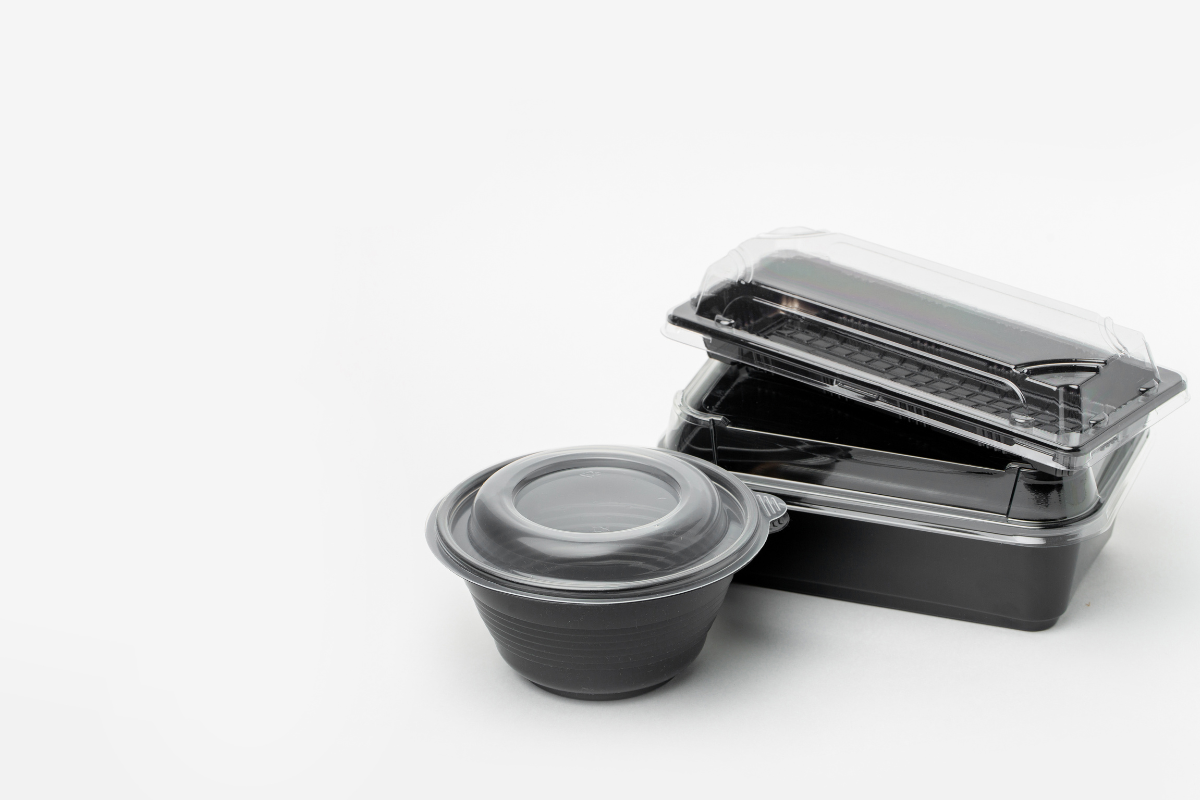
Retan/Shutterstock
As global virgin plastic production outpaces demand and utilization rate percentages linger in the low 70s, the next four years are expected to see downward pressure on the price of virgin plastics. Added to this, tariffs on U.S. plastics trade flows are likely to disrupt domestic supply chains, further complicating an already volatile market.
In response, the plastics industry is doubling down on technological innovation and public perception, investing in mechanical and chemical recycling while actively working to reduce its carbon footprint. At the same time, growing extended producer responsibility laws in states like California and Oregon and PCR mandates in New Jersey are accelerating the demand for sustainable packaging solutions with increased recycled content.
Against this backdrop, one of the most prolific yet least recycled plastics, rigid and flexible food-contact PP, has the potential to play a significant role in meeting both regulatory requirements and corporate sustainability goals. To better understand how, we first need to take a step back to understand why closing the loop on food-grade PP pots, tubs and trays is crucial yet so challenging.
Traditionally, recycling has focused on bottles – starting with glass beer bottles all the way through to PET and HDPE bottles – whose recycling journey is now well entrenched around the world. When these single-use bottles first came to market, they did so with the premise that they would be recycled – something that did not occur with other forms of plastic packaging such as pots, tubs and trays that were deemed to be trash, as they did not fit the traditional recycling model.
