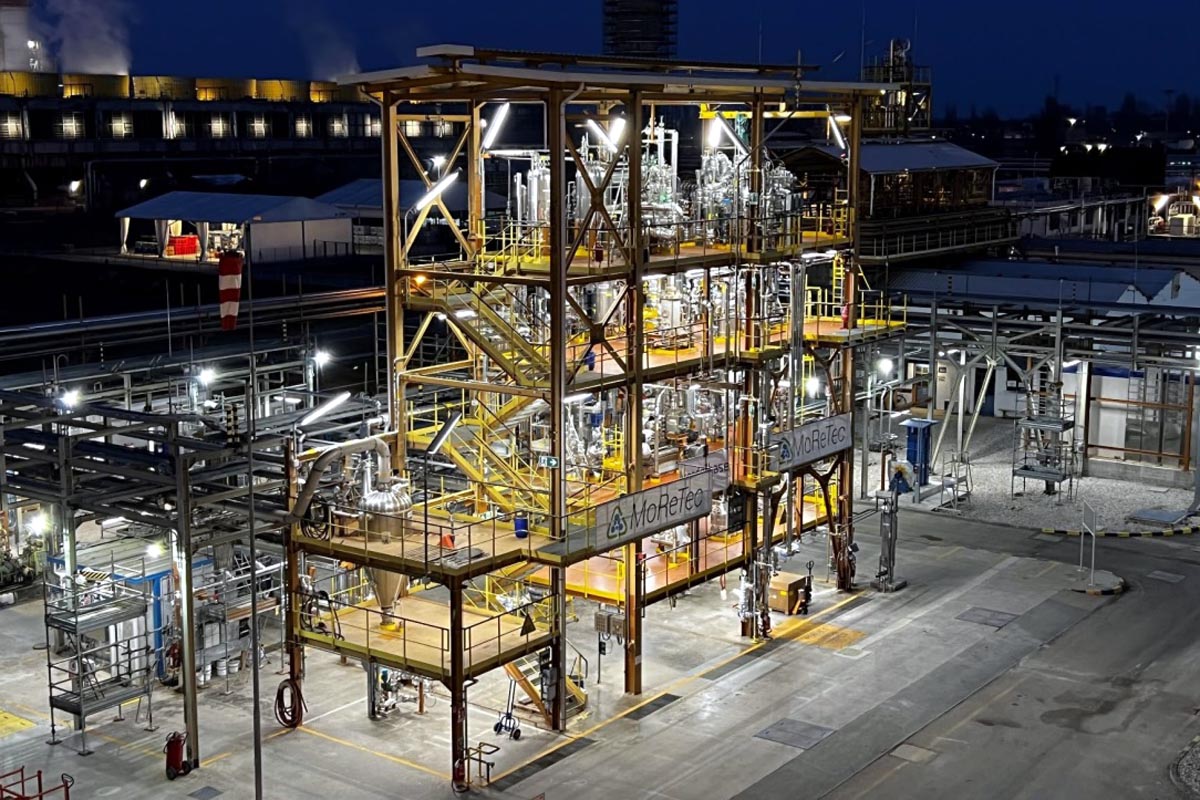
LyondellBasell’s MoReTec equipment. | Courtesy of LyondellBasell
LyondellBasell says its chemical recycling technology presents environmental benefits over competing pyrolysis processes, particularly because the company can use both the liquid and gas outputs as feedstock for new plastics.
One of the world’s largest polyolefins producers, LyondellBasell, held a Sept. 26 webinar to showcase MoReTec, which stands for Molecular Recycling Technology. That’s the name of its proprietary chemical recycling technology, which breaks down post-consumer scrap plastics to produce chemicals that are used to make new plastics.
While hyping the benefits of MoReTec, the executives also acknowledged the current-day shortcomings of chemical recycling – which they called “advanced recycling” – in general.
“When we look at the current landscape for advanced recycling, we see it’s in early stage and limited, and it’s faced with higher costs than mechanical recycling. It’s struggling to reach commercial scale as it goes through its learning curve, and it has lower energy and carbon efficiency,” said Yvonne van der Laan, executive vice president of Circular and Low Carbon Solutions at LyondellBasell. “As LyondellBasell, we recognize these challenges and are tackling them piece by piece with our integrated hub approach that allows us to build scale, reduce operating costs and capture value.”
