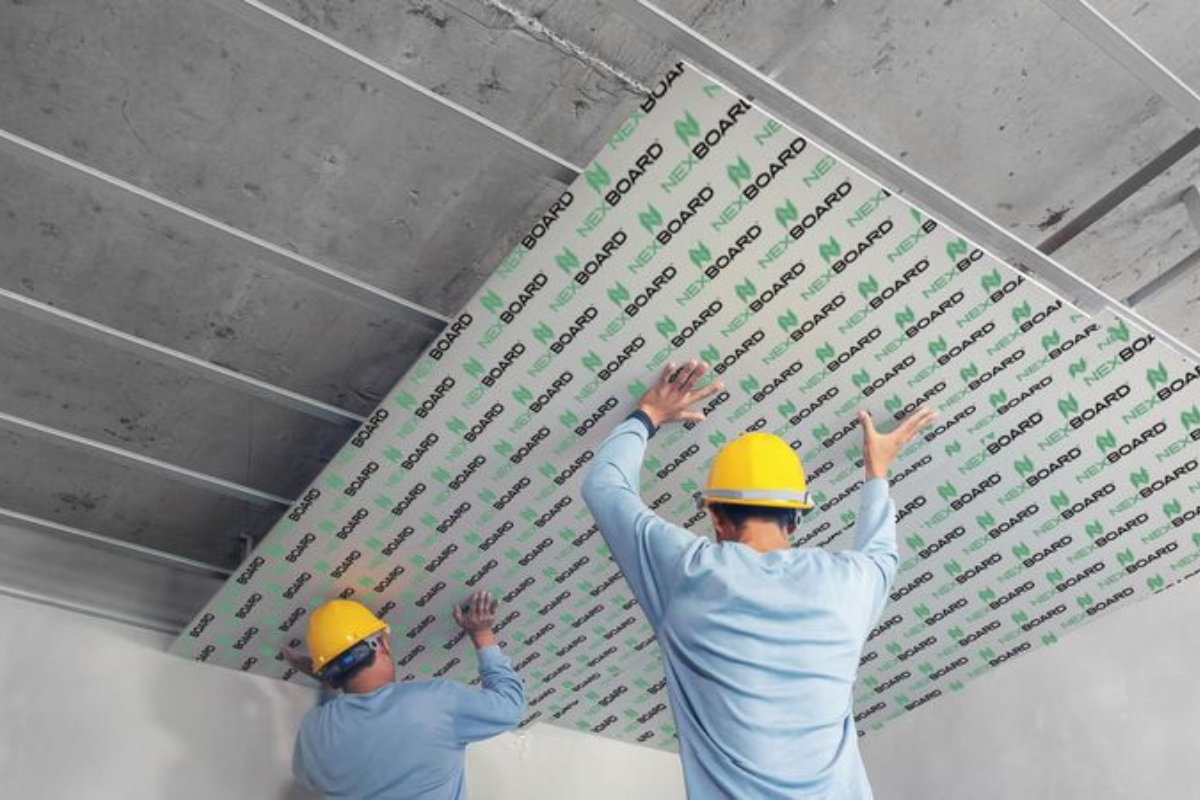
Before commercializing its fire- and mold-resistant construction board, Xeriant plans to secure financing and expand its production capabilities. | Courtesy of Xeriant
Material development company Xeriant is putting the finishing touches on its recycled composite construction panel, which it hopes will “disrupt” the building industry.
The Florida-based company, which partnered with TMF Corporation to develop Nexboard, said it has successfully tested high-volume production for the board, which is made largely from post-consumer and post-industrial plastic and cardboard.
Billing it as a replacement for drywall and wood-based building products, a press release stated that patent-pending Nexboard is resistant to fire, water, mold and insects.
Xeriant’s manufacturing technique will allow the product to be competitively priced, the press release added, “while delivering the quality and uniformity required for successful integration into the construction industry.”
Keith Duffy, CEO of Xeriant, said in the press release that the board’s manufacturing process uses automation technology and that Nexboard will “disrupt the building materials industry.”
“The industry is desperate for a viable green alternative to gypsum board as part of a transition toward greater efficiency, safety and sustainability in building design,” Duffy said. “Drywall has essentially remained unchanged for over a century and is extremely vulnerable to moisture and mold.”
Continuus Materials and WM have been working on a similar project to turn mixed paper and plastic into roofing material.
Reaching the starting line
Xeriant’s next step is commercialization. Another press release noted that samples of Nexboard have been sent to builders, whose feedback will be used to adjust the composite mix to optimize weight, strength and fire resistance.
The company is also looking to secure financing to build out equipment and facilities and set up “a robust supply chain by forging relationships with reliable sources of large quantities of post-industrial plastic and cardboard waste.”
Duffy added that “over the past few months, we have been extensively analyzing and testing various production methods to identify the optimal and most cost-efficient process.”
“Simultaneously, we were positioning Xeriant on the best possible footing to advance the commercialization process, as we meet certain product development milestones,” he said. “Now that we have established an industrial-scale solution, we are able to execute a path to mass production and sales.”
A version of this story appeared in Resource Recycling on July 31.