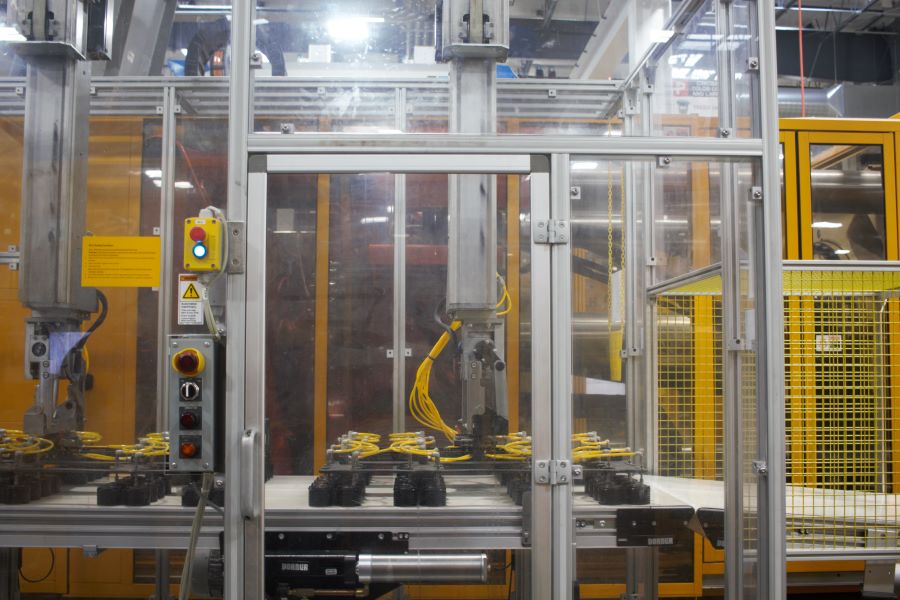
PakTech uses injection molding equipment and blow-molding-grade material, as well as modular equipment designs, for cost and speed efficiency. | Marissa Heffernan/Resource Recycling
Extended producer responsibility programs, labeling requirements and minimum PCR mandates offer both challenges and opportunities, and company leaders at 100% PCR packaging manufacturer PakTech have been steadily working to position the company for the future.
PakTech makes carriers and handles for beverage containers out of 100% recycled HDPE, and recently developed a near-infrared-sortable black pigment for an alternative to carbon black. Its products are also in the process of being accepted curbside under Oregon’s coming packaging EPR law, plan pending approval.
“Like anything, there are challenges and there are opportunities, and we lean into the opportunity and encourage others to look at what we’re doing and do the same thing,” said Jonathan Levy, manager of sustainability and public policy, during a recent tour of the company’s Eugene, Oregon, manufacturing plant.
At the facility, sustainability is baked into the process, from the 100% recycled content handles themselves to the lighting and HVAC systems, said Dan Shook, director of operations.
That’s because initially, the business was a custom molding shop, and handles were a smaller side project. By the early 2000s, PakTech began to focus on the handles, and a move into a larger building then gave the company the chance to start fresh.
The result was an efficient and modular design, with as many aspects as possible done in-house and a focus on eliminating bottlenecks, Shook said.
“We wanted a work center that could take the many different items and the next position up would run the job, and we wouldn’t have to be constrained to wait for a particular tool,” he said. “That was what drove that modularity.”
With production flow optimized, Shook said that the same critical eye was then systematically turned to other aspects: “Let’s deal with our capacity constraints. Now let’s improve our infrastructure. We went from, OK, now we’ve got enough infrastructure, now how do we optimize that so it’s energy efficient? And then we started going through.”
Now, when PakTech decides to upgrade any of its injection molding machines, as it is currently doing, there’s minimal downtime and other machines can pick up the slack in the interim.
“Our goal here is to keep making innovative technology a staple as far as our machinery here, but we know that in 10 years time, technology is going to change and it’s going to make sense not to keep running that asset, but to switch it,” Shook said.
Moving to curbside
In Oregon, PakTech’s handles are in the process of moving from the depot drop-off list to the curbside list under the coming Recycling Modernization Act, after the company worked closely with both the producer responsibility organization Circular Action Alliance and the state Department of Environmental Quality. The change would be made in the form of a plan amendment later this year, which would go through a review and approval process.
“We went to them and we explained everything,” Levy said. “People are going to put their handles in the bin anyway, so let’s just get in the bin. We’ve been able to prove it out that we’re not a contaminant.”
In the past, MRFs were concerned about the flatness of the handles and whether they would flow through the facility correctly, but Levy said tests have borne out that the handles can be sorted and “the thing is, our handles really are not flat. I mean, paper is flat. Our handles have got different ridges and different bumps.”
“Honestly, once it gets collected, coming out of a recycling truck, it’s even more 3D,” he added. “They get bent.”
