This story originally appeared in the March 2017 issue of E-Scrap News. Subscribe today for access to all print content.
The choices available in the shredding equipment market are diverse and numerous. Most manufacturers now have a solution for virtually every application. Understanding the types of shredders available is critical when purchasing one of the most expensive machines in a recycling plant. Many manufacturers are willing to facilitate a test as buyers perform their due diligence to ensure they make the best selection for their specific needs.
For most e-scrap plants, shredding is viewed favorably by customers – whether just for destroying hard drives or for handling larger volumes of mixed scrap. Some customers may be willing to pay extra to witness the destruction of their materials and receive a certificate of destruction. For other operations, shredding is primarily a means to recover scrap value, a strategy that can require multiple shredders, depending on the complexity of the downstream separation equipment.
The shredder types highlighted here do not constitute a comprehensive list; they are just the most common ones used in our industry. Likewise, there is not one “correct” way to shred. Selecting a shredder is a very business-specific choice that depends on many factors, and not one choice will fit every operation.
What speed do you need?
There are a multitude of shredders available, but they generally fall into two categories: slow- or high-speed machines. High-speed models cut or fractionate faster due to the higher RPM of their rotors or shafts, and this generally leads to higher heat generated by more friction as well as higher dust generation. They are often the right machines when heavy items need to be broken apart or when particle sizes need to be small.
Slow-speed machines rely on high torque shear cutting and generally run cooler, produce fewer fines and are quieter. Whether slow or fast, the shredder chosen will need to have the right umbilical systems, including provisions for noise, dust, fire and maintenance, depending on what is being shredded.
For the high-speed machines, mills, whether hammer or ring type, are a key element in size reduction. These mills use high speeds to spin rings or hammers that fractionate the scrap on impact until small enough to fall through a sizing grate.
Rings are a suitable choice when better liberation and fewer fines are desired. A ring’s internal diameter will be about 2.5 times larger than the diameter of the ring’s retaining shaft, which allows for deflection and rotation of the ring. In the case of hammers, multiple types are available, including chisel, notched, plain bars and many familiar profiles seen in the scrap industry. The hammers are especially useful in reducing heavy or hard-to-shred items.
The geometry of these mills adds to the shredding mechanism by means of the sweep of the hammers/rings. As the hammer passes the screen or grate, the distance between the two progressively gets closer to encourage more grinding action and further reduction. There are also some variations in mills where the rotors and shafts are vertical. On these machines, the material is ground against bars and textured wear plates as it falls toward the bottom of the mill. Some vertical machines have several stages of size-reduction implements, such as pre-breaker bars followed by rings below. Rather than a sizing screen, an adjustable orifice at the bottom of the mill’s tub controls the volume of the exit and the length of time the material recirculates inside the vessel.
Other types of vertical mills use large chains to fractionate materials when a coarse shred is needed or when large tolerance is required for a very large piece to be introduced. Maintenance and wear can be higher for mills in certain cases, requiring owners to keep removable wear plates and surfaces in stock. These mills can be good candidates for applications involving hard drives, low-grade e-scrap, steel, appliances, motor stators, or a second or third finishing step. Mills are produced by many companies and are extremely diverse in size and configuration, making them easy to adapt to a specific application.
Shearing up
Shear-type shredders are slow-speed, high-torque machines and are the most common shredders in the e-scrap industry. They are also fairly economical to operate.
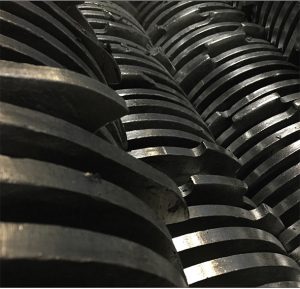
A close-up look at a four-shaft shear shredder that uses half-inch cutters.
The interlocking cutters are disk-like and have hooks integrated into the circumference (see photo to the right). They size-reduce on the principal of shear cutting against cutters on the opposing rotating shaft that have an interference gap between one-hundredth of an inch to three-hundredths of an inch. They are offered in two-, three- or four-shaft models with either electric or hydraulic driven options.
For units with more than two shafts, sizing screens are placed under the shredder cutters to produce a defined particle size.
