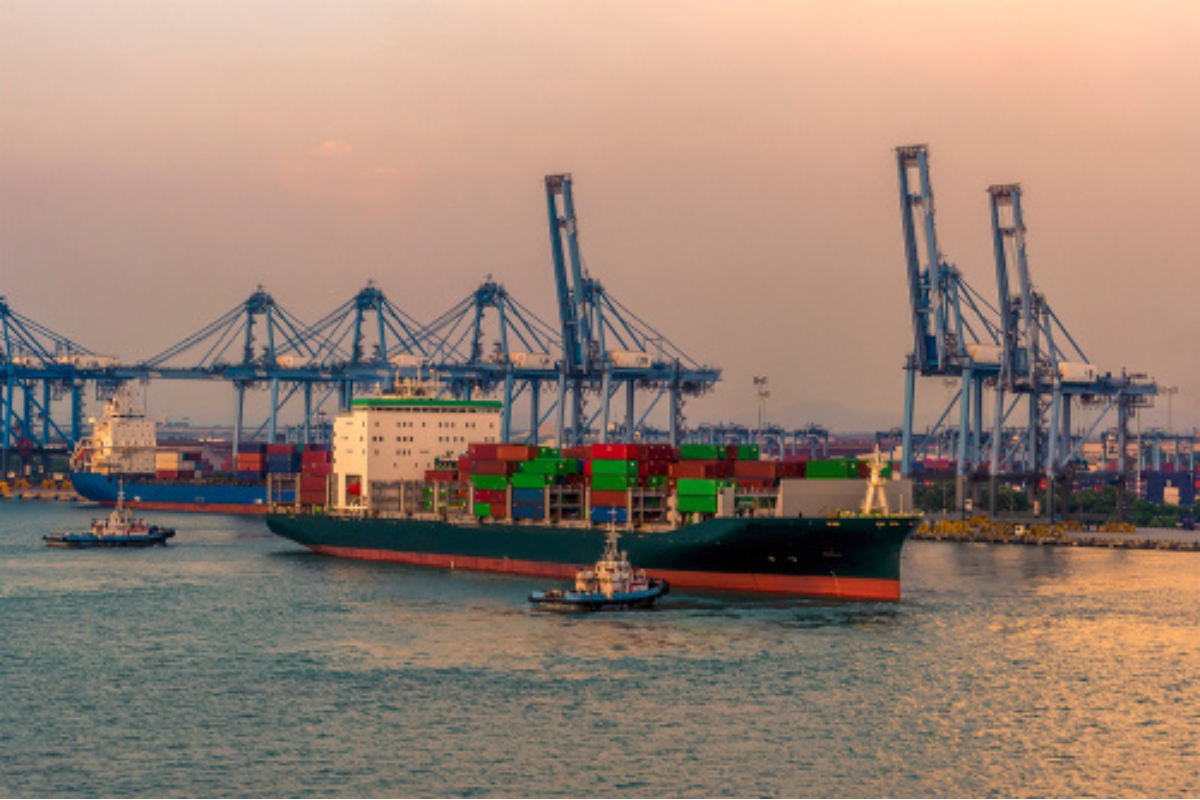
Port Klang, Kuala Lumpur, Malaysia, where U.S. e-scrap companies send a lot of their e-plastics. Several insiders recently shared their thoughts on how the industry will approach e-plastics export violations. | Nicola Pulham/Shutterstock
Chris Kaasmann sees a parallel between the e-scrap industry’s requirement to start managing e-plastics differently and the need for the planet to switch to renewable energy. Both need to happen, but in neither case can you simply flip a switch to realize universal change.
“There has to be a transitional period,” said Kaasmann, a longtime electronics recycling industry stakeholder.
The move by the e-Stewards recycling certification program earlier this month to issue a warning about U.S. exports of e-plastics to Malaysia has kick-started conversations in the industry about the plastics conundrum. On the one hand, the Basel Convention was amended to place restrictions on such exports starting in 2021. On the other hand, there remains too little capacity in North America to clean up and recycle the materials. Meanwhile, stakeholders aren’t keen to see landfilling or burning of the materials, alternative disposition channels that raise costs for e-scrap processors.
E-Scrap News talked with a few stakeholders to get their thoughts on where the industry is likely to go from here, as well as to explain how the e-Stewards electronics recycling standard is making some changes to deal with market realities.
Standard looks to changes
The Basel Action Network (BAN) and its certification standard, e-Stewards, recently put the e-scrap industry on notice that exporting mixed e-plastics – currently a widespread industry practice – is illegal under the Basel Convention. E-Stewards said that if processors continue to send mixed e-plastics to Malaysia, a top overseas destination for the materials, then they are putting their own downstream buyers at legal risk and are endangering their own certifications.
But the certification program is also working to make changes to the standard to ensure e-plastics export violators aren’t necessarily stripped of their e-Stewards certification.
“One way to characterize what we have done is to lower the heat a bit on a screaming kettle while we work to find industry-wide solutions – all the while ensuring that international law remains inviolate,” Jim Puckett, BAN’s executive director, told E-Scrap News.