PakTech recently achieved the Association of Plastic Recyclers’ design for recyclability recognition, as well as curbside recyclable certification from How2Recycle, the Australian Packaging Covenant Organization and Circpack by Veolia. In addition, PakTech’s handles were just classified as an accepted material in both APR and Recycled Materials Association scrap specs for HDPE bales. (APR owns Resource Recycling, Inc., publisher of Plastics Recycling Update.)
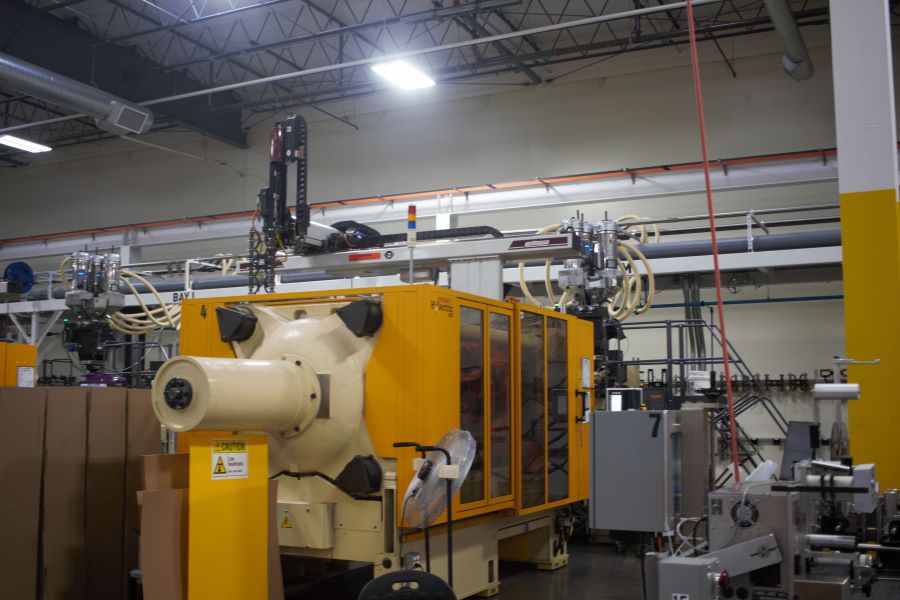
Marissa Heffernan/Resource Recycling
A major factor in the recyclability of the handles is that even though PakTech uses injection molding technology, the material they use is blow-molding grade. Gary Panknin, supply chain manager, said it’s “one of the key fundamental things that’s enabled us to use 100% post consumer recycled material.”
Shook, the director of operations, “had the foresight, looking into the future for innovation to be able to run blow molding material instead of injection grade material,” Panknin said. As a result, PakTech was able to hit close to 100% recycled content by 2012, years ahead of any PCR mandates.
Shook said that was a bit of serendipity.
“At the time we were only trying to satisfy the requirement in New York, which was 30%,” Shook said. “Our initial R&D was like, ‘Hey, we can do that 30%, no problem.’ And the owner made the bold decision: ‘Nope, we’re gonna do 100%.'”
Because of the material grade, Panknin said handles in theory could be returned along with bottles in states with bottle deposit refund systems, but “that’s a tough one to get across to people.”
“It’s the same blow-molded fractional melt material,” he said. “It’s hard to get people to understand it, because they’ll look at it and say, ‘Well, it’s injection grade.’ No, it’s different than an injection grade. It’s actually a bottle.”
A sortable black pigment
NIR sorting technology, which many MRF optical sorters are equipped with, is typically considered unable to detect black plastics. But it’s really the carbon black that is in the pigment that makes it difficult to sort.
PakTech is currently working to publicize a black pigment that is NIR-sortable, Shook said, in an effort to get carbon black pigment out of the manufacturing chain and make it easier to recycle HDPE and other resins.
“We really want to see other folks adopt the carbon black elimination and make that even better, especially in primary packaging, because that’s where our niche is,” he said, so if the industry can get carbon black out of those applications, “we’re in good shape.”
The work took about five years, Panknin said, and unlike other carbon black alternatives on the market that use chemical additives or metal flake to achieve reflectivity — which introduces more contaminants — PakTech worked with Bioregion Technologies, a local grain company and the previous owner of its current building, to use its grain manufacturing waste.
“It all kind of just fell together,” Panknin said. “We just came up with a real circular solution, and we’re coming from the grain manufacturing side, so it’s organic and renewable.”
The pigment is also a true black, Shook said, whereas “most near-infrared alternatives to black, they’re not really black, they’re just dark.”
“I mean, you could tell if you compared them side-by-side, carbon black to the true black pigment — but boy, they are pretty spot-on as far as there really is no compromise for the brand, which is really cool,” he said. “Because otherwise they would be compromising: ‘Well, that’s not quite black. It’s kind of violet.'”
