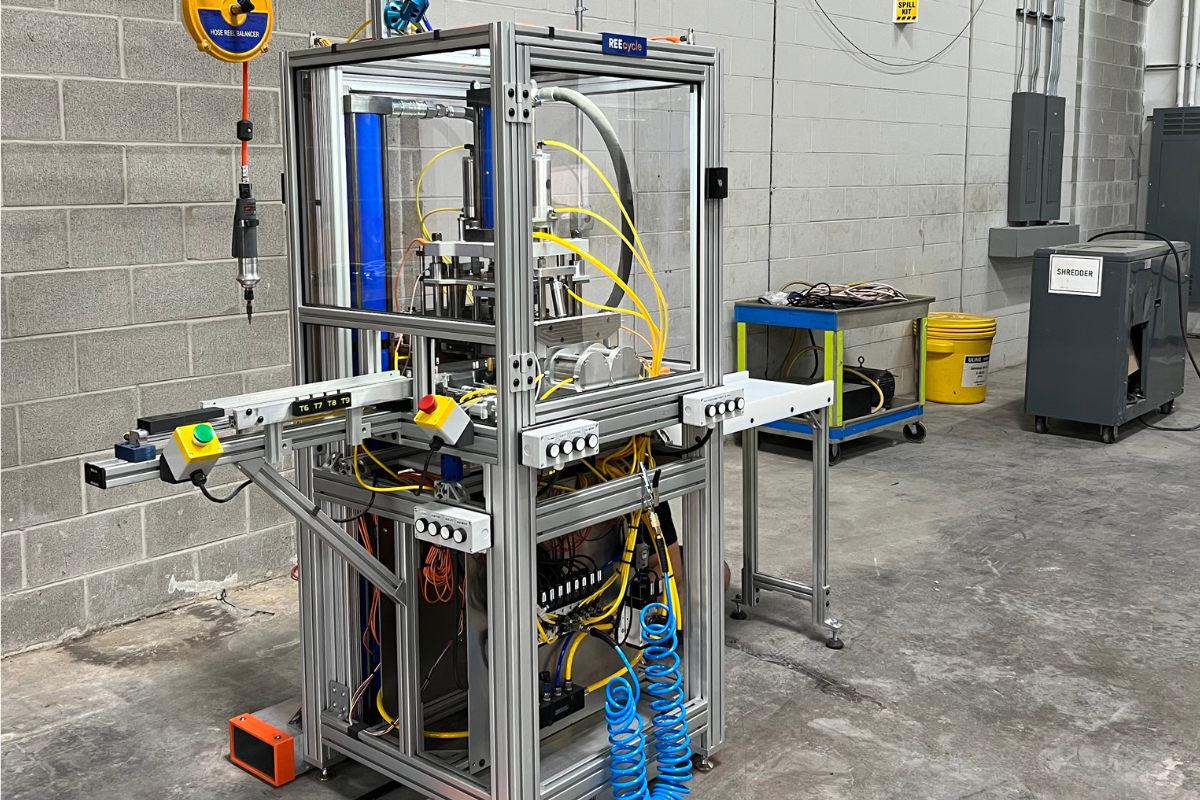
U.S.-based REEcycle includes a skid mounted drive disassembly system in its arsenal of tools for recovery rare earth elements from magnets. | Courtesy of REEcycle
Rare earth element recycler REEcycle received a $5.1 million award from the U.S. Department of Defense to advance its work in extracting elements critical to neodymium-iron-boron magnets — the key building blocks of renewable energy and national defense technologies.
NdFeB magnets are used in numerous defense applications, such as missiles, submarines and unpiloted vehicles, according to a government press release.
REEcycle will use the funds toward restarting its existing demonstration facility and to help commission a commercial-scale plant. The company was founded out of the University of Houston when a group of business students turned a new technology into the foundation of the company, Rasmus Gerdeman, CEO and director of REEcycle, told E-Scrap News. The company uses the patented technology to break down rare-earth magnets, then puts them through its chemical process to extract 99% of the magnets’ valuable materials.
