This article originally appeared in the March 2018 issue of E-Scrap News. Subscribe today for access to all print content.
Sunlight peeking through a facility’s skylights often reveals a hidden threat in a modern e-scrap plant: airborne fugitive dust. This subtle byproduct of mechanical processing is recognized by our industry as a significant foe in multiple ways.
Dust can negatively impact the health of workers as well as cause fires and explosions in the facility. And it’s now a focus of certifications, regulators and even some customers.
That explains why extensive, well-designed control systems are becoming more of a requirement than an option in today’s operational ecosystem.
Simply put, dust control improperly done can threaten a business in very real ways.
To help operators breathe a little easier on the dust issue, this article will lay out the path to a properly functioning and compliant dust collection system. Establishing a facility where air remains clear certainly takes planning and investment. But the upshot is long-term improvements in productivity and compliance.
Starting at the shredder
Step one in the process of dust management is determining how and where air needs to be circulated so that airborne particles are systematically collected. This involves finding the volume of air needed to cover the plant, which is measured in cubic feet per minute (CFM), and links directly to the size and cost of the dust collector required.
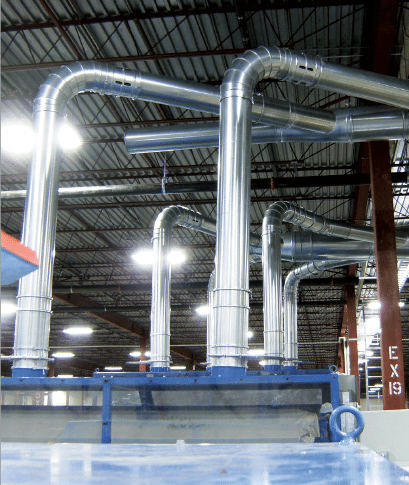
Capture hoods installed on screens can be challenging to arrange, but connecting this segment of the line to the dust collection system is critical.
The top spot for dust generation in an e-scrap processing plant will likely be the shredder, and the volume of air needed to mitigate dust here depends on the shredder type (low or high speed) and the volume of scrap passing through – higher levels of shredding or fragmenting creates increased quantities of fine particles.
Enclosing the shredder with a hood and a flame retardant inlet curtain adds the first layer of containment. However, it’s important to use a hood with proper characteristics to ensure large solids do not enter the ducting that moves collected dust into the larger dust collection system. Placing a deflector or a labyrinth on the pickup ducts above and away from the cutters is a good starting point.
Experience plays a part in sizing CFM for the area near a shredder, but studying the cubic feet volume of the hopper and hood and visualizing how many air changes per hour occur at different airflows helps in the determination. As an example, a moderate four-shaft shear shredder can require 2,000-4,000 CFM to ensure that negative pressure is achieved in the shredding chamber so that dust is contained.
It’s also important to review how material is fed through the curtains into the shredder’s hopper. Perhaps large items are lifting the curtains and allowing dust to escape periodically as the load on the conveyor changes. The answer to this issue can be as simple as enclosing the top of the conveyor several feet before it enters the shredder.
Other critical points on the line
Vibratory and screening equipment rank second in terms of dust generation. These machines disturb and introduce fine particles into the air easily.
Screening, however, also helps in the performance of a dust collection system by removing fines early and provides the most benefit if placed soon after the shredder.
Designing a capture hood for screens can be challenging since pans and screens need ample maintenance access and can be large in surface area. One approach is to hang several hoods adjacently, each with its own extraction ducts. The screener perimeter can then be lined with a curtain, allowing accessibility. Similar to the setup of the shredder hood, it’s crucial to deflect large particles away from the inlet of the duct on screening equipment.
Elsewhere on the line, an operator will want to focus on transitions from one conveyor or sorter to another. Simple covers may sufficiently enclose relatively minor dust generation points. Some plants use an air-jet sensor sorter, which uses large volumes of compressed air to remove circuit boards and metals from the shredder stream. Most equipment manufacturers provide ventilation ports on their sorters for this purpose – the ports connect components to the plant ducting.