Levy added that while eco-modulation factors for the various packaging EPR programs are not yet fully set, he believes that PakTech’s products should qualify for many of them, as it’s 100% recyclable, uses high levels of recycled content, is weight-optimized and does not use carbon black.
“We heard the MRFs, we heard the industry, we heard everyone, and they were all saying black is not recyclable,” Levy said, adding that Panknin decided to tackle the challenge. “Now we have a recyclable black package.”
The black packaging is undergoing a series of different flow studies in MRFs, and while the results are not yet final and public, Levy said they’re showing very high recovery rates, north of 80%. Panknin added that lab-level testing has also shown high recoverability, so “here it is, black and white.”
The biggest headwind against adoption, Shook said, is combatting the ingrained belief that anything black is not sortable.
With PCR tackled, source-reduction policies remain a concern
On the policy side, Levy said when it comes to PCR requirements, “I don’t really have very much to say.”
“We want everybody to get to where we are, so, I mean, we support them and we want to see more PCR requirements and that kind of thing,” he said. “But as far as how is it going to affect our company? I’m not worried. We’re already there.”
Looking at reuse, there’s a strong grassroots effort among local breweries in several states, Levy said, but PakTech is still exploring an official system. For now, “we think it’s great that it’s happening” organically, he said.
Panknin noted that the company established a recycling collection program several years ago and gave breweries using their products blue bins and posters, which are now in more than 500 locations in North America. But they found that instead of returning the material to PakTech for recycling, many breweries decided to reuse them instead.
Logistics for such a program is the largest hurdle, Shook said, as it’s “a little impractical to say we’re going to return stuff from the Southeast and the Northeast and then reprocess it here and then send it back. So it’s great to see the folks who are regionally doing this.”
However, source-reduction requirements do worry Levy and Shook. Their product already uses as little material as possible while maintaining functionality, Shook said, and “if you say we’ve got to reduce 20%, you’ve just pushed us out. There’s nothing I can do.”
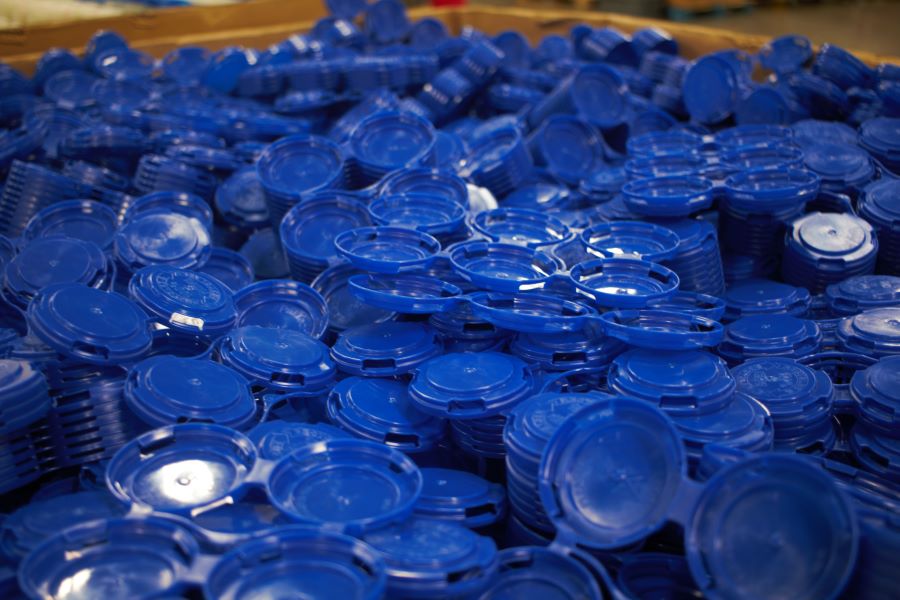
Marissa Heffernan/Resource Recycling
Levy said he prefers the language in Maryland’s EPR law, which calls for waste reduction, and Oregon’s, which focuses more on recyclability and increasing collection volumes.
“I don’t see how these states with these requirements are going to get to these recycling rates, because you’re reducing the demand driver for that material to be recycled,” he said.
Part of the problem is legislators not hearing enough from those in the industry, Levy added.
“When we’re talking to legislators and policymakers, they say, ‘Well, you’re plastic, so you must be bad. Oh, you’re fiber, oh, you must be good,'” he said. “But then when you show them the science and you show them the LCA, it kind of blows their mind” that in some applications and metrics, plastics outperform fiber.
Shook added that what PakTech is working to communicate is the danger of creating source reductions “that push us out of the marketplace.”
Most of the work is on education and exposure, because “there’s a lot of myths out there as far as plastics go and packaging,” Shook added.
Levy added that it’s now a question of behavioral change.
“We just want to make sure that people just don’t look at plastic as inherently bad,” he added, because “every material has got its purpose. Let’s use the right material for the right packaging purpose.”