Establishing a domestic supply chain
The ongoing back-and-forth with China on rare earth materials has encouraged U.S. investment in the domestic magnet supply chain.
“A resilient mine-to-magnet supply chain will require diverse sources for rare earth elements,” Laura Taylor-Kale, assistant secretary of defense for Industrial Base Policy, said in a written statement. “REEcycle’s capabilities will help the United States become less dependent on foreign sources by extracting full value from material that would otherwise end up in landfills.”
In December 2023, the Chinese Ministry of Commerce banned exports of rare earth magnet production technology and machinery, and in May 2024, the Biden administration imposed 25% tariffs on imports of permanent magnets from China, to start in 2026. Since 2018, rare earth magnet supply chains have been excluded from such tariffs.
The Trump administration’s plans as to further tariffs are as yet unclear, though the new president has threatened additional 10% tariffs on Chinese exports.
Earlier this month, the U.S. Department of Energy also awarded funds to several companies engaged in rare earth magnet recovery.
U.S. manufacturing of rare earth magnets is growing, according to analysis from Fastmarkets. E-Vac is building a sintered NdFeB rare earth magnet plant in Sumter, South Carolina, about an hour from Columbia, that is scheduled for completion in fall 2025. And rare earth producer MP Materials recently started up commercial production in Texas that includes trial production of automotive-grade sintered NdFeB magnets.
“By enabling REEcycle to recover critical materials from electronic waste, this award will support the DoD’s work to expand the supply of rare earths needed for the production of defense articles,” Anthony Di Stasio, director of the Manufacturing Capability Expansion and Investment Prioritization directorate, said in a written statement. “These awards are an essential tool for mitigating risks in the defense industrial base and reducing overreliance on foreign supplies.”
REEcycle’s process is very efficient in recovering REEs and is cost-competitive and scalable, Gerdeman said. The company estimates that end-of-life HDDs contain more than 1,000 tons per year of recoverable metals.
He compared transporting aluminum UBCs with a large magnet that weighs 2-3 tons, whose content is approximately 30% rare earth elements. Because the magnets are dense with valuable materials, even when factoring in trucking costs for long distances between the supplier and the plant, the recovered elements are cost-competitive with mined elements, he said.
“We don’t see ourselves as a competitor to a mining company. We see ourselves as a necessary complement in the overall supply chain,” he added. “There’s just not enough rare earth to go around outside of China. The big difference with our process is we don’t use 50 tons of dirt to find 1 ton of rare earths. We capitalize on the work already done in mining and avoid the generation of any acidic or radioactive waste. Our only by-product is iron and boron.”
Applying for the funds took just under three years, Gerdeman said.
REEcycle has developed a system to disassemble hard disk drives from electronics recyclers and data centers into their individual pieces, rather than shredding them whole. Not only does this help optimize value for the recovered components, but also it segregates the magnets, significantly improving the recycling efficiencies and yield.
The company could potentially re-process residual concentrates or powders from other chemical processes, to extract any remaining value in the material. He noted that the chemical process has been around for 10-12 years, and its effectiveness has been well-established.
REEcycle is poised to restart its demonstration plant, which was idled as the company fine-tuned its strategy and processing technology, and it will commission a commercial-scale plant later.
The two biggest challenges have been how to scale the operation to an economically viable size, and how to collect the necessary volumes of magnets. The company has partnered with a large scrap collector and has amassed inventory to feed the plant when it restarts.
REEcycle is able to collect and process large magnets, such as those from MRI machines, electric vehicle motors and wind turbines. It can also process smaller magnets from hard drives and automobile speakers that contain NdFeB magnets.
The commercial-scale plant would start with a three-month engineering study, followed by a 12-month process involving obtaining the necessary permits and allowing for equipment lead times, Gerdeman said.
“We are very thankful to have the support of the DoD as we continue our journey, and with all the heightened focus on this problem, we are excited to help solve a portion of it.”