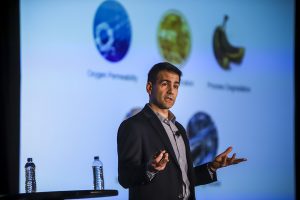
Alan Barcon of PolyOne Corporation.
Processing technology can be used to overcome shortcomings in both PET and mixed plastics, according to two plastics recycling professionals.
During the 2019 Plastics Recycling Conference and Trade Show, experts took to the stage to share various recycled plastic material insights. Alan Barcon of PolyOne Corporation and Alfredo Faubel of Athyron LLC presented during a session titled “Getting Technical Across Materials.”
They talked about optimizing the use of RPET by mitigating the polymer’s shortcomings, as well as creating a desirable product from generally undesirable scrap plastics.
Modifying a standard plastic for desired traits
Barcon, associate director of marketing and technology for additive manufacturer PolyOne, explored strategies for mitigating certain failings of PET without inhibiting its recyclability.
Barcon praised PET as a “fantastic plastic,” but he noted that it “does have some inherent shortcomings,” depending on the use.
For example, oxygen can penetrate the wall of a PET package, he explained. This isn’t a major issue if the PET is used in a water bottle, but if it is holding a dairy product or fruit, it is “definitely a problem,” because those products contain oxidizable nutrients.
Additionally, PET allows light to reach its contents, and it can degrade during the processing phase. Also, using high levels of RPET in manufacturing can be challenging.
Pairing PET with other materials or introducing additives can overcome shortcomings, he said.
“In order to really maximize its potential you really have to pair it up with the right additive depending on what your application is,” he said.
The oxygen permeability issue can be tackled by pairing PET with an oxidizable nylon or other similar polymer, Barcon said. The materials can be paired using a cobalt catalyst. “As the oxygen permeates the container wall, it’s scavenged by that oxidizable polymer,” he said.
To determine which oxidizable polymer is right, the functionality should be considered. A product that needs a 30-day shelf life can get by with using very different materials than something that needs to last for a year or longer. “That has an impact on the amount of oxidizable additive that you’re going to put into the PET,” Barcon said.
Container size and shape also play into these decisions, as will the presence of other additives. Even small amounts of certain colorants “can actually interfere with the oxidation reaction between oxygen and that oxidizable polymer,” Barcon said.
To tackle the light-penetration problem, Barcon again noted that it really depends on the application of the package. If it’s a juice containing vitamin C, for example, the juice can degrade when hit with UV light, and so the plastic should include a light-protection agent.
“You really have to consider, ‘Well, how much light do I need to block?'” Barcon explained. That requires some chemistry and testing.
Barcon’s company, PolyOne, produces several light-blocking options, including an organic-based low-level UV barrier that does not impact recyclability. Last year, it announced an additive for milk-product containers that blocks the damaging effects of UV and visible light. That additive, called Lactra SX, allows “design-friendly, single-layer PET containers to perform on par with multi-layer bottles and laminate paperboard cartons, requiring less material and reducing production waste for increased sustainability,” according to a press release.
Additionally, the Association of Plastic Recyclers (APR) recently recognized PolyOne for its Smartheat RHC additive, which allows for a higher post-consumer resin content in containers and opens opportunities for greater lightweighting.
For stronger light-blocking needs, manufacturers sometimes use pigments in the plastic, Barcon noted during his presentation.
“They are effective, but the issue is then, what do you do with that PET bottle? You don’t want it to go straight into your transparent PET recycle stream, because it will contaminate it, so that’s an issue,” Barcon said.
A more desirable option from a recyclability standpoint is to use clear PET bottles with a full-body sleeve label. Barcon said sleeve technology has improved significantly, allowing them to be more easily removed.
Fiber-reinforced wood replacement
Texas-based Athyron sells a product called Miura Board, which has been manufactured for over 12 years. It’s a durable wood replacement, produced using 100 percent recycled materials.
The product came out of Athyron’s mission to create value from waste, said Faubel, CEO of Athyron.
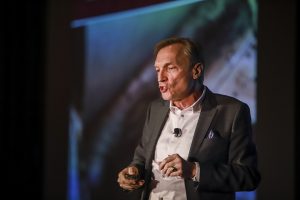
Alfredo Faubel of Athyron.
“Essentially when most people see plastic waste we actually see wasted plastic,” Faubel said.
Miura Board is made from a fiber-reinforced composite. The company takes in commingled plastics and combines them with carpet fibers. Athyron then uses a patented process to blend those thermoplastics with non-melting fibers, which can be drawn from a variety of sources. In February, Plastics Recycling Update wrote about the technology and commercialization efforts.
“The beauty of this technology is that it’s very agnostic in terms of the kinds of feedstocks you can use,” Faubel said during his presentation. That allows the company to use mixed plastics, excepting PVC.
Polymers that melt at higher temperatures, such as nylon or polyester, or glass fiber are added, and the company creates a durable product with “very interesting properties.”
“You can cut it, drill it, nail it, screw it, route it, sand it, but it doesn’t split, it doesn’t crack, it doesn’t swell like wood,” Faubel said.
The material is also paintable or weldable, he said. It can be laminated with wood or other finishes, and it can also be used as a laminate on wood surfaces. It’s also UV-resistant and solvent-resistant, meaning it can be dipped in chlorocarbon solvents, acetone and other substances and it won’t dissolve.
Miura Board is, itself, recyclable at end-of-life. One key feature of the material is that it can be melted, pelletized and used in injection molding. The material can be molded at lower temperatures, Faubel said, which shortens the cooling cycle, allowing greater throughput.
One factor limiting its end market usage is its shifting appearance.
“Whatever comes out today, that’s the color,” Faubel said, noting that this precludes some retailers from carrying the product, as customers demand consistent colors and a wide variety. “It doesn’t mean we cannot pigment it, but then it wouldn’t be 100% recycled. Now, you’re buying an ingredient, basically.”
Photo credit: Brian Adams Photo/Plastics Recycling Conference
To receive the latest news and analysis about plastics recycling technologies, sign up now for our free monthly Plastics Recycling Update: Technology Edition e-newsletter.
More stories about technology
- RIT researchers develop AI-based textile recycling system
- Industry nuance is key in adopting emerging technology
- Google, Dow partner on AI to identify recyclables