As such, one of the challenges in the U.S. is the misconception of what is recyclable and what is trash, and there are several key factors that reinforce this.
Re-thinking ‘unrecyclable’
It starts with municipalities that are not collecting PP pots, tubs and trays – PTTs – because of historical precedents and being unaware of the potential value and demand from recycling processors and brand owners.
To address this, we need a strong interaction with local authorities with instructions to recycle – there needs to be space made in the recycling stream for PTTs, which would include PET, because even PET pots, tubs and trays are slipping through the recycling stream.
This requires getting MRFs on board to dispel the notion that collecting PP would dilute the value of the recycling stream. The challenge here is that currently landfilling is seen as the simpler and certainly cheaper option.
There is a crucial role here for waste management companies, with support from organizations like Closed Loop Partners and The Recycling Partnership’s Polypropylene Recycling Coalition, to develop the infrastructure for collecting PP products. Since PP packaging is seen as the smaller fraction, many MRFs don’t yet have the right sorting station to separate out PP.
Historically, a MRF sorts PET and HDPE, representing approximately 80% of the total volume of plastics. The remaining volumes are about 15% PP and 5% other unsorted plastics. Certainly PP is currently a smaller fraction of the plastics stream, but PP collection volumes could increase substantially if there was an active focus on PTTs.
Forecasting US trends
If we take the U.K. as an example of what occurs when the focus is on extracting the value of food-contact PTTs out of the waste stream, we can forecast a positive outcome for the U.S.
According to RECOUP’s 2024 U.K. Household Plastic Packaging Collection Survey, collection rates for PTTs have increased since 2013, when they were at 20%, to around 174,000 metric tons of PTT collected, equivalent to a collection rate of 40%. As of April 2024, 89% of U.K. local authorities now provide a curbside collection scheme that includes PTTs. As a consequence, we are seeing a marked reduction of general waste collection and an increase in plastic and paper collection.
Risks of not creating plastics’ circularity
In fact we are now also seeing a stronger tendency towards the paper-fication of packaging as retailers shift to plastic alternatives such as paper and aluminum. The plastics industry is actually harming itself by not creating a circular economy for food-grade PP, as it risks being overtaken by alternatives that actually have higher carbon footprints in the long run.
PP is a major packaging material – in the U.K. it represents two-thirds of the consumer packaging per weight, and given that bottles are heavier than the PTTs, this means their volume is greater. As such, it should not be ignored. It is eminently recyclable and has numerous applications.
What is lacking is the incentive and acknowledgement of the value of recycled PP from packaging.
Once councils collect the PTTs and MRFs agree to sort them, the next step is to ensure there is a market for them.
Although the traditional market for recycled PP started with what we call the commodity market – ordinary applications such as shipping pallets, crates and many other non-food rigid products – the tipping point for successful recycling requires going beyond these very generic, price-competitive applications to closed loop systems that increase the incentive to recyclers.
Solutions to re-shape R-PP circularity
Of course this comes with its own set of challenges, as recycling post-consumer PP to food-grade compliance standards is a technically demanding process that requires more intensive investment, not to mention a new approach that embraces making high-quality food-grade R-PP.
Yet addressing the recyclability of all plastics – particularly food-grade R-PP – offers the best business case for expanding infrastructure and local recycling capacity.
And the good news is we have proven, science-based processes to recycle post-consumer food-contact packaging back into R-PP resins that are safe to turn back into food-grade R-PP packaging.
In turn, this will create the required incentive for processors.
Design for recycling must align with circular economy requirements
It is clear that to address the more complex circular economy recycling issues, we must continually reassess our guidelines for designing for recycling, re-aligning with the latest recycling technologies to overcome the hurdles.
Ideally packaging should minimize the use of pigments wherever possible and ensure that any pigments used are stable and non-reactive after multiple recycling processes. This issue has not received a lot of attention so far. However, it is key to ensuring recycled PP and other plastics remain suitable for new contact-sensitive products such as food packaging, health and beauty products and cosmetics.
