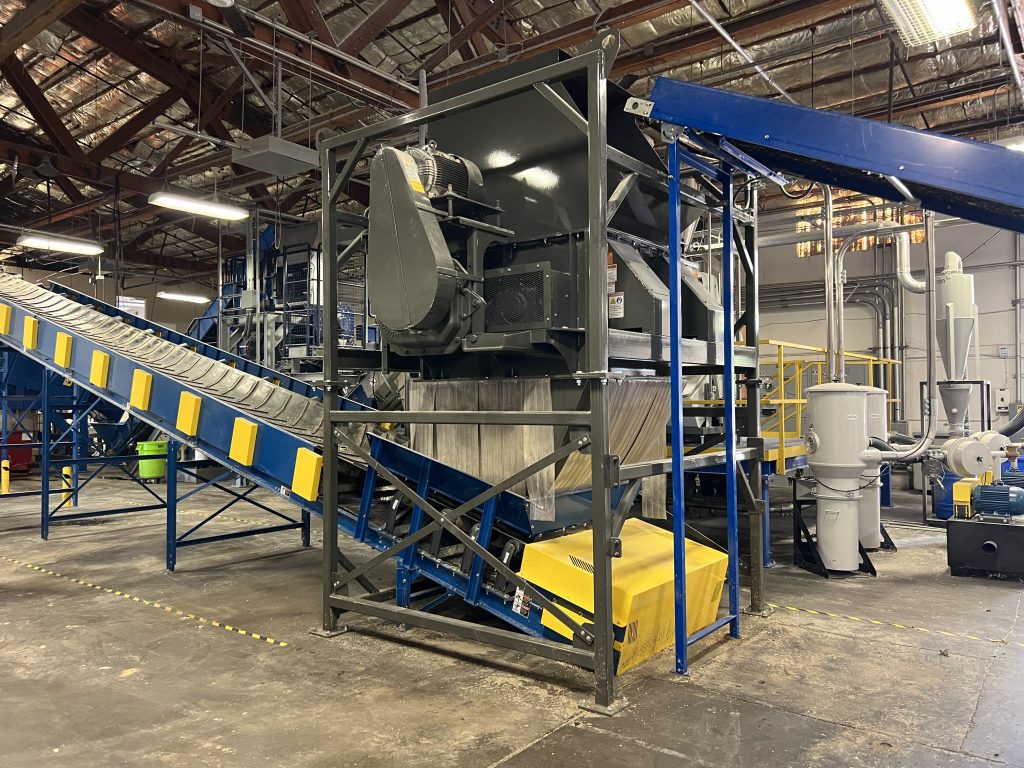
Innocycle shreds and washes used PET cages at its California reclamation plant. | Photo courtesy Innocycle.
Innovive, a U.S. manufacturer of single-use plastic cages for mice and rats in laboratories, has scaled up its recycling operations in recent years, nearly doubling its annual processing capacity since 2020 and building an in-house reclamation center in Sacramento, California.
The San Diego-headquartered company, which launched in 2004, makes rodent cages – known as vivariums or individually ventilated cages (IVCs) more technically – for use by a variety of research operations and similar customers. The cages are made from PET, with the bedding inside made from organic material. Innovive, which has offered recycling for its products since its inception, operates a sister company, Innocycle, that collects and recycles used cages from customer facilities.
Innovive’s recycling efforts have been increasing each year: The company processed 1.2 million pounds of PET in 2023, up from 1.1 million pounds the prior year. The company announced the latest numbers on Jan. 30.
Much of the growth has come in the last few years – Innovive nearly doubled its processing volume since 2020 and increased by 48% in one year alone, from 2021 to 2022, when the company opened a dedicated Sacramento reclamation facility. Prior to developing its own reclamation plant, the company operated a smaller prototype processing line and partnered with other companies to scale up its recycling capabilities.
The new facility and expanded processing capacity received a boost from grant funds awarded by the California Department of Resources Recycling and Recovery (CalRecycle). In awarding the grant, CalRecycle noted Innovive’s project “will expand existing recycling to 75% of cages sold in California.”
The facility totals 30,000 square feet and has a current capacity to process 8 million pounds of PET per year, a company spokesperson told Plastics Recycling Update.
Customers participating in the recycling program are asked to stack used cages and aggregate them in their original bags, and an Innocycle truck will come to collect them. The bags are delivered to Innocycle’s reclamation plant.
There, the bedding is separated from the cages, which are then shredded and washed to produce recycled PET flake. The bedding, meanwhile, is sent to an industrial composter.
The facility uses plastics and organics separation equipment from Scott Equipment, flake processing and cleaning machinery from Lindner, and a flake optical sorting system from Tomra.
Nearly all the recycled flake output is sent to a network of vendors who produce Innovive’s products. Innovive uses recycled PET flake from recycled cages at levels of more than 30% recycled content in its new products, and it also uses RPET purchased from other suppliers.
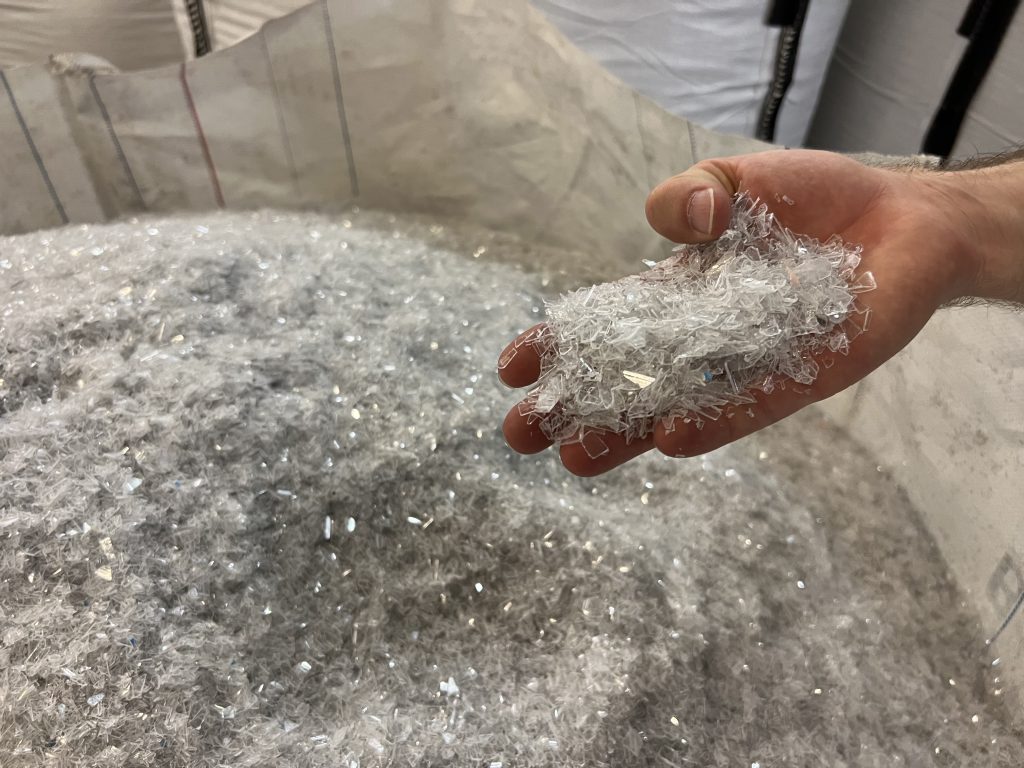
Innocycle’s washed PET flake is used to produce new PET cages. | Photo courtesy Innocycle.