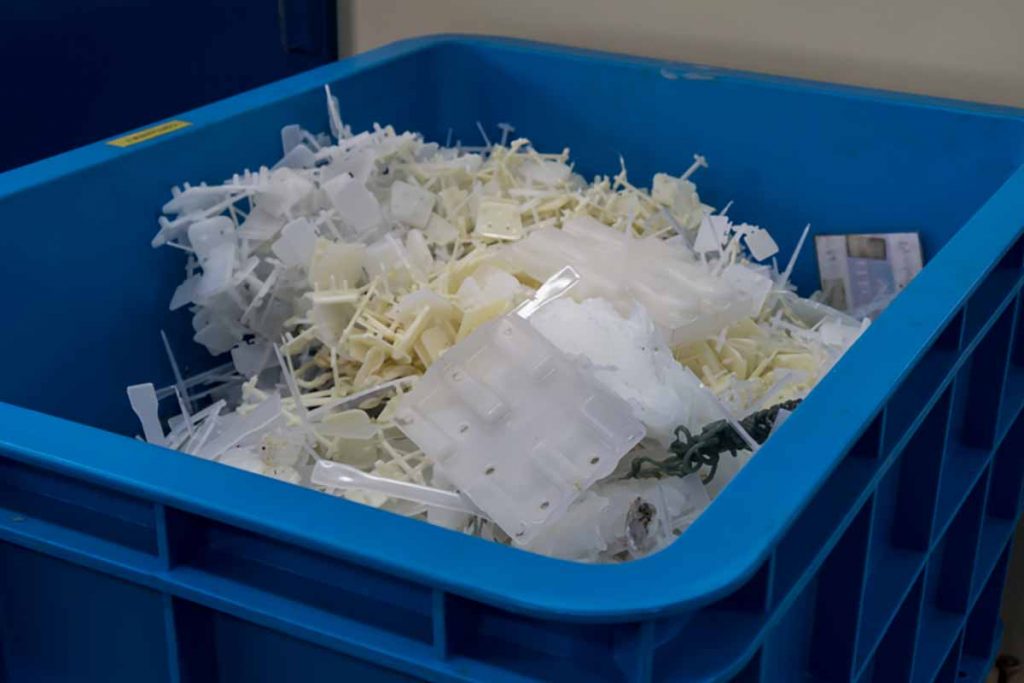
The author argues that post-industrial plastics recycling yields important environmental benefits and can help overcome challenges in post-consumer plastics recycling. | mofaez/Shutterstock
At GreenBlue, a national nonprofit focused on sustainable materials, we recently concluded a public comment phase as part of our development of the Recycled Material Standard (RMS). The RMS will define recycled content and verify that materials moving through the supply chain are, in fact, recycled.
As anticipated, the inclusion of certifying post-industrial materials garnered much attention. With much work to be done to bolster collection and markets for post-consumer materials, there may be some natural resistance to focusing on the post-industrial realm. We knew varying views would be heard from the start, and we welcome the opportunity to have this conversation.
Below are some of the main considerations our project has kept in mind when it comes including post-industrial material in the wider conversation about resin certification and wider plastics recycling enhancement efforts.
We have included post-industrial materials from day one
The very first time we met with the RMS Advisory Committee, this was the first topic on the agenda, and the first unanimous consensus decision. Because the parameters around post-industrial materials have remained largely undefined for decades, we recognized the necessity to offer clear definitions and examples for post-industrial materials.
The RMS is being developed for multiple materials across industry sectors. We’ve started with plastics and a focus on packaging; however, the standard will eventually be expanded for broader use across different sectors and additional materials.
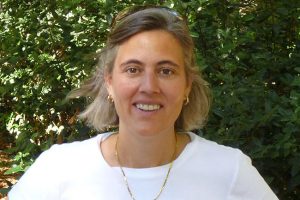
Laura Thompson
Circularity does not prioritize molecules
Whether using post-consumer or post-industrial materials, the use of either keeps valuable materials in play and displaces the need for virgin raw materials. Companies should consider both sources in goal setting and be transparent in reporting progress.
Is it prudent to cap targets at 30% post-consumer content? Or should we continue to aim high, putting post-industrial material to work and pushing for 50% recycled material – or higher? In some cases, the quality of post-industrial will allow for a higher content target.