For two-shaft models, cleaning fingers are used for stripping off the shredded materials from the cutter stack and preventing shaft deflection or damage. The two-shaft shredder models are affordable, but are limited to producing mostly a long strip cut, which is based on the width of the cutters. For those wishing to produce a tighter particle size, material can be conveyed to an external screener – oversized pieces can then be re-fed into the same shredder in circumstances where throughput does not need to be high.
Multi-shaft shredders deliver a defined particle size and reasonable throughput based on the screen opening size. Care must be used when choosing the cutter thickness and screen size since throughput can be reduced by excessive recirculation. Having about a 10 percent larger hole versus cutter width can be a winning approach for shredding e-scrap. Overall, the most common shredder for e-scrap is the four-shaft model, which is a top performing and adaptable platform.
Granulators and reducers
Many operations use a type of shredder called a granulator. There are two main types of granulators on the market, they either accept whole scrap or are designed to be secondary and handle pre-shredded material.
These machines are high-speed and run at 125 to 250 RPM, depending on design. To be efficient, they rely on momentum and use solid, heavy rotors. Multiple blades affixed to the rotor shaft shear against stationary blades or anvils attached to the granulator frame. A sizing screen allows the material to recirculate until small enough to pass.
When working with granulators, maintaining the correct specification on shear gap (distance between rotor blade and stationary blade interface) is a key aspect to enabling proper and efficient cutting. Most machines allow for a blade flip where the cutter can be unbolted and turned over to use an unworn face. Many anvils can be sharpened as they wear, making these machines very serviceable over time.
Some machines have a hydraulic ram and a large hopper that takes on whole scrap and pushes it into the rotor cutters horizontally. A PLC (programmable logic controller) monitors the demand on the drive motor and can modulate how much the ram feeds material into the cutting area.
Other machines are designed for smaller pieces, such as pre-shredded materials, and rely on gravity for feeding into the granulator chamber. Similar to mills, these machines offer high-quality liberation and throughput. They are challenged when dealing with steel and non-ferrous metals and shine when processing batches of plastics, circuit boards and cable. A common granulator application is wire chopping because the systems can produce an ideal particle size for separation of pure copper granulate.
Waste reducers, meanwhile, are slow-speed machines and use their uniquely designed pointed cutters to puncture, tear and rip material against sizing bars or an opposing shaft. The output sizes produced will be coarse and probably will need to be shredded again in a secondary shredding step. Although mostly seen processing municipal waste, these machines have several features which make them interesting to use in e-scrap applications.
For instance, they exhibit a high tolerance to large ferrous parts and cut while in reverse, making them extremely productive. In addition, their use of horsepower can be frugal: A 200 horsepower machine can often process the equivalent to what a 400 horsepower shear shredder can offer. Waste reducers also grab material well and do not require any ram-feeding auxiliary measures. Some models are adjustable and the amount of cutters per shaft or spacing between the cutting bars can be changed in the field, making them adaptable to evolving applications or business conditions.
Most systems produced are hydraulic drive and may even need to be constrained to make sure the downstream shredder is not overwhelmed. For example, a 200 horsepower reducer can nearly shred twice as much as a 600 horsepower four-shaft shredder producing a 2.5-inch particle. A simple algorithm can be programmed into the reducer’s PLC to pause the shafts and time their periodic reversal to essentially modulate the flow and balance downstream requirements.
Using a reducer as a pre-shredder can also allow operators to harvest clean scrap pieces such as plastic, steel or aluminum, and also remove large or heavy parts that could possibly jam the next shredder.
Customize and thrive
All the shredders mentioned thus far have their own ways of customizing based on application, but it’s particularly useful to know how to optimize shear shredders specifically.
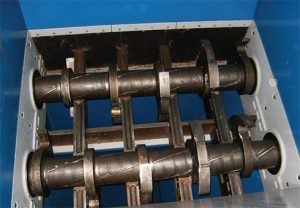
Waste reducers tear and rip material against sizing bars or an opposing shaft.
The cutter is one of the most pivotal factors in shredder performance. The overall radius or diameter of the cutter directly affects the available cutting force since force equals torque divided by distance. Based on this simple physics equation, one can see that reducing distance, in this case the radius of the cutter, improves the amount of force developed. There is of course a limit to how much this trick can work, since the cutter size overall has to be large enough to geometrically grab whatever is being shredded.
