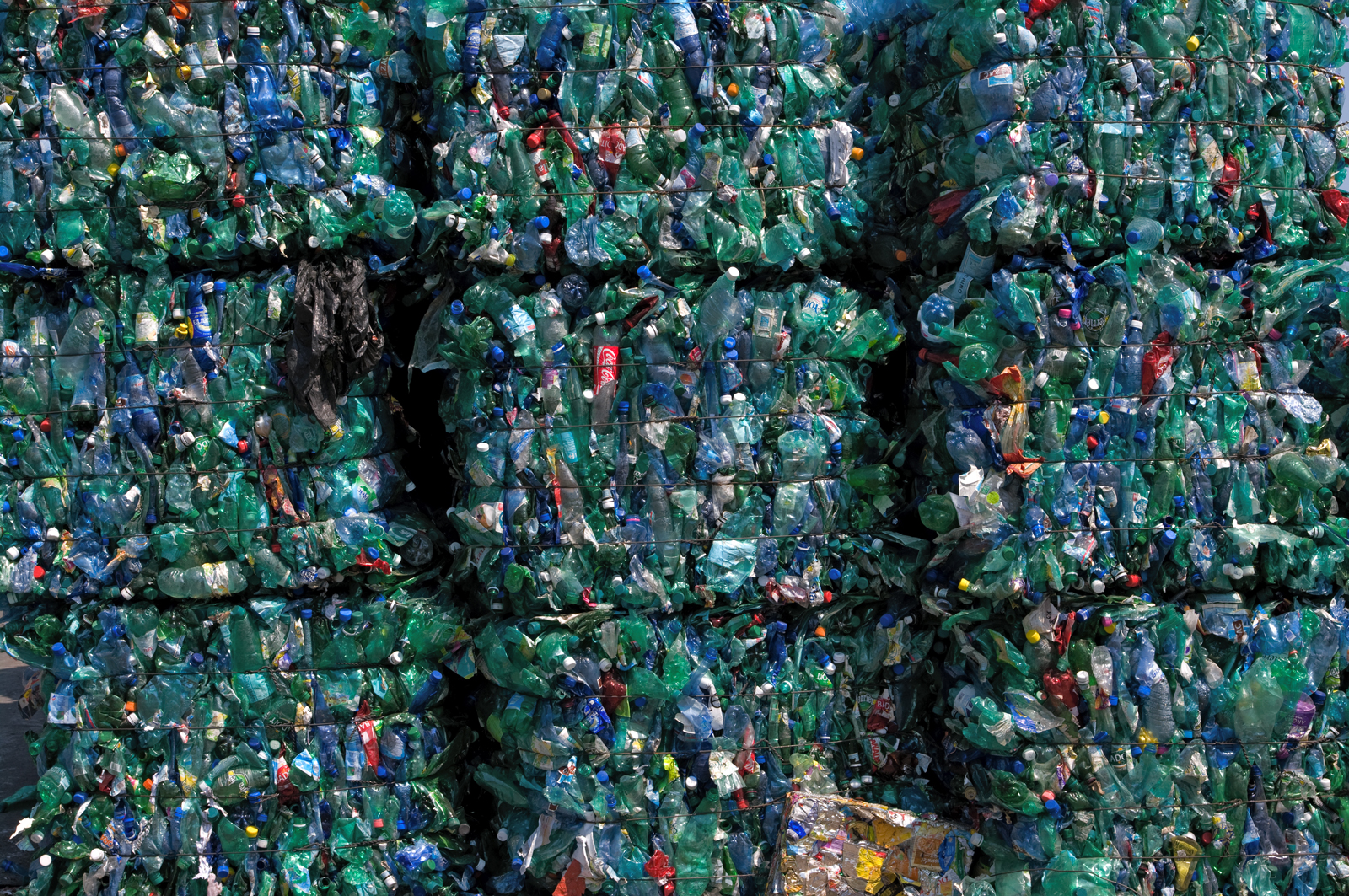
Huguette Roe/Shutterstock
A spate of recent laws in various states set lofty goals for both recycling materials and putting that recycled content back into new products. However, the infrastructure and industry are not at the right scale to meet those statute-mandated goals, and that could spell legal and financial trouble for producers. Those producers have a few options to consider, but action must be decided on soon, as some of the deadlines are already in play.
The recycling industry knows that recycling is not just about plastics; however, for legislators, plastics are at the forefront of recycling policy. Whether it’s California’s SB 54 pushing toward a 25% source reduction in plastic packaging, or the minimum post-consumer recycled content standards in California, New Jersey and Washington, plastics are widely seen as the issue driving policy.
