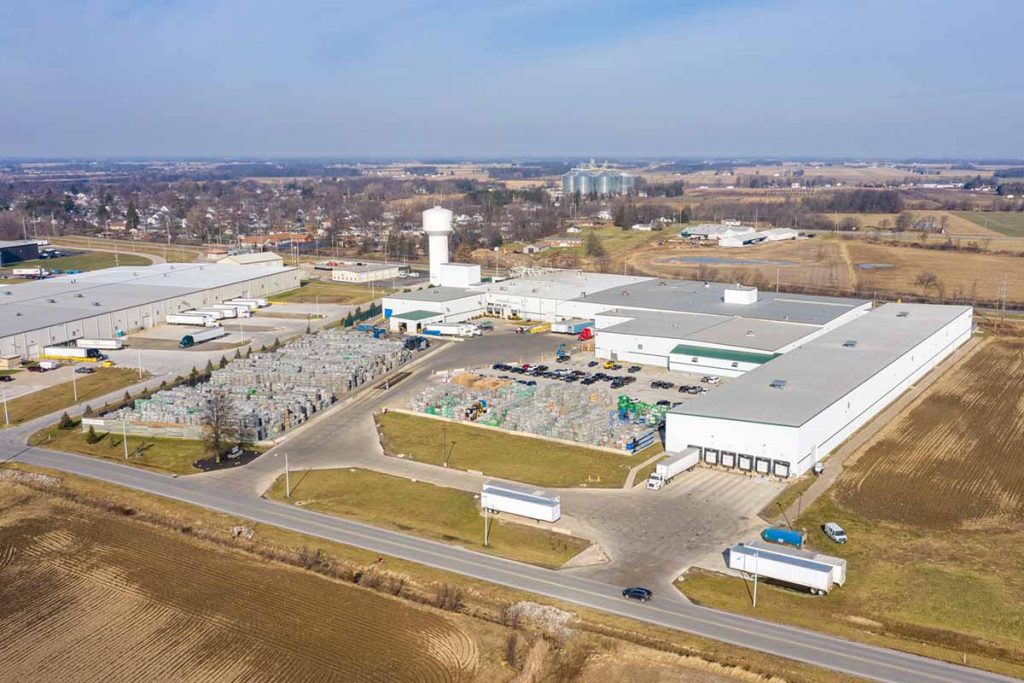
View of the Evergreen facility in Ohio.
A Midwest plastics recycling firm used Earth Day this spring as a platform to announce its plan to double its food-grade RPET capacity to 80 million pounds per year. A company leader noted the initiative harnesses “the latest and greatest technology.”
Clyde, Ohio-based Evergreen will install new extrusion line equipment, upgrade existing optical sorters and expand its building size as part of the project, which was officially announced on April 22. Clyde is located in north-central Ohio, about 75 miles west of Cleveland.
Evergreen is part of a company formerly known as Polychem Corporation, a manufacturer of load securement packaging products, including recycled PET strapping. As part of the Earth Day celebration, which included speeches, food and music at company locations, Polychem announced that it’s changing its name to Greenbridge and Evergreen Plastics is being renamed Evergreen.
Evergreen brings in about 100 million pounds per year of PET bales. It supplies colored PET flakes and pellets for its parent company’s production of strapping, and it can produce up to about 40 million pounds per year of clear food-grade RPET for sale to outside customers, including food and drink packaging producers.
Significant investment
First started in 1998, Evergreen’s capabilities and capacity have increased over the years. Its last major investment in extrusion capabilities was in 2011, when it added a second Erema pelletizing line and expanded its building.
Greg Johnson, who is vice president of operations for Greenbridge and who oversees Evergreen, said the company installed six robotic sorters in December 2020. Working behind the optical sorters, those robots, which were provided by AMP Robotics, are doing a final polish on the PET bottle stream, removing colored PET and contaminants such as other polymers, he said.
The newest project represents an even more significant expansion effort.
“Our current project in Clyde involves expanding both the facility and the capability again,” Johnson explained.
The $22 million initiative includes a number of improvements, Johnson explained. The 238,000-square-foot building will be expanded by 54,000 square feet, providing additional space for pelletizing. Crews were set to break ground on the construction in early May.
Evergreen currently has two Erema extruders with a combined capacity to produce up to 40 million pounds of food-grade RPET each year. The company will add Starlinger solid-state polycondensation (SSP) reactors to the end of both lines, he said.
Evergreen will also add a Starlinger pelletizing line capable of producing another 40 million pounds per year. It will also have a Starlinger SSP reactor.
“It’s a very large extruder,” he said. “That will be coupled with the latest and greatest technology, as well.”
Evergreen will also boost its optical sorting capabilities. It currently has three Pellenc bottle sorters and six flake sorters. Johnson said the company will work with suppliers to boost the object recognition capabilities for the three bottle sorters and upgrade four of the six flake sorters to the latest technology from Tomra. The improvements include black object detection and software for quantifying contamination.
The new equipment has been ordered, Johnson said, and the building expansion is scheduled to be completed early in the fourth quarter, after which point the new equipment will be installed. The project is expected to be complete by mid-2022.
Johnson explained that the company isn’t adding capacity to the front-end sorting and wash systems, which have exceeded the pelletizing capacity. As a result, Evergreen won’t need to immediately source additional bales of PET scrap to feed into the system, he said.
In addition to new equipment, Evergreen plans to continue growing the sustainability services it provides customers, Johnson said. Evergreen conducts sustainability audits and helps customers recycle their scrap materials by utilizing the company’s long-standing connections with other materials recyclers.
This article appeared in the Spring 2021 issue of Resource Recycling. Subscribe today for access to all print content.