It’s also useful to consider how the height of the hook plays a role in cutting ability – force, after all, is also proportional to surface area and pressure. A smaller surface area, as seen in a cutter with a shorter hook, will exhibit more pressure and that will enable better shearing.
Whatever cutter configuration is chosen, the quantities and patterns of cutters placed in the shredder chamber are significant. The total number of hooks engaging together at the same time will all equally draw on the available cutting force, so only having one hook engaging at a time is always going to be the strongest option. For higher throughput, more hooks need to engage at once and spiral or chevron patterns of the cutter hooks are often seen in the offerings from most manufacturers.
The cutter alloy is also a key variable and can influence operational costs due to cutter wear rates. Common cutter materials include D2 tool steel, 4140 heat treated, and hardox variants such as 600. The brittleness of the cutter must be balanced with the difficulty of the materials being shredded to ensure there is no cutter cracking or failure. For e-scrap, hardox 600, hardfaced and heat treated 4140, and similar alloys are common. If it is not possible to make a cutter change and the shredder does have a planetary or similar gearbox, the gear ratio can be changed to adjust the shredder shaft speed, with slower speeds yielding more torque. On occasion, just an internal section of the planetary can be switched out at small expense to make the ratio change.
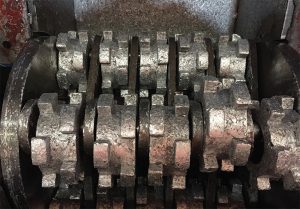
Machines that utilize ring mills use high speeds to efficiently liberate material with few fines.
In the driver’s seat
Another choice to make pertains to drive type. Most shredders feature either a hydraulic or electric drive, and both approaches have a role to play with their applications.
Hydraulic systems are mainly used for heavy-duty processing or situations requiring frequent reversal. Hydraulic-mechanical systems have a compound drive, in which a hydraulic motor turns a planetary gearbox to achieve a desired torque with a lower-cost motor. Some hydraulic pump systems allow the volume the pump displaces to be adjusted to control the speed of the shredder shafts, but others only allow for one fixed speed and are less expensive. Hydraulics are a proven technique, but this setup does require by-the-book maintenance to keep the machines running well to avoid replacement of expensive pumps prematurely.
Electric motor directly driven shredders are popular due to their efficiency and the fact they are simpler to maintain. A dry clutch or belt system is common to reduce gearbox damage caused by hard jams and reversals. The planetary gearbox, however, will require frequent oil changes and monitoring since that is the most likely failure point in these types of drives.
When using an electric drive, external options can allow for more shredder customization, such as a variable frequency drive (VFD). VFDs allow the motor and shredder speed to be decreased and adjusted on the fly by reducing the frequency of the power. They can also be used to speed up shafts, but they do lose motor torque once the motor frequency rises above the standard 60 hertz. Using the shredder’s drive motor amperage, a special controls routine can be developed to run a shredder at speeds above normal motor speed. The machine then slows down once more shredding amperage load is detected, ensuring peak torque is realized only when truly needed. Such a setup can drastically increase throughput for various types of materials.
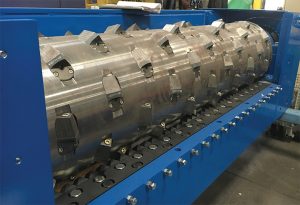
Granulators rely on solid, heavy rotors like the one above.They generally handle pre-shredded material.
The power of choice
Never have so many great options in shredding equipment and customization been available to operators. This allows users to have a system in place to meet the exact needs of a facility.
Key performance choices include selecting the right cutter or hammer materials as well as identifying the optimal configuration, design, screen size and drive system. Using advances in drive systems to dynamically adjust the speed can be a game changer. Selecting a shredder style and platform that can be easily reconfigured and adjusted for changing business needs is a good investment.
Step one in the search for a shredder should always be to arrange a test using your actual materials. And, of course, be sure to speak to several suppliers.
Part one of our series on shredding best practices appeared in the December 2016 edition of E-Scrap News and focused on critical concerns to ensure workers are properly protected when engaged in size-reduction activities.
Rafael Reveles is an engineer and president of Converge Engineering (the recently launched engineering services business of Sims Recycling Solutions). He has 17 years of experience designing and building e-scrap processing systems and can be contacted at [email protected]. Find out more about Converge at convergeengineering.com.