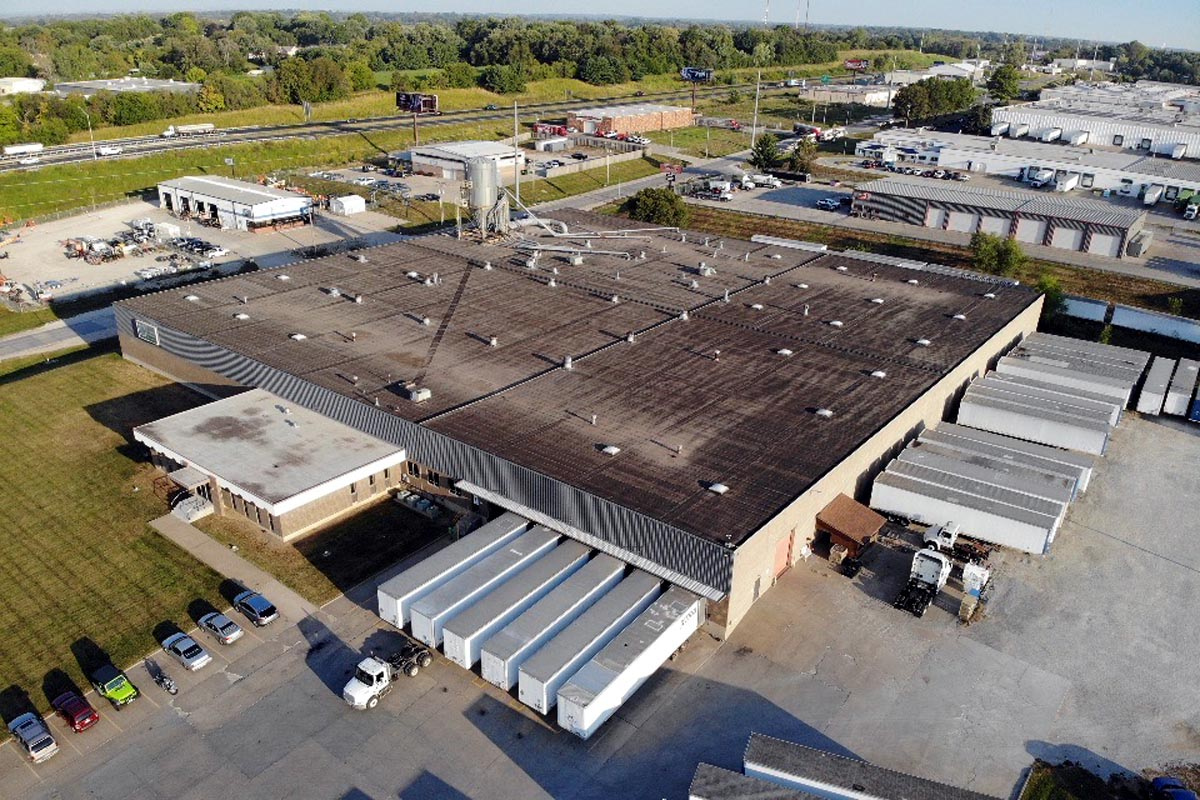
St. Joseph Plastics’ grinding facility in St. Joseph, Mo. | Courtesy of St. Joseph Plastics
Two plastics reclaimers have merged to form one company with nine facilities and about 300 employees across the Midwest and South.
Indianapolis-based Plastic Recycling Inc. (PRI) merged with Missouri-based St. Joseph Plastics in late September. Together, the companies have the capacity to produce and cross-sell 50 million pounds of curbside PCR and 200 million pounds total of compounds with recycled content annually.
In an interview with Plastics Recycling Update, company leaders emphasized the similar company cultures. Founded by Alan Shaw in 1988, PRI employs five members of the Shaw family.
“The Shaws are very entrepreneurial and they look at new opportunities, new projects. They’re always moving forward. We’ve always tried to do the same,” said Rob Starr, president, CEO and owner of St. Joseph Plastics, which is based in St. Joseph, Mo., north of Kansas City.
“I think the culture, the similarity of the entrepreneurial spirit, that’s really to me what makes it a great fit,” he later added.
St. Joseph Plastics mostly handles PP, but it recycles PE as well. Roughly one-fifth is post-consumer plastic. PRI recycles a variety of polymers from different sources, particularly PP, PE, ABS and polystyrene.
To the merger, PRI brought three facilities in Indianapolis; two in Jefferson City, Tenn.; and one in Spartanburg, S.C. It has roughly 180 employees. With about 100 employees, St. Joseph Plastics brought two facilities in St. Joseph and one in Sedalia to the table. The company leaders declined to provide details of the merger transaction.
Business benefits of combining
The combination yields a number of business benefits.
On the supply side, it allows each to source post-consumer and post-industrial scrap materials from a larger geographic area, noted Brandon Shaw, marketing manager at PRI.
Marco Meloni, PRI’s chief operating officer, said that large customers want to ensure their plastic suppliers have access to a secure and ample supply of feedstock. Combining the companies gives the reclaimers access to diversified feedstocks and the ability to recycle them for use in different applications.
St. Joseph Plastics earlier this year received a letter of no objection (LNO) from the U.S. FDA to recycle curbside food-packaging PP scrap into new food packaging. Meanwhile, PRI has an LNO allowing it to recycle source-controlled PP streams into food packaging.
At the same time, PRI has brought on-line a $2 million line in Indianapolis that will be able to process curbside PP for use in food-contact applications. Shaw noted that PRI will be able to license St. Joseph Plastics’ LNO to produce the food-grade PP from curbside sources. That LNO currently allows the PP to be used in packaging for dry solid foods (with no free fats or oil), and the package can be exposed to temperatures ranging from freezing up to room temperature. PRI aims to bring its multi-million-dollar lab to bear to achieve a broadening of the letter’s conditions of use, Shaw noted.
On the other side, St. Joseph Plastics can leverage PRI’s LNO for source-controlled PP, and St. Joseph Plastics will be able to run the same compounds for automotive markets that PRI is producing, Starr said.
St. Joseph Plastics plans to leverage PRI’s capabilities to help it produce higher-quality resins for more demanding end applications, Starr noted.
“We’re just so much better combined,” Starr said.