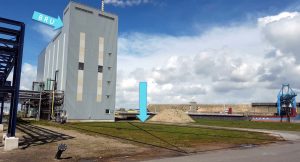
The location of the planned PS foam recycling facility adjacent to an existing bromine recovery unit in Terneuzen, Netherlands.
European groups are backing an initiative to recycle polystyrene materials containing a banned flame retardant. They recently reported key progress in their effort.
The Dutch nonprofit group PolyStyrene Loop is working to build a demonstration plant in the Dutch city of Terneuzen. The group, formed by companies representing the PS foam value chain, was recently awarded a European Union grant of 2.7 million euros (about $3 million), Recycling International reports.
The facility would use a recycling process called CreaSolv, which was developed and advanced by the Fraunhofer Institute for Process Engineering and Packaging IVV (Fraunhofer IVV) and a company called CreaCycle. The CreaSolv process plays a central role in another technology development recently covered by Plastics Recycling Update: Global consumer products brand Unilever is using it as a possible solution for multi-layer flexible packaging recycling.
The technology uses a solvent to selectively dissolve targeted plastics while maintaining the polymer chains. They are then separated from any other plastics, additives or contaminants. A precipitating agent re-forms the targeted plastic so it can be dried and recycled.
The solvent is vaporized so it can be reused in the process. Only small amounts of the solvent – less than 1 percent, by weight – are needed to dissolve the material.
Unilever announced that it plans to build a plant in Indonesia this year to test commercial-scale viability of the approach.
Fraunhofer IVV has also used the CreaSolv technology to tackle e-plastics, separating the polymers from flame retardants so they can be recycled.
Important approval
Formed in January 2016 after a meeting of industry representatives the previous fall, PolyStyrene Loop has been working toward building a plant to apply CreaSolv to expanded polystyrene (EPS) and extruded polystyrene (XPS) building-insulation products. Specifically, the organization wants to apply it to PS insulation containing a brominated flame retardant called hexabromocyclododecane (HBCDD). HBCDD is now restricted in the European Union because it’s listed as a persistent organic pollutant.
HBCDD-containing foams were used for about five decades as insulation in buildings. With a life expectancy of 40 to 60 years, they’re now beginning to enter the end-of-life stream, where they’re currently incinerated.
In May, the Basel Convention’s Conference of Parties approved the CreaSolv process as a valid pre-treatment technique for HBCDD-containing foam. The Basel Convention General Technical Guidelines now also list it as a best available treatment for destroying HBCDDs. The only other best available treatment is incineration, which destroys HBCDD but prevent recovery of the plastic or bromine used in the flame retardant.
“From now on it is no longer mandatory to incinerate all EPS construction waste because it contains approximately 1 percent HBCDD,” according to CreaCycle, which will supply the key solvent.
PolyStyrene Loop noted that the approval was important to helping secure project financing.
“This new framework ensures a global, long-term regulatory stability, an essential condition for the development of the Polystyrene Loop project,” according to the group.
Plant capabilities
The facility, expected to come on-line in 2018, will be financed by a cooperative representing different members of the EPS value chain. It is slated to be built at a manufacturing site owned by ICL-Industrial Products Terneuzen, which produces bromine used in flame retardants.
The CreaSolv process is capable of producing recycled PS suitable for processing into new foams. Fraunhofer IVV had earlier carried out a test using the CreaSolv process on EPS with up to 1.5 percent HBCDD. The process was able to yield PS beads with the flame retardant removed to below 100 parts per million, according to a PolyStyrene Loop press release.
Recycled materials containing more than 100 parts per million of HBCDD can’t be sold, Recycling International reported.
“It was demonstrated that the removal efficiency of HBCDD in the CreaSolv process was higher than 99.7 percent,” according to the release.
Those beads were later converted by a project partner into new thermal insulation panels.
In addition to recovering PS for recycling, the Netherlands plant will be able to recover bromine from the HBCDD. After the polymer is removed, the HBCDD will remain in the solvent. When the solvent is vaporized for re-use in the system, the HBCDD will be left as a sludge in the bottom. The HBCDD will then be sent to an existing hazardous waste incinerator at the ICL-Industrial Products facility. That incinerator is equipped with a unit for recovering the valuable bromine so it can be recycled into new flame retardants.
PolyStyrene Loop noted the CreaSolv process can be used to dissolve PS foams onsite for later processing at the Terneuzen plant. Doing so improves the freight economics.
The longer-term vision is to provide recycling of HBCDD-containing foam across Europe, as volumes entering the end-of-life stream increase.
More stories about technology
- RIT researchers develop AI-based textile recycling system
- Industry nuance is key in adopting emerging technology
- Google, Dow partner on AI to identify recyclables