Once the whole system has been analyzed, then it will become clear what size collector size is needed. Even after a size has been pinpointed, dust collector costs can increase dramatically due to electrical modifications and the addition of larger ducts and explosion safety devices. An operator will also have the choice of splitting the system into several collectors or running a centralized unit. The layout of the plant plays a role in the choice – space constraints, maintenance access points for other equipment and other factors will need to be considered in the placement of the collector.
Next, an operator will need to consider less obvious factors in the layout of the system.
For example, maintaining a minimum airflow velocity in the ducting system is critical to ensure dust does not settle and create blockages. A typical velocity in this case could be above 4,000 feet per minute to ensure the dust does not drop. Consider adding access ports in the ducting every 15 to 20 feet or as prescribed by your engineer. Once the ducting is installed, fine adjustment is done with blast gates and bleed-in valves at each hood. Bleed-in valves allow a small amount of clean air to enter the duct to reduce hood airflow while not affecting the duct velocity.
One last layout decision is required: whether the dust collector will go outside or indoors.
If placed outside and the clean air is also discharged outdoors, the volume of air the dust collector removes from the facility will need to be made up by means of make-up air blowers or vent openings in the building. In cold climates, a heater may be needed for these extra blowers, which can be expensive. Outdoor collectors also need a robust system of material containment to ensure no pollution occurs.
Filters, ducts and other infrastructure components
A number of critical pieces of hardware will also be necessary to make sure the dust mitigation network runs smoothly.
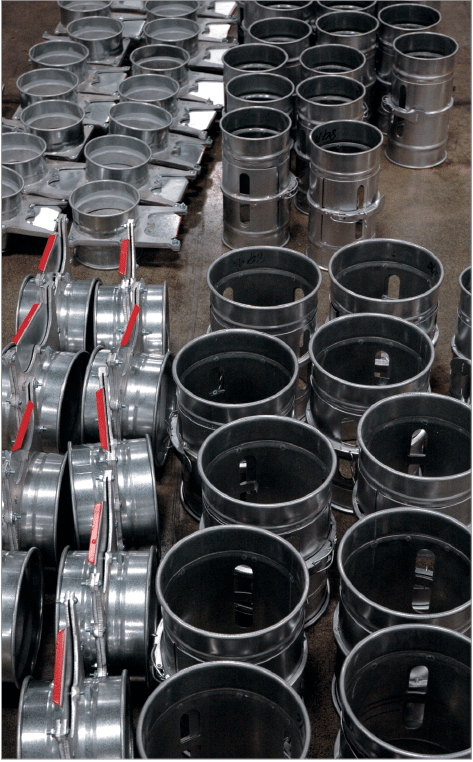
An operator will have many choices when it comes to designing the ducting system. A civil engineer may need to be consulted if ducting will be hung from the ceiling.
Once dust moves into the collection system, filtration becomes a key component. There are several styles of filters, including cartridge and bag types. Cartridges tend to be easier to replace than bags and are more efficient, thus requiring fewer filters and much less total baghouse physical size. Either type should be ordered with a spark-resistant package – this arrangement includes carbon-laced filters to absorb static charge, aluminum fan wheels and internal grounding. Purge air will be required to clean the filters, and this can come via existing plant air or a new compressor system. To maintain high filtration performance, some e-scrap facilities use secondary high-efficiency particulate air (HEPA) filters and bag breach sensors that are interlocked into the plant controls.
When it comes to ducting decisions, an operator will have many choices, including the classic spiral type and the quick-connect style (this latter option costs more upfront but is easier to install, thus reducing contractor costs). Many quick-connect ducts are self-bonding and do not require a ground jumper wire to be installed on every connection as is the case with spiral types. If the ducting is going to be hung, a civil engineer may need to come in to evaluate the strength of the roof, especially if a snow load may be present. Also, special trapeze mounts may be needed for the ducting to distribute the weight across multiple roof joists.
