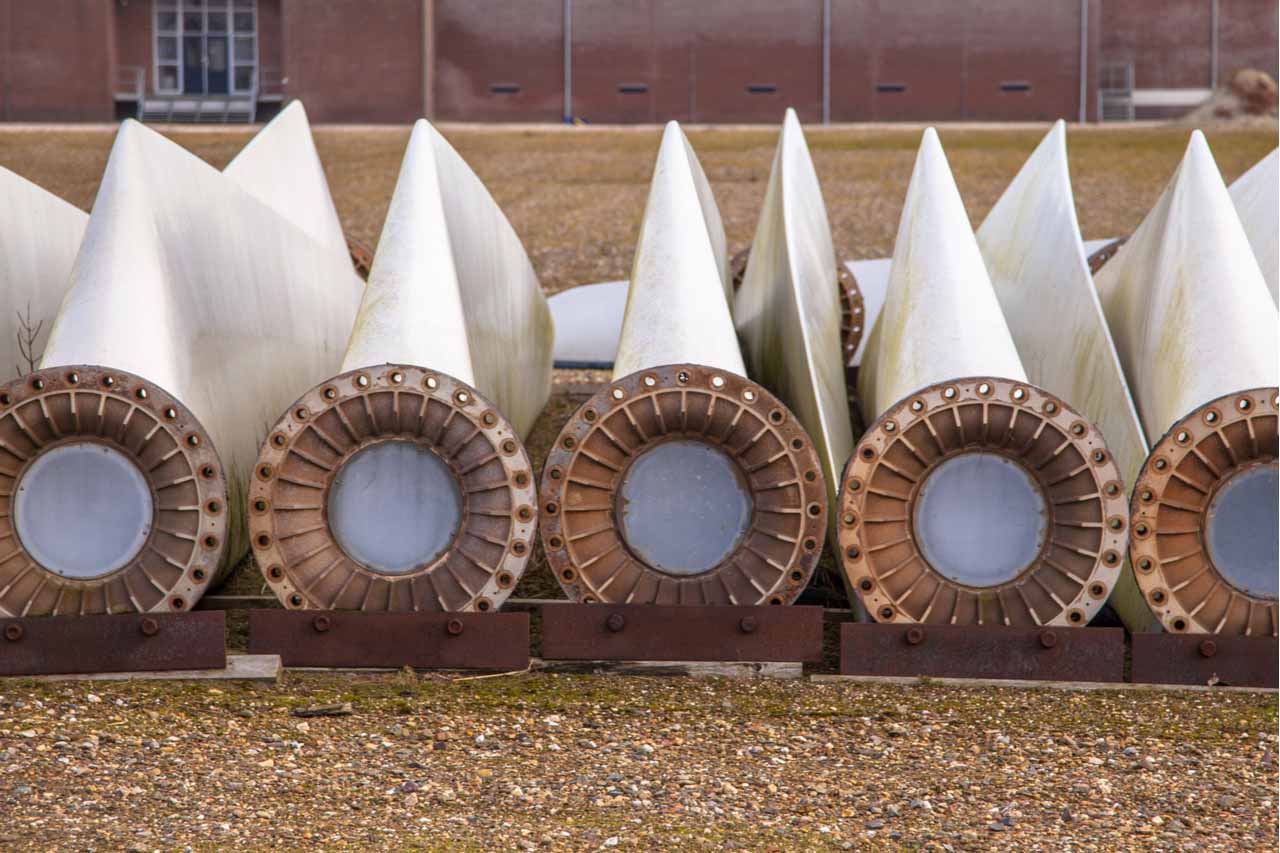
A recent report estimates up to 50,000 tons of blades per year will enter the end-of-life stream in the U.S. by 2023. | Rudmer Zwerver/Shutterstock
Groups representing electricity producers and composites manufacturers released a study exploring landfill diversion options for wind turbine blades.
The “Wind Turbine Blade Recycling: Preliminary Assessment” looked at three end-of-life options: pyrolysis, burning in a cement kiln, and grinding blades so the particles can be used as filler. The study was released by the Electric Power Research Institute (EPRI), which commissioned the American Composite Manufacturers Association (ACMA) to prepare it.
A lot of blades will be coming off-line in the coming years, with few large-scale, commercial recycling outlets available. The report estimates up to 50,000 tons of blades per year will enter the end-of-life stream in the U.S. by 2023.
Wind turbine blades are particularly challenging to recycle. By weight, 80% to 90% of the blade is a fiber-reinforced composite (either glass or carbon fiber), presenting size reduction challenges. And the polymers involved are thermosets, so they can’t be remelted and molded like thermoplastics. Most blades in the U.S. go to landfill disposal.
In terms of recycling the fiber-reinforced composite into new materials, the report looked at processes for mechanically size-reducing the composite and using the resulting chunks, needles or powder as a filler. The study noted the low-value material can be combined with other materials and used in decking, insulation and building panels.
The report laid out the challenges with that process: “The recyclate is mixed material, resulting in up to 40% waste such as paint and contaminants, which require solid waste disposal. Grinding can create a fine dust irritant, and shards create handling challenges. There is a large decrease in the mechanical properties of the recycled material (e.g., stiffness, strength). Moreover, it currently is not cost-effective and requires further investment to process.”
Last year, Plastics Recycling Update reported Global Fiberglass Solutions (GFS) expanded its capacity to recycle wind turbine blades at its Sweetwater, Texas plant. The company grinds the blades and combines the material with virgin or recycled plastics to create reinforced, filled thermoplastic pellets, which can be molded into a number of different products. Karl Englund of GFS was also interviewed by researchers preparing the EPRI report.
The EPRI report provided a high-level estimate of the costs and revenues associated with grinding and reusing the material. It found that grinding the composite to 1-3 centimeters in size costs about $90 to $120 a ton. Further grinding to fibers and powders costs another $100 to $150 a ton. Then, roughly 20% to 40% is waste that needs to go to disposal, with tip fees varying dramatically depending on geography. Finally, the recovered fibers and powders would be worth about $200 to $275 per ton.
“Thus, it is clear from these numbers that commercial profitability would be difficult in the regrind and re-use option, thus requiring user fees or subsidization,” the report concluded. That conclusion was contradicted by Englund, who told researchers the process is cheaper than landfill disposal, making it an attractive option.
Other treatment options
The EPRI report also discussed two end-of-life options in which the polymer is not recovered. It looked at grinding the material into one-inch or two-inch pieces and then subjecting it to a pyrolysis process, using what’s called a Thermolyzer technology from CHZ Technologies. That technology breaks the material down into char, which has recoverable carbon and glass fibers, and syngas, which can be burned for energy.
Additionally, the report explored grinding the material and putting it in a cement kiln, where the glass fibers would become part of the cement and the polymer would be burned, displacing the need for coal or natural gas.
More stories about challenging materials
- Unifi pushes for textile recycling progress
- PET Recycling Coalition doubles down on thermoforms
- RIT researchers develop AI-based textile recycling system