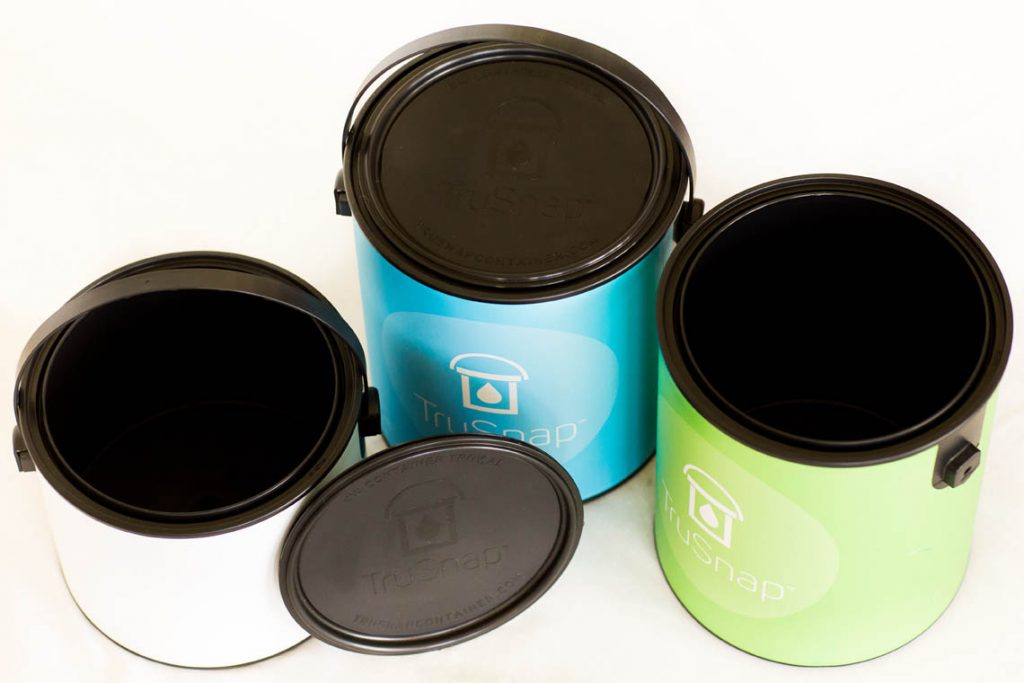
KW’s recycled PP paint can manufacturing operation, KW Container, has experienced increased sales during the pandemic. | Photo courtesy of KW
Supply and demand realities for key curbside plastics are evolving fast during the coronavirus pandemic, and they’ve led one major plastics recycling company to adjust operationally.
During a session of WasteExpo Together Online 2020, a virtual event held last week in lieu of the annual convention, Stephanie Baker of KW Plastics described how the pandemic has boosted the value of certain plastic products, and she explained recent investments her company has made to keep up with the demand.
Public perceptions around plastic have shifted during the pandemic, after a few years of heavy anti-plastics sentiment that sometimes translated into product bans, explained Baker, director of market development for KW Plastics, which is based in Troy, Ala.
“Suddenly, COVID-19 hit and safety and health became an immediate priority overnight,” Baker said. Single-use products found a newfound benefit in preventing the transmission of the new virus.
Supplying the products became the new challenge, and KW quickly began receiving letters from customers who were concerned about sourcing sufficient resin to meet higher demand. Those supply concerns placed greater value on the essential role recycled materials processors play in manufacturing.
“From the very beginning, there was no question whether recycling was considered essential or not,” Baker said.
“I think it shifted the conversation from talking about recycling as part of the waste industry to talking about recycling as part of the manufacturing industry,” she said.
Demand increase drives capacity expansion
KW saw firsthand demand shifts, including through its in-house manufacturing operation, KW Container, which produces paint cans from recycled PP.
“We have never seen demand in the paint and coatings industry like we have,” Baker said. Typically demand spikes in the spring with consumers launching home improvement projects, and demand levels off late in summer as fall approaches.
This year, “the retailers that sell paint are still going very strong,” Baker said. KW has added additional lines and hired more employees to keep up with that PP paint can demand.
KW also saw shifts in HDPE demand, and the overall demand increase across resins led KW to add two new extruders to its production line, Baker said last week.
“If we can get the equipment, which is tight right now, we have plans to add two or three more, because we feel like we are going to see this demand continue to grow for at least the next two or three years,” Baker said. “We want to do everything we can to get ahead of that demand.”
“So we are investing in the middle of the pandemic, as crazy as that sounds, into more production capacity,” she continued.
All of these developments indicate that domestic recycled plastic end markets are “very strong and they are reliable,” Baker said.
She attributed KW’s success during the pandemic in part to its diversity of suppliers and customers, and its critical mass of sourced material.
More stories about Processors
- Major plastic initiative sets sights on system change
- California will fund mixed plastics facility, other projects
- E-plastics processor expands line of recycled board