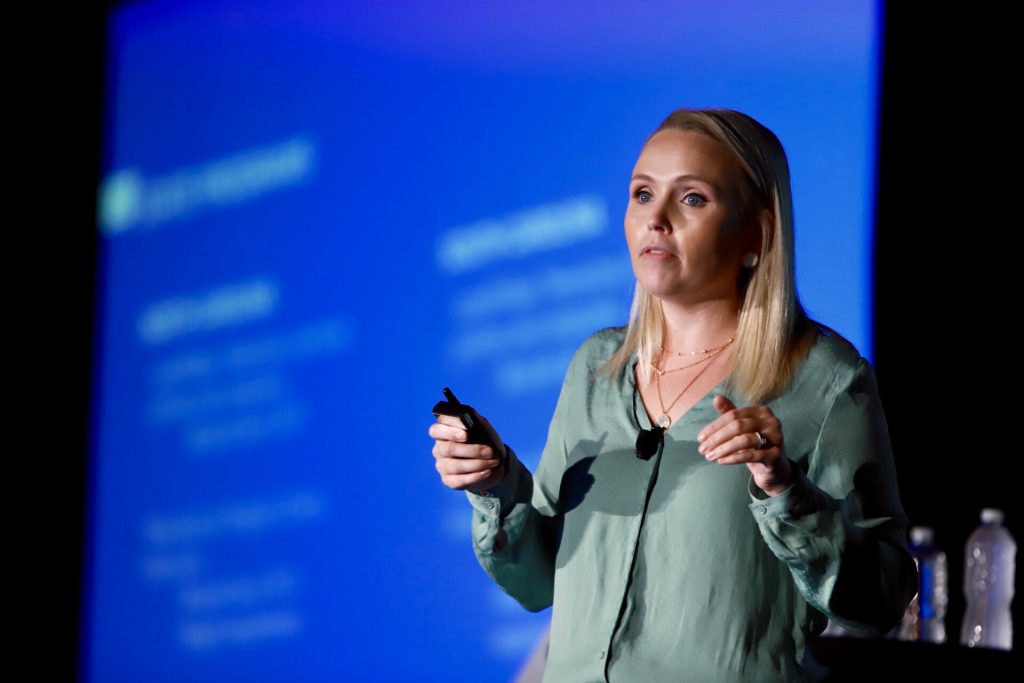
Megan Tabb of Synergy speaks at the 2019 E-Scrap Conference and Trade Show. | Brian Adams Photography
At the E-Scrap Conference and Trade Show last month, Megan Tabb of North Carolina processor Synergy Electronics Recycling offered advice for companies looking to remain afloat in the challenging world of CRT management.
CRT strife is well known in the e-scrap industry, generating headlines about warehouses filled with abandoned TVs, improper disposal leading to prison sentences, lawsuits targeting processors, and more.
While CRTs are on the decline in the end-of-life device stream nationwide, they’re still a major component of what e-scrap companies handle.
“Even though we are slowly seeing this material go out of the waste stream, it still represents a very significant portion of what’s being generated in the Carolinas,” said Tabb, whose company handles CRTs and other types of scrap electronics. She estimates North Carolina will generate a little over 12 million pounds of CRTs over the course of 2019. “While it is decreasing, it’s obviously still a significant problem for us.”
Tabb offered a handful of tips for processors to avoid common pitfalls.
Keep it moving
First and foremost, Tabb said, processors need to focus on moving the material. That means they should process everything that comes in the door. “Just say no to stockpiles,” Tabb said.
A key to regularly moving CRTs is ensuring the processing operation is staffed appropriately, and that means evaluating seasonal trends, Tabb said. E-scrap handlers see peaks during certain times of the year when more consumers are buying electronics. Tabb described spikes in CRT recycling after Black Friday, the Super Bowl, spring cleaning season and more.
“Make sure you staff appropriately so you can handle that when your volume goes up,” she said.
Processors should also seriously evaluate their CRT processing capacity, and when changes come, they should revisit these figures. For example, if a processor wins a big account that will bring in a higher volume of CRTs, the company should consider whether operational changes are needed, such as a second or third shift.
Companies should also work to verify the fact their downstream vendors can handle the volume of CRTs they’re receiving, particularly when changes spur increases in material moving to that vendor.
“In our industry, it’s really hard to say no when somebody wants to send you a load and you know you can make money on it, but sometimes CRT processors have to do this,” she said.
Above and beyond with audits
Although downstream due diligence is a key component of e-scrap certification programs such as e-Stewards and R2, Tabb advised taking even greater measures when it comes to CRT management.
Certified recycling companies already vet their vendors with base-level audits, she explained, but there are more serious audits that examine more than the minimum requirements. That might mean doing an on-site audit of a downstream vendor even when it’s not required by a certification body.
“You might want to make it a rule in your company that you’re going to do an on-site audit of your CRT vendor every year, because sometimes that’s the only way you’re going to know that there’s a capacity issue there, or there’s a processing issue there,” Tabb said. “Just go on-site, go out and visit them – sometimes all you need is just to see the facility for yourself. So make that a requirement for your CRT vendors.”
Companies that lack the resources to perform these audits themselves can consider hiring a consultant to perform these tasks, she added.
And if problems pop up during these audits, Tabb said, companies shouldn’t ignore them, however small they seem.
“Sometimes in some situations we learn that minute thing that raised a red flag for us before actually turned into something huge,” she said. The processor should have the vendor put a corrective action plan in place to fix the problems.
Planning for the unknown
Finally, Tabb advised companies to anticipate problems beyond their control.
“There are so many things affecting your operation that you have no control over,” she said. “So make sure you have a contingency plan for this.”
That can include planning for what to do when the company has lost employees or when the company has to switch downstream vendors, for instance. Despite these challenges, the same amount of material will continue coming in the door.
“Have a secondary vendor in place,” Tabb said.
And, she added, companies should know their vendors’ contingency plans, because vendors have downstream outlets or buyers of their own that are subject to changes.
“They’re going to inevitably have problems, and you want to know what they do,” she said. If a downstream vendor is at capacity, fails an audit, loses an outlet for CRT materials, or any number of other problems, these issues can come back to impact the upstream processor.