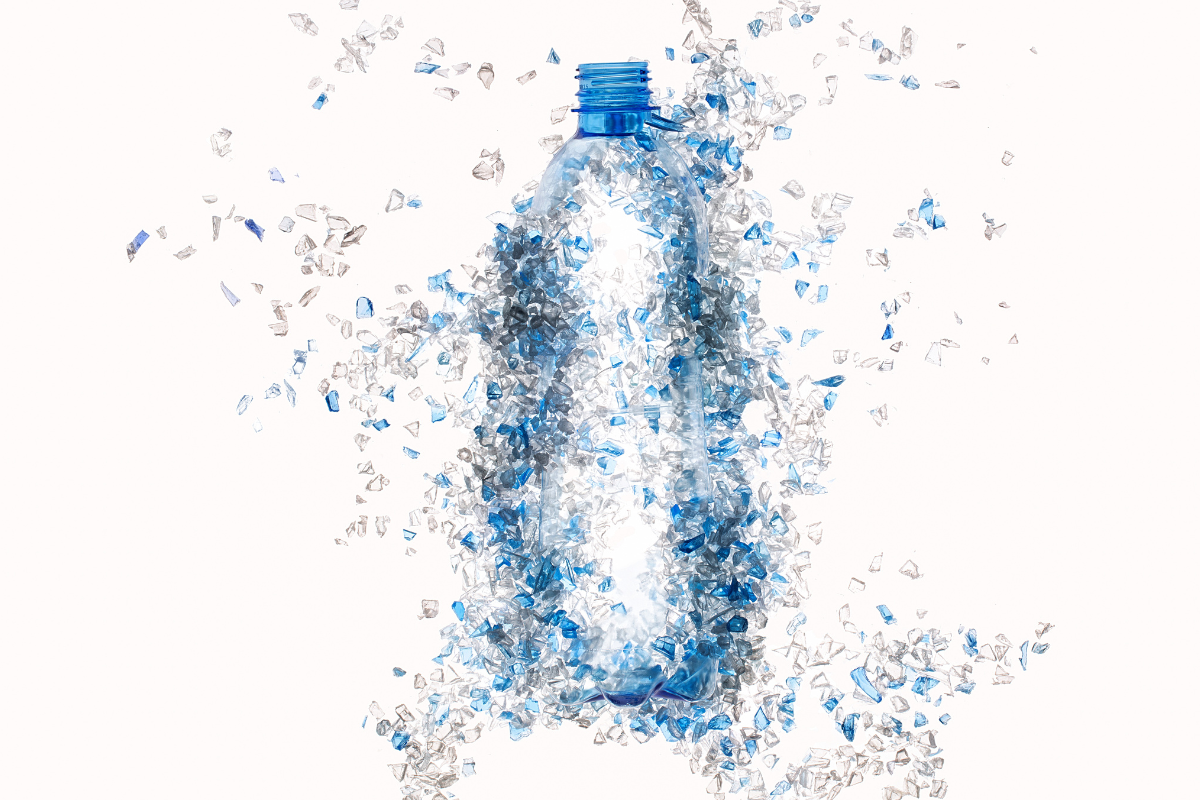
Study authors evaluated three categories of chemical recycling technology and found that the “purification” category yielded the highest PCR return. | Vitte Yevhen/Shutterstock
As with many emerging technologies, chemical recycling goes by a variety of names, including “advanced” and “molecular” recycling. A study from Closed Loop Partners dug into the differences.
The study, titled “What Is Chemical Recycling, Why Does It Have So Many Different Names, And Why Does It Matter?” is the result of 18 months of study into the environmental impacts and financial viability of several types of chemical recycling technologies, a press release noted, undertaken with the goal of understanding “how and if these diverse technologies can fit into a circular future for plastics.”
The overarching finding was that chemical recycling technologies can be sorted into three distinct categories: purification, depolymerization and conversion.
“Molecular recycling is a broad umbrella term – also referred to as chemical recycling or advanced recycling – that encompasses dozens of technologies that use solvents, heat, enzymes and even sound waves to purify or break down a wide range of plastic feedstocks to create polymers, monomers, oligomers or hydrocarbon products so that they can re-enter manufacturing supply chains, instead of going to landfill,” the report noted.
It added that the technologies should only be considered circular when the supply chains produce a final product, which excludes fuels.
“Molecular recycling is a group of technologies that can complement mechanical recycling and help widen the aperture of plastic waste that we can recycle today,” the report concluded, adding that it is “not a silver bullet but plays an important role in creating a waste-free future for our hardest-to-recycle plastics,” especially non-single-use and non-packaging plastics.
However, more upstream and downstream solutions are needed, according to the report, including design, reuse and better policies.
Crunching the numbers
The study evaluated nine technological processes. In terms of total packaging volumes accepted across the United States and Canada, the study found that conversion technologies could accept 82% of all plastic packaging produced – more than mechanical, purification or depolymerization technologies could alone.
“These types of technologies also can process mixed plastic waste, while purification and depolymerization requires a sorted and single-resin feedstock,” the report added. “Because feedstock can be mixed, conversion technology companies are often paid to take feedstock rather than paying for feedstock.”
However, the researchers noted that when looking at the amount of PCR each category can yield, conversion technologies “have the longest route back to becoming plastic.”
The study authors estimated that If 1,000 kilograms of plastic feedstock went into each of the three technologies, purification would yield the highest volume of PCR, showing an 88% material processing efficiency. Conversion technologies yielded the lowest amount, showing a 42% processing efficiency.
“The capacity to move away from virgin plastics requires the recycling sector to be as efficient as possible,” the report stated.
Through an environmental lens, purification and depolymerization technologies had smaller environmental footprints on average, the report found, taking into account energy use, greenhouse gas emissions and water impacts.
Looking at the economic viability of the technologies, based on cost and accessibility of feedstocks and the market demand for the products, the study found that of nine technology companies, seven had a positive internal rate of return in the 2021 base case. That’s noteworthy “given that our base case assumes that these technologies are expected to sell their outputs at market commodity prices without a premium,” the study noted.
The study concluded that the chemical recycling sector is “incredibly nuanced and diverse” and due diligence before investing is critical.
“The opportunity for consumer brands, policymakers, and investors is to collaborate to develop a vision of success for this sector,” the study stated.