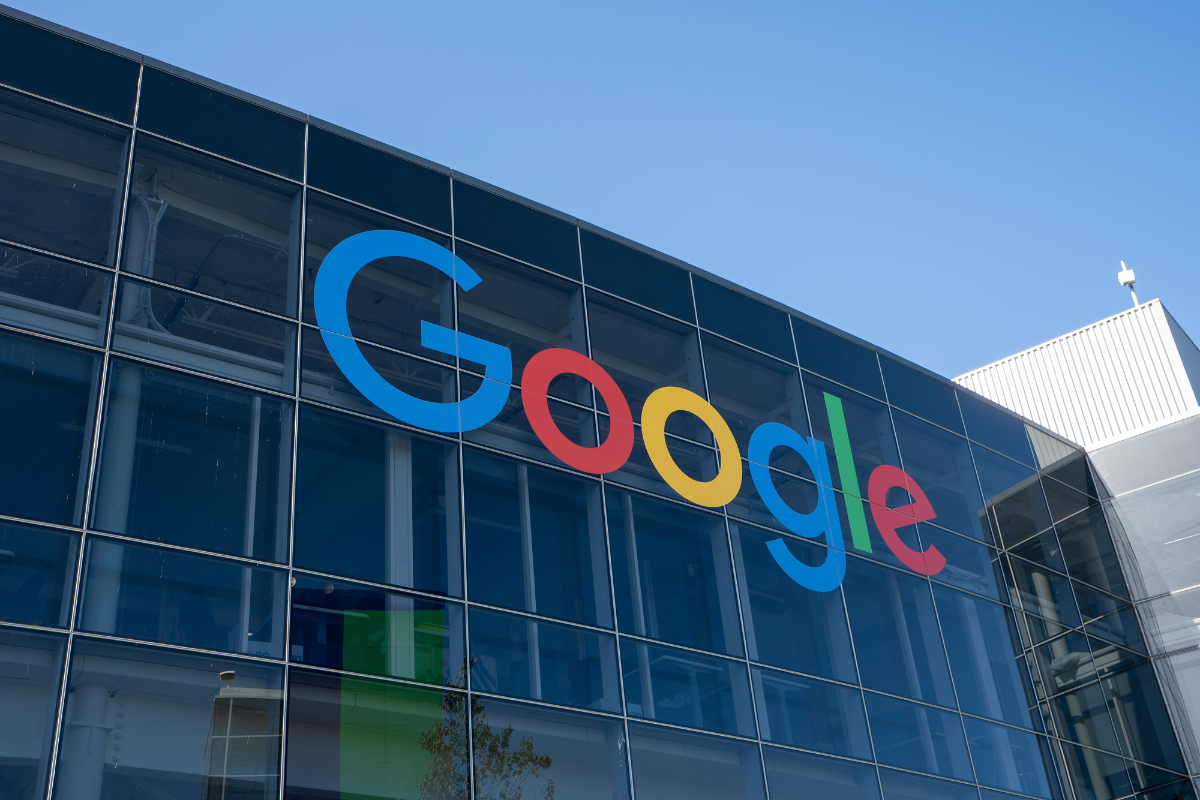
The “Plastic Free Packaging Design Guide” focuses on how Google has moved toward fiber-based packaging and away from plastics in its consumer electronics products. | Tada Images/Shutterstock
Google this month published a comprehensive look at how the company has approached designing its packaging for minimal plastic use. In publicly detailing its methodology, the major corporation laid out a philosophy that “sustainability should be a collaborative endeavor, not a competitive one.”
The “Plastic Free Packaging Design Guide,” published June 10, focuses on how the company has moved toward fiber-based packaging and away from plastics in its consumer electronics products. It lays out the many considerations that go into such a change.
“Transitioning to plastic-free packaging and moving away from mixed material packaging formats demands a rethinking of traditional components,” the company wrote. “Achieving the necessary product protection, accessibility, aesthetic appeal and responsible disposal – all while managing costs – required expansive material exploration and testing.”
The report walks through the common types of plastic packaging Google has traditionally used, including plastic laminations, shrink wrap and thermoformed plastic trays, and it describes the pros and cons of using those traditional products.
For instance, the company reported that PP laminated packaging provides substantial structural strength, scratch resistance, moisture protection and visual appeal from the finish. But, the company noted, when PP is laminated to paper packaging, it can disrupt the paper recycling stream.
“During the pulping process, the plastic film does not break down like paper fibers,” the report explains. “Instead, it must be screened out, ultimately contributing to landfill waste and reducing recycling yields. Large pieces of PP film float to the top of each recycling batch while small pieces are continuously strained out by size with a pressured screen and by density with cyclone cleaning.”
The company tested several alternatives and has found success with an ultraviolet varnish from ink supplier Megami. Google ran recycled pulp from its Megami-coated packaging versus the packaging that included the traditional PP laminate, and it found the material passed both lab tests and real-world operational tests. The standards, which were drawn from the Fibre Box Association, looked for a minimum 80% fiber yield, adequate deinking and the lack of remaining paper contaminants like waxes, coatings and soft adhesives, in the repulped fiber.
With those positive tests, the Megami varnish has been “successfully implemented at scale,” Google reported.
The 69-page report includes similar trial and replacement stories for the varied packaging products the company uses.