
David C. Bursell of MoviTHERM believes infrared technology is a game changer for protecting the lives of workers and avoiding property damage at recycling facilities. | Piotr Zajda/Shutterstock
Waste and recycling facilities are crucial in handling the world’s growing waste streams, but they pose a significant risk of fires.
Facility operators face many challenges keeping employees, property, and assets safe from fires. For recycling facilities, the increased emphasis on recycling has resulted in an increased 32% average recycling rate, pushing recycling centers to the brink of overload. Couple this with the increase of flammable waste products in the waste stream, like li-Ion batteries, and the need for effective fire detection systems in these facilities has never been more critical.
The EPA reports that 64 waste facilities experienced 245 fires that “were caused by, or likely caused by, lithium metal or lithium-ion batteries.” These fires significantly threaten public safety, the environment and businesses. The causes of these fires vary, but the most common are human error, lack of maintenance and electrical faults, notes a report from AXA Insurance and the Waste Industry Safety and Health (WISH) Forum.
The data highlights the need for effective fire detection systems in these facilities. Infrared cameras have emerged as a game changer in early fire detection, greatly improving safety in waste and recycling facilities.
Challenges in keeping waste and recycling facilities safe
Waste and recycling facilities are prone to fires due to the nature of the materials they handle. Flammable materials, such as paper, plastics and chemicals, are commonly found in these facilities. Additionally, the high temperature required to process and recycle waste can cause equipment to overheat, leading to a fire. Moreover, these facilities usually have large open areas, which can cause the rapid spread of fires, making it difficult to control them when they do happen.
Early detection of fires is critical for preventing significant damage to property, assets and the environment. Fires can quickly spread and cause catastrophic consequences, leading to loss of life and property. Additionally, firefighting in waste and recycling facilities is complicated by the presence of hazardous materials that make it difficult to contain and extinguish fires. Safe evacuation is also critical in waste and recycling facilities to prevent loss of life and injuries.
The impact of infrared cameras in early fire detection
Infrared cameras have become essential to early fire detection in waste and recycling facilities. These cameras work by detecting radiation in the infrared range of the electromagnetic spectrum. This allows them to detect hot spots that could indicate a fire before it is visible to humans. Infrared cameras can also detect temperature changes that indicate a fire is spreading or a piece of equipment is malfunctioning.
By detecting fires before they become visible to the naked eye, waste and recycling facility operators can take action to prevent the spread of the fire before it causes significant damage. Infrared cameras can be mounted to survey large areas and detect in real time hot spots that could be precursors to fires. This enables facility operators to locate hot spots quickly and respond effectively.
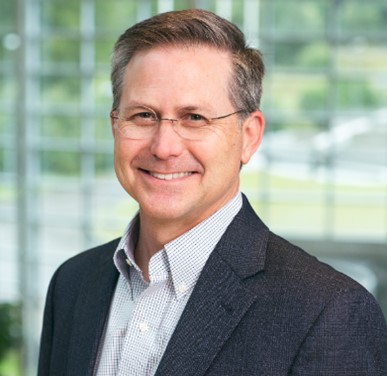
David C. Bursell, moviTHERM
Infrared cameras, unlike human observers, can see through smoke and dust. This is particularly important in waste and recycling facilities, where smoke and dust are common, making it difficult to detect fires using traditional methods. Moreover, infrared cameras can monitor the temperature of equipment, which can help operators identify potential problems before they cause a fire. This proactive approach to maintenance can help prevent fires from occurring, saving money and preventing injuries.
Connecting infrared cameras via the Internet of Things
Connecting infrared cameras and other fire detection sensors via the Internet of Things (IoT) can enhance awareness and keep waste and recycling facilities safe. The IoT allows sensors and devices to communicate with facility operators and each other in real time. This means operators can receive alerts and notifications when a potential problem is detected.
IoT-connected infrared cameras can also provide valuable data that can be used to optimize fire prevention strategies. By analyzing the data from infrared cameras, facility operators can identify potential fire hazards and take steps to prevent them from occurring. This includes identifying areas of the facility that pose a higher risk of fire, such as equipment prone to overheating, and implementing targeted maintenance programs to reduce the risk of fires.
Furthermore, connecting infrared cameras via the IoT can reduce the challenges of firefighting and safe evacuation in waste and recycling facilities. By providing real-time information about the location and severity of a fire, operators can deploy firefighting resources more effectively, reducing the time it takes to contain and extinguish the fire. The IoT can also be used to automate evacuation procedures, providing employees with real-time information and directing them to the safest evacuation routes.
Putting it all together
Waste and recycling facilities face significant challenges keeping employees, property and assets safe from fires. Infrared cameras have emerged as essential tools for early fire detection, enabling facility operators to detect hot spots before they become visible to the naked eye. Connecting infrared cameras and other fire detection sensors via the IoT can enhance awareness and keep waste and recycling facilities safe by providing real-time alerts, informative dashboards and shareable views to aid firefighting and evacuation procedures. Using infrared cameras and the IoT, facility operators can take a proactive approach to fire prevention, reducing the risk of injuries and property damage and ensuring the safe and efficient operation of waste and recycling facilities.
David C. Bursell is vice president of business development at MoviTHERM. For over 23 years, he has been extensively involved with infrared imaging science. He has worked for several imaging companies, including Inframetrics, FLIR Systems and now MoviTHERM. His education includes a B.S. in mechanical engineering from Brigham Young University and an MBA from Boston University. He has also studied digital marketing analytics at the Massachusetts Institute of Technology.
The views and opinions expressed are those of the author and do not imply endorsement by Resource Recycling, Inc. If you have a subject you wish to cover in an op-ed, please send a short proposal to [email protected] for consideration.
A version of this story appeared in Resource Recycling on May 8.