The good news in this is that solving for increased recovery of plastics will bring solutions that improve the system that also delivers paper, glass and metals to recycling facilities, as they all take a ride in the bin in residential curbside recycling programs. However, as extended producer responsibility (EPR) laws for packaging are being implemented in California, Colorado, Maine and Oregon, we are years away from seeing major increases in recycling rates in those states. That leaves a significant gap between the demand for recycled material, particularly plastic, and the available supply. Combine that gap with the coming post-consumer resin (PCR) standards, and there is a major issue ahead with respect to the mismatch of supply and demand, and it has legal ramifications.
Right now, the cumulative demand for PCR from the three state laws plus the voluntary commitments to use PCR by brands far exceeds current availability of PCR. A study published in 2022 by Independent Commodity Intelligence Services (ICIS) found that the U.S. would need an additional 140 materials recovery facilities (MRFs) to close the gap and meet the demand that is already being expressed for PCR, including PET, HDPE and PP. That does not include possible new policy drivers that could further widen this gap.
New Jersey’s Recycled Content Law states in its purpose statement, “By requiring manufacturers to utilize post-consumer recycled content, markets for such materials are enhanced as demand shifts from virgin to recycled sources. Recycling relies heavily on supply and demand to keep the industry afloat. As oil prices decrease so do prices for virgin plastic which subsequently decrease the demand for recycled materials. Requiring manufacturers to meet minimum recycled content requirements helps to stabilize markets, increase the resiliency of the recycling industry when oil prices fluctuate, and shield municipal recycling programs from the volatility of the cost to recycle.”
Really? The legislature placed a heavy burden on this one law. While indeed the demands are real, can this drive the level of investment needed to expand infrastructure, encourage participation, reduce contamination in residential streams and align material with optimal end markets? I think not.
Further, no company makes packaging destined for a particular state, or for that matter, three states. So, to meet the demands of California, New Jersey and Washington, companies need to meet these standards across their national portfolios. That requires a level of supply that simply will not be realized in time for the compliance requirements.
Many brand commitments are coming due in 2025 and the state laws have schedules that require achievement of various levels of PCR on an aggressive calendar. For example, California will require beverage containers to include 25% PCR by January 2025 and 50% PCR by 2030. New Jersey has requirements for plastics, paper and glass. It requires glass packaging to meet a 35% PCR content standard this year. To say that is impossible is a colossal understatement.
Washington’s law notes that the regulations for the bill begin in 2023 and each product category is phased in with increasing post-consumer recycled content (PCRC) requirements over the next fifteen years. Further, it adds that by 2036, all packaging for covered product categories must include at least 50% PCRC, excluding trash bags, which have a 20% requirement after 2027.
“Each year, producers must report on minimum post-consumer recycled content (PCRC) requirements from the previous year,” the law notes. “The minimum requirements began for beverage and trash bag producers in 2023. Household cleaning and personal care products will start in 2025, and dairy milk and wine sold in small 187 ml bottles will begin in 2029.”
The market is expected to evolve rapidly to make all of this new PCR available, and as you have already figured out, I am skeptical this will happen.
We can certainly talk about how these laws fail to reflect the reality of how recycling markets work, but right now that discussion is only useful in terms of informing how we should engage as new proposals are considered. These laws are already in effect now, so the challenge here is what can industry do to help ensure compliance? In my estimation, something will need to shift dramatically over the coming years, or we are going to hit a “compliance wall.”
What are the options? Multiple industry segments could align and double down on supporting EPR to increase recycling rates and then go back to regulators and say, “look, we’re doing all we can, so can we slow this down?” Would this take the form of working in some of the largest states, say New York and Texas, or would it look more like a federal solution? Do we organize an effort to push back the compliance timelines without the sincere effort to push up recycling rates first? I suspect this would be costly, poorly received and highly likely to fail. Do we run out the timelines, fail to comply and see what happens?
The answer here is elusive, but one thing is for sure: pretending the problem isn’t there will not solve it. Sectors spanning CPG, beverage, personal care, household products and retailers need to engage in dialogue and test where there may be common interest and a possible way forward that all can engage with and support.
Companies often set audacious goals and then fail to meet them. In those cases, a company can always shift the narrative, explain away the failure and earn favor by setting yet another goal. It’s different for regulations. Failure to achieve these requirements comes with financial penalties. In the case of California, the law sets penalties at a rate of $0.20 per pound based on the shortfall of recycled content used compared to the minimum content requirement.
In the past, policy has forced companies to think more about their packaging and its impacts, it has also driven innovation and a collective response around implementation. This momentum needs to be harnessed now and focused in a constructive way on a collaborative effort to offer and support solutions to the PCR compliance wall challenge.
Michael Washburn is principal and owner at Washburn Consulting: Sustainability & Public Affairs.
This article appeared in the Spring 2024 issue of Plastics Recycling Update. Subscribe today for access to all print content.