We also need to keep an open mind about “open loop” recycling. There are many situations where closed-loop (for example, bottle to bottle) recycling simply can’t be accomplished, but allowing materials to flow to other market sectors keeps the molecules in motion.
We need an even playing field
Certifications create a set of rules that enable procurement teams to use common definitions and set clear expectations. By including both post-industrial and post-consumer materials in the scope of the RMS, the standard ensures that they can be tracked as separate materials. With a certification playbook, brands can more readily articulate needs to their suppliers and can focus their energy on other aspects needed to achieve ambitious goals. Clearly defined boundaries and tracking systems for both streams also enable accurate reporting so brands know how they are progressing on their goals.
Yes. And.
Yes, of course, the planet needs more access, sortation, market development and demand for post-consumer plastics. And the same can be said for post-industrial materials. There is a massive data gap on the current use of post-industrial materials. While it is often presumed that these materials are captured and put to use, there is ample evidence that it is not.
Equipment providers see continued growth in sales for post-industrial applications. Erema, for instance, shared a case study last year and emphasized the following: “While the general public isn’t all that aware of the potential for post-industrial plastic recycling, it actually represents an immense opportunity to divert usable plastics from landfills while enabling cost and energy savings for plastics products producers.”
We should act on facts and not be stifled by fear
The ultimate goal is displacing more carbon-intensive virgin materials. We have heard a lot of speculation about how the supply chain might react to certifying post-industrial materials. While it is important to consider unintended consequences, we can’t let worries stop progress.
We also cannot pick winners and losers in supply chains; instead, we need to consider a suite of solutions that will protect the health of our ecosystems. With the urgency of the plastics pollution challenge we face, there is no room for near-sightedness. The system needs to be holistically addressed and we must encourage action on all levels.
Life cycle thinking tells us that post-industrial materials often have less impact than post-consumer sources. Recycling post-industrial materials tends to result in higher yields (displacing more virgin material) and there is often less processing required (less need for transportation, sortation, cleaning, etc.).
It’s hard not to get emotional when we understand the challenges at hand. Change is hard, but progress cannot be made without it.
The plastic recycling system desperately needs innovation
Post-industrial processing uses a wider range of capabilities than what we see employed for post-consumer packaging. Technologies such as paint removal and metal and other material separation are being developed to meet the needs of specific sectors, like automotive. For example, advances in processing end-of-life vehicle bumpers are far more likely to come from the recyclers performing similar processes for post-industrial bumpers. Perhaps technology developed for paint removal will provide insights for ink removal from packaging.
Additionally, food contamination is a major challenge for some applications. It has taken herculean efforts to get consensus on acceptance of empty pizza boxes – just imagine the hurdles for flexible packages exposed to wet foods. However, Global Environmental Management Initiative (GEMI) has a project underway to tackle contaminated post-industrial plastics from the protein industry, which could eventually lead to solutions for post-consumer films. If collaborators can find solutions, we should reward those efforts with a certified stamp of approval. Go, GEMI, go! The future of recycling flexible packaging may depend on your success.
Recycling plastic is technically challenging
A recent comparison of beverage containers, summarized by the Can Manufacturers Institute (CMI), illustrated the current status of recycled content by material type, which provides insights to how challenging plastic recycling can be. While aluminum cans have reached an average of 73% recycled content (of which about one-third is post-industrial), PET bottles average just 6% recycled content.
The CMI article further explains some of the challenges associated with mechanical recycling of PET: Each cycle affects the basic properties of the plastic. Materials change color and lose clarity, and volatile materials can migrate. In other words, every heat history, for both post-consumer and post-industrial plastics, further degrades the plastic molecules, and contaminants just exacerbate the problems. Use of post-industrial materials can require the same clever compounding solutions presented by post-consumer materials. Both require innovation.
Think of the entire system
With these challenges at hand, it is important to give our supply chain problem solvers more tools and resources to find solutions. Certification standards are an important tool, and post-industrial materials are a great resource. Let’s create solutions for the entire system to advance the use of recycled materials.
Laura Thompson, GreenBlue’s Recycled Material Standard program director, can be contacted at [email protected].
The views and opinions expressed are those of the author and do not imply endorsement by Resource Recycling, Inc. If you have a subject you wish to cover in an op-ed, please send a short proposal to [email protected] for consideration.