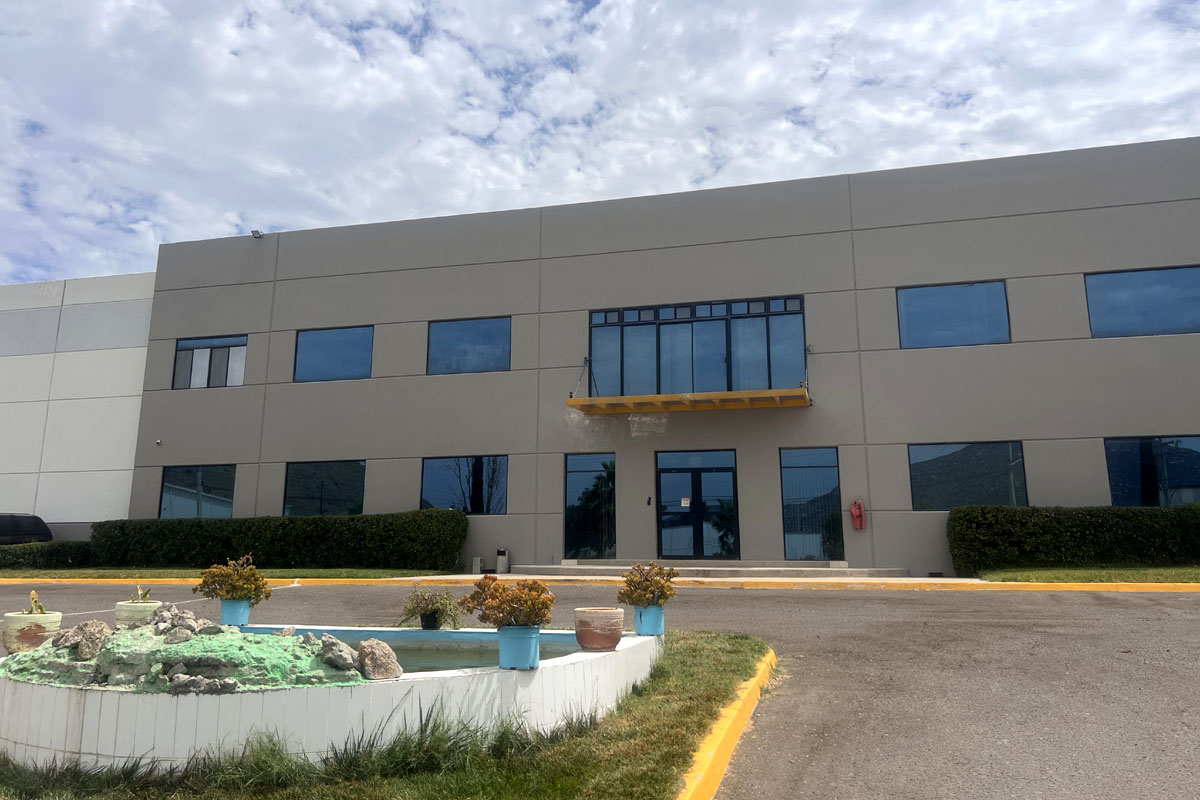
Leaders at Polyfit hope to take advantage of a changing legislative landscape that is creating demand for film that contains PCR. | Courtesy of Polyfit
Plastics reclaimer Polyfit invested up to $7 million expanding its campus in northern Mexico, boosting its polyethylene recycling capacity at a time of rising demand in the U.S.
The Chino Hills, Calif.-based company in December opened a 160,000-square-foot facility in Tecate, Mexico, growing the company’s total North American LDPE/LLDPE pellet production capacity to at least 120 million pounds per year, company leaders told Plastics Recycling Update.
Douglas Miner, Polyfit’s vice president of sales and marketing, said the company is responding to rising demand for PCR.
“Most of that is driven by the brand owners themselves saying that we have to have X percent in there,” Miner said. “They know the legislation is coming. You’ve got the consumer saying they want to be responsible, and we want to be responsible for getting the plastics recycled and increasing the recycled content.”
Polyfit, which was founded in 1986 and also has plastics recycling facilities in Southeast Asia, serves the U.S. market from its campus in Tecate, which is just east of Tijuana and roughly an hourlong drive from San Diego.
Product of several expansions
The Tecate campus has undergone several expansions in recent years.
The first facility, at around 120,000 square feet, opened in 2020. The following year, it was expanded by 60,000 square feet to add a sorting line and provide space for other feedstock preparation steps. Later, Polyfit merged a warehouse adjacent to the building, expanding it to 250,000 square feet total.
That large building is where most of the LDPE/LLDPE recycling occurs, with a capacity of up to 72 million pounds per year, said Hunter Leung, Polyfit’s CEO and a member of the family that owns 100% of the company.
In December 2021, Polyfit began construction on a new 160,000-square-foot building, which was completed in December 2022. Leung estimated Polyfit invested about $6 million to $7 million in that project, including installing processing equipment, a wastewater treatment system, fire systems, air filtration equipment and more.
The new building is focused on HDPE and PP recycling, with the capacity to produce between 4 million and 6 million pounds a month, depending on the input mix, Miner said. The additional plant boosted the company’s total pellet production capacity to at least 120 million pounds per year.
Leung said Polyfit’s total capacity is roughly 72 million pounds per year of LDPE/LLDPE, 30 million pounds per year of PP, and 18 million pounds per year of HDPE. He noted that the new building also provides space to allow a future doubling of LDPE/LLDPE pellet production capacity, to 144 million pounds a year, “if the demand is out there.”
The Tecate campus employs over 400 people, Leung noted, with the company relying on manual sorting. Miner said that highly trained manual sorters can produce cleaner film streams than optical sorters, and by the time the LDPE feedstock gets to the shredders, it’s 98% clean.
The company also uses “a substantial number of washing lines,” Miner said, adding that the washing equipment was designed in-house. The company also runs its plastic through two extruders, not one, and it sends the melt through screenpacks in a unique way that provides “very rigorous screening.”
“We have a very unique and proprietary process to get our end pellets out the door that we feel is the best in the industry, the cleanest,” Miner said.
The end result is a polyethylene pellet that can be used to blow film less than half a millimeter thick and with a very low gel count, he said.
Seeing increasing demand
Leung said Polyfit’s post-consumer feedstock comes from materials recovery facilities (MRFs), distribution centers and stores, other reclaimers and other locations. All is sourced from the U.S. and none comes from Mexico, he said, a requirement of the maquiladora program in which Polyfit is participating.
Miner and Leung said Polyfit is already a huge player in the bag market in California, where Senate Bill 270 banned thin carryout plastic bags but allows thicker reusable bags if they meet certain conditions, such as containing 40% PCR content.
Miner noted that Polyfit also sells a lot of LDPE/LLDPE for blow molding into film for consumer packaging overwraps, high-end garbage bags, bubble packaging, mailers and more.
Polyfit sees legislation as providing a bright outlook for PCR demand in the future. Miner noted that, in addition to California, other states have passed minimum recycled-content mandates as well, including New Jersey, Washington state and Maine.
Leung also pointed to California’s Senate Bill 54, the Plastic Pollution Prevention and Packaging Producer Responsibility Act, which establishes extended producer responsibility for plastic packaging, mandates sources reduction and specified recycling rates be achieved, and more.
Leung said SB 54 stimulates Polyfit’s closed-loop recycling programs run on behalf of retailers and brand owners.