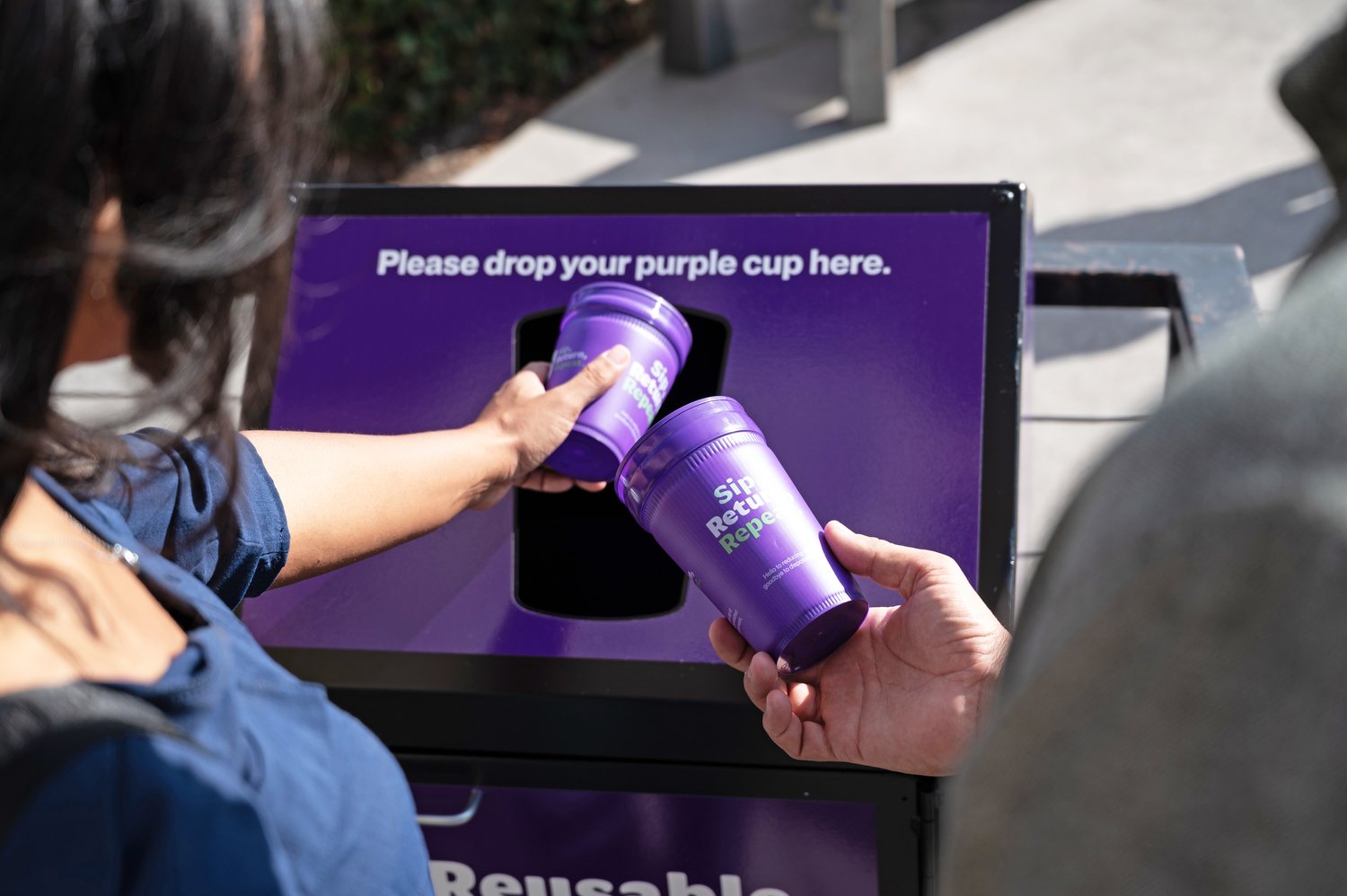
Organizations across the U.S. have been working to grow reuse programs to the scale of cities and beyond. | Courtesy of Petaluma Reusable Cup Project
This article appeared in the April 2025 issue of Resource Recycling. Subscribe today for access to all print content.
