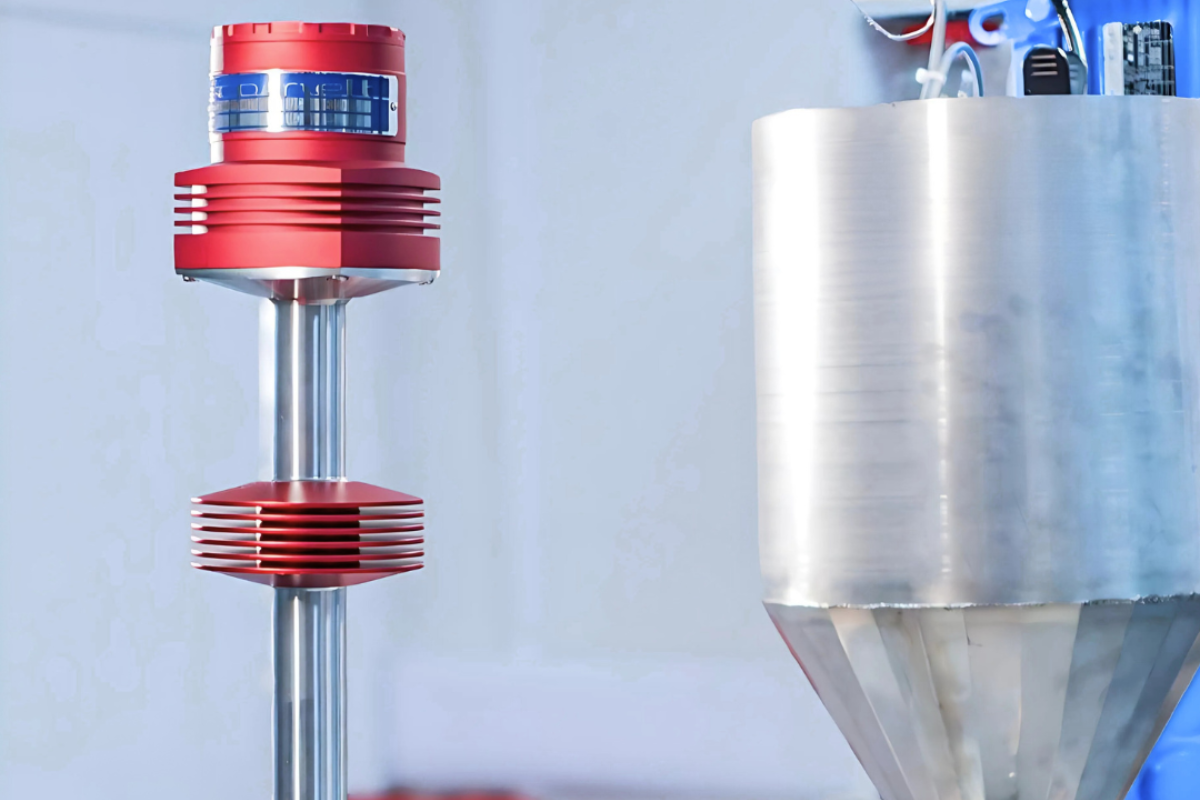
The melt flow sensor brings data collection right into the production line. | Photo courtesy HydraMotion
Equipment supplier HydraMotion has released a new line of melt flow analyzing tools, which report crucial resin composition information in real time. The company says the new equipment is particularly well-suited for RPET production lines. Continue Reading