E-Stewards, a voluntary electronics recycling standard, currently considers mixed polymers from electronics to be a material of concern. As a result of that classification, exporting them could be a critical non-conformity to the e-Stewards standard, particularly if the violation is “done willfully and without extenuating circumstances,” Puckett explained.
But a lot of companies are doing it.
“Based on anecdotal information from the industry, about 70% of the plastic collected by US electronics recyclers is said to be exported to Malaysia,” according to a guide produced by e-Stewards. “This must be viewed as being very close to an estimated non-compliance rate as it is doubtful that these are streams that are cleaned and separated. We fear that we could be witnessing about 125,000 US tons per annum of illegal trade in plastic waste.”
“One way to characterize what we have done is to lower the heat a bit on a screaming kettle while we work to find industry-wide solutions – all the while ensuring that international law remains inviolate,”—Jim Puckett, executive director for Basel Action Network (BAN).
Allowing a majority of e-Stewards-certified facilities to lose certification would usher in serious consequences, both in terms of eroding e-Stewards’ revenue base and overall market competition. And requiring processors to landfill or incinerate materials they otherwise sell to Malaysian companies would hurt the processors financially, as well as endanger contracts with customers who aren’t keen on disposal.
To address the situation, e-Stewards’ Leadership Council in October directed staff to prepare changes to the standard.
“When we discovered the widespread violations we decided to put a hold on the [critical non-conformance] policy for this violation as if the entire industry was signaling extenuating circumstances due to the lack of options,” Puckett said. “We decided to research the situation among e-Stewards and in the entire industry. During that period, we continued to expect the auditors to do their job and flag up minor and major non-conformities on these violations.”
The changes, which are broadly described on page 6 of a guide e-Stewards recently published, include reclassifying mixed plastics as problematic components or materials (PCMs), instead of materials of concern. Puckett said the change brings e-Stewards closer to how the Basel Convention itself addresses the materials.
Under the change, exporting mixed plastics to Malaysia still wouldn’t be allowed, but the practice wouldn’t be as likely to lead to a loss of certification. (Puckett noted that even violating the critical non-conformance policy never entails automatically losing certification, anyway.)
The Leadership Council also signaled approval for changing e-Stewards language to allow PCM exports under certain circumstances. That will open some doors for some certified processors. For example, facilities in Canada could still export plastics to Malaysia if the receiving facility practiced environmentally sound management of the materials and if the processor first received export permission from the Canadian and Malaysian governments (the process of obtaining permission for shipments is called prior informed consent, or PIC, under the Basel Convention).
Emphasizing that the change is not a “get out of jail free card,” Puckett noted that continual major willful non-conformities could still lead to a critical non-conformity. Additionally, certification bodies (CBs), which are the companies with auditors doing the auditing and issuing of certificates, “have their own ways of dealing with such.”
Because the U.S. isn’t a party to the Basel Convention, exports of mixed plastics from the U.S. to Basel-party countries aren’t allowed. If they happen, the companies in the Basel-party countries are at risk of enforcement by authorities.
An exception is if the two countries have a separate bilateral trade agreement in place. Canada and the U.S. currently have such an agreement. Puckett suggested a way forward might be to have Malaysia and the U.S. craft a bilateral agreement. He also said U.S. ratification of the Basel Convention would also open up export options.
“BAN would never ever consider doing less than what is required by international law, but in light of the newly discovered plight of a lack of domestic options and in order to bring the entire industry along and level the playing field, we decided to consider making our standard align with Basel to the letter rather than having it go over and above international law by banning what Basel would in normal circumstances require PIC for,” Puckett said.
Processors talk market realities
Kaasmann, vice president of compliance at electronics recycling and reuse company GreenChip, is a member of the e-Stewards Leadership Council.
He noted that the challenge with e-plastics is “not black and white.” Electronics recycling companies want to comply with international law and e-Stewards requirements, but immediate alternatives aren’t widely available.
Some plastic could be shipped to Europe, but the e-scrap companies there have different business models that are built on them receiving funding through extended producer responsibility laws, he noted.
And landfilling and incineration are problematic options for companies participating in state EPR laws or working for OEMs that have zero waste focuses, said Kaasmann, who also previously worked for Samsung. If processors begin widely disposing of plastics, state programs may not count that weight toward manufacturers’ recycling obligations, resulting in brand owners missing their targets and opening them up to penalties from state regulators.
“It creates challenges with product takeback laws that are predicated on recycling,” he said.
Disposal would also raise costs for processors, some of which work under contracts with electronics manufacturers.
“I have real concerns that manufacturers may not be willing or understand truly why they would potentially see a price increase to landfill, for instance, or to send to Europe or some other solution,” Kaasmann said.
One potential shorter-term solution is having U.S. companies ship e-plastics to Canadian facilities, which then re-export the materials after going through the PIC process, he said. Then there is the possibility of the U.S. ratifying the Basel Convention or signing a bilateral agreement with Malaysia.
In the meantime, everybody is in a bit of a “wait and see” moment, he said.