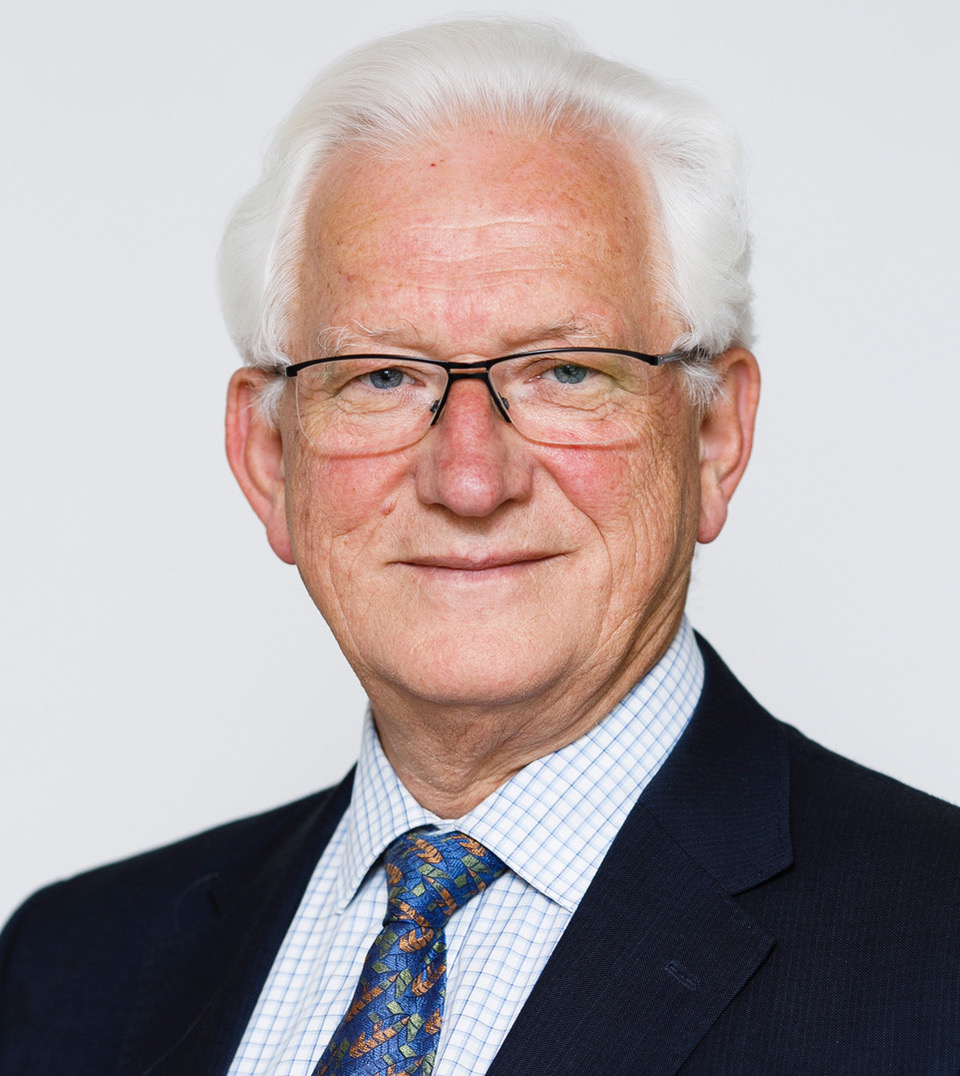
Edward Kosior
It is important to ensure that all decorative materials on packaging are totally removable, from labels to inks and binders.
NextLooPP participant Bostik, for example, has developed the next-generation range of wash-off label solutions for PP, HDPE and PET in Europe.
Another participant, MCC Verstraete’s NextCycle IM technology, addressed the issue with its NextCycle removable in-mold labeling solution tailored for rigid PP packaging. HydroDyn, a cleaning technology company, has developed an approach for removing labels, adhesives, inks and other contaminants from recycled plastics, which can eliminate up to 99.9% of extrinsic contaminants.
As we continue through the plastics supply chain, virgin resin producers will benefit as they tap into the unique opportunity of getting involved with recycled materials and becoming suppliers of complete packaging requirements.
Edward Kosior has worked in the plastics recycling sector for 48 years, including 22 years as an academic and 26 years working in recycling and sustainable solutions. He’s the founder of the consulting organization Nextek Ltd.; of NextLooPP, a global project working to close the loop on post-consumer polypropylene; and of COtooCLEAN, which uses a unique super-critical CO2 technology to decontaminate, de-ink and delaminate soft plastic films back to food-grade compliance.
The views and opinions expressed are those of the author and do not imply endorsement by Resource Recycling, Inc. If you have a subject you wish to cover in an op-ed, please send a short proposal to [email protected] for consideration.