Other necessary components for the system will be geared specifically toward fire prevention. The process of ventilating shredders presents a risk of spark creation and small fires because paper, toner and flammables may accidently enter the stream. An infrared spark detector can be fitted to the ducting prior to the collector and initiate a downstream water spray inside the duct to knock down a spark and also shut off the equipment.
Also, many collectors can be sourced with sprinkler heads pre-installed that can be connected to the building’s overhead sprinkler system. Such an approach is a good practice and will require a permit. Use caution to make sure the sprinkler heads do not foul with debris. Special thin cellophane bags can be added by the sprinkler company to keep the sprinkler heads in good condition.
Focus on fire
As mentioned just above, facility fires are a major issue when it comes to dust management.
Dust dispersed in the air can become combustible, even if the particles come from a material such as aluminum that itself will not necessarily ignite easily. Since the shredding process producing the dusts can also generate sparks and occasional small fires, the risk of combustibility on this part of the line is heightened. And the problem can quickly elevate in stature. The fast burn rate during a dust-related blaze produces heat, flames and hot gases that cascade through the dust cloud and generate rising air pressure, similar to what might be generated by a bomb. The worst-case scenario is a secondary explosion – this can occur when an initial event disturbs all settled dust in the facility. The result can be a devastating blast that literally blows the walls out.
Combustible dust also presents a regulatory risk since a citation can be issued if a facility is deemed to be operating unsafely by OSHA or other authorities and not adequately addressing explosion risks with approved safety equipment and housekeeping procedures. The National Fire Protection Association (NFPA) develops standards that most regulators and cities adopt, and these standards lay out the required equipment and procedures.
First and foremost, an operator should be regularly testing dust characteristics per the correct American Society of Testing and Materials (ASTM) test procedures at an accredited lab. If the dust tests positive for combustibility, then explosion safety measures and protocols will need to be retrofitted or incorporated into the design of the new dust collection system – this can cost nearly as much as the dust collector.
There are both active and passive types of explosion protection devices. Some technologies use canons with inert powders to stop an explosion from developing and spreading. Another strategy is to use vents and valves to isolate the dust collector and safely vent out the pressure that could cause an explosion if left unmanaged. Passive systems are prevalent in e-scrap installations and cost less in annual maintenance, but a facility’s design engineer should make the ultimate determination.
Since many dust collectors are located indoors, a special flameless explosion vent (or vents) will be needed to keep flames and particulate from exiting during an event – these systems work by quenching the heat and dust with a wool-like stainless steel. In addition, no-return flap valves will shut and latch if the airflow reverses in the ducting (as would be the case with an explosion), and this keeps flames from spreading and starting a secondary explosion.
Since the risk of combustible dust explosions is so serious, NFPA specifies a dust hazard assessment (DHA) be done by a qualified party to check the overall system and evaluate whether plant risks are controlled. The DHA report must be kept on file for regulators and will provide a road map for best practices on maintaining the system.
Basic housekeeping and facility cleaning is also important. Accumulations of dust within a plant can be dangerous and fuel the secondary dust explosions capable of demolishing a whole factory. In general, these visible accumulations of dust are prevented by cyclical cleaning plans that should include roof joists, the top of machinery and production areas. Use care that any vacuums used for cleaning are explosion proof.
Wrapping it up
Dust control can be an expensive but necessary addition to a shred line to protect the health and safety of the employees and community. Properly designing the system upfront saves resources in the long term, improves the professional image shown to clients and regulators, and reduces risk of business interruptions later on.
When weighing the investment, consider the higher cost of retrofitting later or extra cleanup and housekeeping that can be reduced by a well-designed system upfront. Operating a clean plant is good practice and appreciated by those who work on and around it.
Rafael Reveles is an engineer and president of Converge Engineering. He has 18 years of experience designing and building e-scrap and metals processing systems and can be contacted at [email protected]. Converge Engineering (convergeengineering.com) provides dust collection systems and e-scrap shredding and materials-recovery equipment to recyclers.