“We want to do the right thing. As business people, we can’t necessarily do what’s proposed immediately if there’s not a cost-effective solution and a backing from our customers and the manufacturers and alignment within the entire industry,” Kaasmann said.
Jeff Gloyd co-owns consulting firm Gloyd Recycling Solutions with his wife, Lila Gloyd of GreenChip, and has had leadership roles at some major e-scrap recycling companies, including evTerra Recycling and Universal Recycling Technologies (URT).
“I have real concerns that manufacturers may not be willing or understand truly why they would potentially see a price increase to landfill, for instance, or to send to Europe or some other solution,” —Chris Kaasmann, vice president of compliance at electronics recycling and reuse company GreenChip.
In a LinkedIn post responding to e-Stewards’ announcement, he said he’s “positive the industry is not ready for this.”
“No capacity in the domestic plastic recycling network. No ability for existing sorting technologies to meet contamination standards. No ability for processors to absorb the substantial revenue loss and increased fees from landfills and [waste-to-energy],” he wrote. “Either companies will drop the certification or how we classify plastics needs to change.”
In an interview with E-Scrap News, Gloyd said the challenge goes beyond processors installing float-sink systems.
A number of U.S. e-scrap companies have installed such equipment in recent years, including CompuCycle in Houston, Universal Recycling Technologies (URT) at multiple U.S. facilities, eCycle Solutions in Ontario, and others.
Float-sink systems clean up and separate polymers but not to the degree that would enable their legal export to Malaysia.
“You need millions of dollars in extra equipment, and that’s where the capacity doesn’t exist here,” Gloyd said.
There are some companies, including BoMet Polymer Solutions, Synergy Electronics Recycling and Plastic Recycling Inc. (PRI), that further process recovered plastics into recycled resin or products. But, overall, there remains way more U.S. supply than demand for e-plastics.
In the meantime, Gloyd said he’s curious how OEMs, which have environmental, social and governance (ESG) goals, will respond and whether they’ll forbid e-plastics exports or offer some flexibility to their vendors. “Are they going to follow the letter of the rule, or are they going to follow some level of exemption the same way e-Stewards is?” Gloyd asked.
If they cancel contracts with processors that aren’t complying with the export requirements, they may find they don’t have anyone left to contract with, he said.
Kaasmann pointed out the reality that companies can put whatever description they want on a bill of lading, calling a shipment a single polymer, for example, without much policing.
He noted that e-Stewards plans to improve its education of auditors to help them know what to look for, but anybody can be deceived. And if an e-scrap company fools an auditor and gets a certification renewal, that puts at a competitive disadvantage the e-scrap companies that are being transparent and doing the right thing, Kaasmann noted.
“I just think we’re at a really, really difficult place to be at, and I’m not sure the future is that clear for what the immediate solution is for the entire industry,” Kaasmann said.
The state program factor
Then there’s the question of how state EPR programs handle different downstream options for e-plastics.
Jason Linnell, executive director of the National Center for Electronics Recycling (NCER) and an expert on U.S. electronics EPR laws, pointed out that the programs have different levels of information about downstream disposition methods.
“The main question for whether a manufacturer can get credit for material that is sent to a landfill or incinerator is whether the material was ‘recyclable,'” —Sarah Murray, coordinator of the E-Cycle Wisconsin program at the state Department of Natural Resources.
“Most do not have direct access to the recyclers and wouldn’t get reports right away on which downstream markets they are using,” he said. “Some would reference general recycler qualifications in the law, and say it is up to the manufacturer or their programs to make sure their recycler vendors are following the requirements.”
As one example, the latest report from the Washington Materials Management and Financing Authority (WMMFA), which manages Washington state’s EPR law for electronics, notes that two of the recyclers participating in the program remove e-plastics by hand and ship them to Malaysia for recycling. Another, URT, lists both the U.S. and Malaysia as downstreams after e-plastics undergo a more extensive recycling process at URT.
Linnell noted that some state programs are strict about landfill prohibitions, while others view their landfill prohibitions as applying only to whole products, not components/commodities with limited or no recycling markets.
California, for example, for eight years has allowed recyclers to send CRT glass residuals, another material with constrained recycling downstreams, to landfills and still receive recycling payments from the state.
In terms of plastics, Linnell said he knows that some recyclers have formally requested permission from state regulators to landfill the materials in the past.
One program, E-Cycle Wisconsin, currently allows some e-plastics to be landfilled and still count toward manufacturers’ recycling obligations.
Sarah Murray, who works at the state Department of Natural Resources and is coordinator of the E-Cycle Wisconsin program, said state officials a few years ago developed a guidance document on what can be landfilled under the program.
“The main question for whether a manufacturer can get credit for material that is sent to a landfill or incinerator is whether the material was ‘recyclable,'” she wrote in an email to E-Scrap News.
The guidance document lays out the factors DNR considers when it decides what isn’t recyclable. Currently, DNR allows two categories of plastics to be landfilled and OEMs to still claim credit for them: plastics containing flame retardants and other plastics that sink in float-sink sorting systems, and film and LCD layers from flat-panel displays.
“No one has approached us about whether any additional types of plastics should be considered non-recyclable,” she noted.