During the webinar, which was broadcast from LyondellBasell’s R&D Center in Ferrara, Italy, where the company has a semi-industrial-scale MoReTec plant, van der Laan and Jim Seward, executive vice president and chief innovation officer at the company, explained the competitive advantages of the technology, as well as plans to scale it up in Europe and the U.S.
Catalyst reduces energy usage
Pyrolysis, which involves heating plastic in the absence of oxygen, breaks polymer chains in plastics to produce gas and liquid fractions, as well as some percentage of solid contaminants. The gas is often burned to produce energy to heat the process. Environmentalists have pointed to that reduced yield and combustion when they criticize pyrolysis as inefficient and polluting.
“Pyrolysis is actually a fairly relatively intensive-energy-using process, but we are applying our long history of catalyst development in this space as well, looking at how we can convert polymers back to monomers,” Seward said in his presentation.
The MoReTec pyrolysis process is able to use the gas fraction to produce new plastics, as well as the liquid, further displacing fossil-based feedstocks, he said. By using its catalyst, MoReTec lowers reaction temperatures, which reduces energy usage, and improves the plastic-to-plastic yield.
Seward said that recovering gas for use as feedstock rather than fuel yields Scope 1 greenhouse gas generation benefits, using electrically heated systems and lower temperatures lower Scope 2 emissions, and replacing fossil-based feedstocks with scrap plastic reduces Scope 3 emissions.
“Combining all of this, we believe the pyrolysis feedstock produced from MoReTec has less than 50% of the carbon footprint of fossil-based feedstocks,” Seward said.
He acknowledged that purification of the pyrolysis oil and gas outputs will be required if they make up higher and higher percentages of the feedstock going into the company’s ethylene crackers, where they replace naphtha and natural gas liquids.
“This is an element of our industrialization path,” he said.
The crackers then process the inputs into monomers, which are fed to existing polymerization plants to be made into new plastics for use in demanding applications, such as food and healthcare packaging, according to the presentation.
Plans for scaling up
In terms of scaling up, Seward said LyondellBasell is first looking to build a plant near Cologne, Germany, capable of processing 50,000 tons per year, with a final investment decision on that project likely to come before the end of this year. If approved, that plant would be scheduled to come on-line in 2025.
Then, the company will likely move its attention to a larger MoReTec unit – one capable of producing 100,000 tons per year – at its Houston refinery, he said.
“We anticipate MoReTec units within each of our integrated hubs,” he said.
Van der Lann said LyondellBasell currently plans to continue operating its Houston refinery until the end of the first quarter of 2025. Before that date, the company will decide on repurposing assets from the refinery to create MoReTec 2 there.
Globally, LyondellBasell has a goal of marketing 2 million tons of circular and renewable-based polymers by 2030. They’re sold under the company’s Circulen brand portfolio. Last year, the company sold less than 80,000 tons of Circulen plastics, far short of its goal.
Looking forward, LyondellBasell projects the Circular and Low Carbon Solutions business will generate an additional $1 billion in earnings before interest, taxes, depreciation and amortization (EBITDA) per year starting in 2030.
Van der Laan said LyondellBasell has marketed over 220,000 tons of recycled and renewable-based plastics so far, although the majority has been mechanically recycled resin and renewable-based plastics, which include non-fossil-fuel-derived feedstocks such as used cooking oil. LyondellBasell projects that, by 2030, about half of the sales in that business will come from chemically recycled plastics, branded CirculenRevive, as well as renewable-based plastics, branded CirculenRenew. Revive will include both recycled plastics produced by LyondellBasell and purchased from third parties.
She said the company is estimating about 15% of its annual capital expenditures will go to building out the recycling technologies, of which MoReTec is a key part. The 15% includes upstream scrap sorting and processing needed to produce feedstock for MoReTec. A joint venture LyondellBasell is a partner in, Source One Plastics, is currently building a feedstock preparation facility in Wesseling, Germany, near Cologne. That plant will supply 70% of the feedstock needed for the Cologne MoReTec unit.
Van der Laan and Seward emphasized that they foresee healthy profit margins for the chemically recycled resins, given projections for a continuing supply-demand imbalance and the company’s competitive advantage from its ability to scale up the efficiency of its process.
From a smaller MoReTec plant (50,000 tons or so), the company projects a cost advantage of between 10% and 15% compared with other chemically recycled resins, she said. From a larger plant, such as the one contemplated for Houston, LyondellBasell anticipates a cost advantage of 30% to 50%.