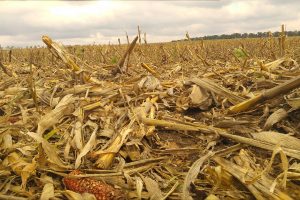
A byproduct from corn harvesting is a key component in a new method of e-scrap leaching.
Researchers on two continents have recently made breakthroughs on the use of leaching techniques to recover critical materials from e-scrap.
American research
Scientists conducting research for the U.S. Department of Energy’s Critical Materials Institute (CMI) developed a method of using bacteria to produce acids to dissolve and separate rare earth elements from shredded electronics.
The method, which is more environmentally friendly than traditional chemical methods used in the mining and recycling industries, uses a strain of Gluconobacter bacteria. The microbe consumes sugars and produces acids.
“They thrive in sugar-rich environment. They like simple sugars that are easy to eat, easy to break down, just like we like Twinkies and donuts,” said David Reed, the principal investigator heading up the research. “But refined glucose accounts for 44 percent of the expense of this recovery method, so we started looking for lower-cost alternatives.”
One such glucose alternative identified by researchers is found in the residue left after corn harvesting – it’s a mixture of stalks, leaves and cobs called corn stover. This agricultural byproduct is relatively easy to convert to usable sugars and cost competitive for larger-scale commercialization, according to a press release from Ames Laboratory.
The Ames Tribune has more details on the research.
Finnish research
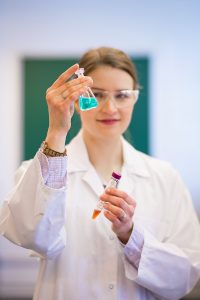
Studies for the recovery of valuable elements, such as gold and copper, are currently underway from waste electrical and electronic equipment.
Researchers at a university in Finland are scaling up their technology to recover a number of critical raw materials, including precious metals and rare earth elements, from shredded e-scrap.
A team at the University of Jyväskylä has been working to find ways to better recover critical metals. They’ve developed a hydrometallurgical process in which thermally treated material is leached in stages to separate the metals. Copper is recovered via electrowinning. Other metals are separated “using a novel liquid-liquid extraction and state-of-the-art metal scavengers,” according to a press release.
“We are producing gold, silver, palladium, copper and platinum with very high recovery rates and purities, and rare earth metals as oxides,” Ari Väisänen, the project leader, stated in the release.
Now, the work is moving from the lab into a research-and-development demonstration facility. The primary goal is to ensure the process can be scaled up to industrial levels and to produce a fully functional metals recovery unit for commercialization.
Top photo credit: Ivaylo Velikov/Shutterstock
Bottom photo courtesy of University of Jyväskylä
More stories about research
- Texas A&M researches rare earth extraction
- Report: Battery ‘retirement tide’ nears
- Right-to-repair scorecard shows improvements for cell phones