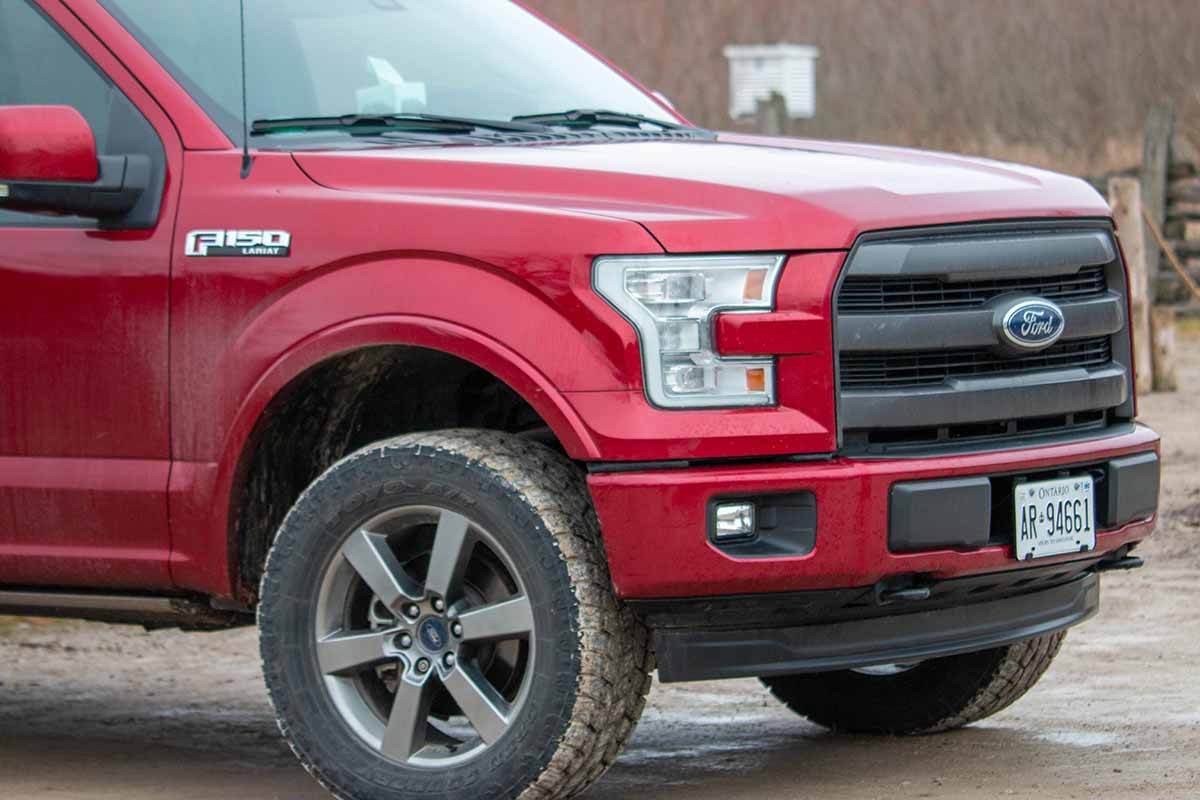
Researchers at Rice University turned milled-together bumpers, gaskets, carpets, mats, seating and door casings from Ford F-150 pickup trucks into graphene. | mynewturtle/Shutterstock
An experiment by Rice University and Ford turned mixed plastic from old vehicles into graphene, which was then used in a polyurethane foam for new vehicles.
Using a high-heat method called flash joule heating, the researchers turned milled-together bumpers, gaskets, carpets, mats, seating and door casings from Ford F-150 pickup trucks into graphene. Ford has used graphene in polyurethane foam composite since February 2020, to improve tensile strength and absorb low-frequency noise.
The polyurethane foam composite can then be “flashed” back into graphene at the end of its life, according to the study.
“Responsible disposal of vehicles at the end of life is a pressing environmental concern,” the authors wrote. “In particular, waste plastic forms the largest proportion of non-recycled waste material from light-duty vehicles, and often ends up in a landfill.”
Over the past six years, the report noted, the amount of plastic in vehicles has increased 75%, to about 770 pounds per vehicle, to reduce weight and improve fuel economy.
Using the flash heating method, about 30% of the initial plastic was recovered as “highly carbonized plastic,” the study said, with the other 70% outgassed. That resulting plastic was heated again and turned into graphene at about 85% of the highly carbonized plastic mass, meaning about 25% of the mass from the original plastic was recovered as flash graphene.
So far, most labs have been testing polyurethane recycling methods that involve pyrolysis processes. Those methods “require complex catalysts, inert atmospheres and they struggle to recycle dirty or mixed streams.”
Flash joule heating, on the other hand, is a solvent-, water- and furnace-free method that can be done at a projected electrical energy cost of about $125 per ton of plastic. Graphene, the report said, can retail at $60,000 to $200,000 per ton.
That simpler process also means flash graphene can be produced with fewer environmental impacts, the report said. The researchers found their method used far less energy and water and produced fewer greenhouse gas emissions than two other common ways of making graphene.
The flash heating process “is currently being rapidly scaled” to a production capacity of multiple tons each day, the report noted.
The study was published in the first issue of a new Nature journal, Communications Engineering. Researchers from Rice University and Ford’s Research and Innovation Center are authors, and it was funded by the National Science Foundation Graduate Research Fellowship program, the Air Force Office of Scientific Research and the U.S. Department of Energy’s National Energy Technology Laboratory.
More stories about research
- RIT researchers develop AI-based textile recycling system
- Researchers: Effective plastic treaty requires production cuts
- Research, programs improve film recycling access