Systems for collecting, sanitizing and redistributing foodservice items are ready to scale up with the help of curbside collection, certain policy changes and other factors, panelists said at the Resource Recycling Conference late last year.
“The next chapter of reuse needs to be tested at city-scale to create an immersive and convenient experience, so that it can be widely adopted,” said Andy Rose, head of circular systems modeling at Perpetual, a nonprofit that works with communities to design and implement reuse systems.
Such a program could feature a common set of reusable items that’s disbursed through a variety of businesses, checked out like a library book or with a deposit, then finally collected back through bins around town, he said.
Rose and other program leaders described progress from coast to coast, including a reusable foodware program at Grand Canyon National Park, a plastic cup reuse pilot in Petaluma, California, and a glass container study in Durham, North Carolina.
Macy Zander, local reuse manager for another national nonprofit called Upstream, pointed to the significant share of resources — almost half of new glass and plastic, for example — that goes into hundreds of billions of single-use items every year in this country.
“Though recycling is clearly a very critical piece of the solution to effective waste management, we believe that there needs to be a shift in focus upstream to cut waste before it is even put out into the world,” she said. “The majority of these items are used by consumers for mere minutes or sometimes seconds before they get discarded.”
She added: “There’s a brighter side to this, though, and that is reuse.”
In many ways, the push offers a return to tradition while also cultivating local economic development and benefiting public health, the panelists said. And the field is wide open for someone to take the lead.
“Some people would argue with me, but I would say there is really no example of a reuse system deployed at scale globally, with the possible exception of beverage reuse in Germany,” said Elizabeth Balkan, director of Reloop North America, which takes American officials on tours of European systems that, as with recycling, often outshine those in the U.S.
“We gotta get to work, right? Because we’re behind,” Balkan said. “And there’s a lot of great lessons learned that we can also capture, so that we don’t have to reinvent the wheel.”
‘We need everybody’s help’
A program much like the one Rose described played out over three months last fall in Petaluma, a medium-sized town about an hour north of San Francisco.
The regional government agency Zero Waste Sonoma partnered with Closed Loop Partners’ NextGen Consortium, a brand-supported initiative to address single-use foodservice packaging, to create an open-loop cup reuse system, meaning it wasn’t restricted to one business or event.
Instead, 30 restaurants, including chains and mom-and-pops, shared a purple polypropylene cup that residents could drop off at more than 60 matching purple bins around town. It went further, with a paid public awareness campaign, the participation of a local MRF to pick up misplaced cups and an Uber Eats-style pickup service — “all the bells and whistles,” Zero Waste Sonoma Director Leslie Lukacs said.
“This is the first of its kind in our nation to do an equitable program because there is no deposit; everybody is just getting the reusable cup, and that’s it,” she said.
In the end, roughly 220,000 cups, or more than half, were returned, enough to provide environmental benefits compared to single-use cups, according to the final Closed Loop report released in February. On top of that, at least 80% of local residents knew about the program, understood how to participate and wanted it to continue.
“This data is not just going to help our community, it’s going to help everybody in the reuse space,” Lukacs said. “It’s been a highlight of my career to have this happen in my own backyard.”
The city of Seattle has taken a similarly wide-ranging approach to its own reuse program, said McKenna Morrigan, strategic adviser for Seattle Public Utilities. The Reuse Seattle initiative aims to support a reuse ecosystem by contracting for dishwashing and other services, recruiting participating businesses and paying for pilot projects and public communications.
“We know that we are not going to be able to make the progress that we want to see around reuse on our own, you know, as a city. We need everybody’s help to make progress,” Morrigan said. “We really see our role as creating the conditions for reuse solutions to flourish.”
The effort has partly come down to policy, she noted. Before 2022, Washington’s food code only allowed bring-your-own-cup programs for coffee shops and the like under certain conditions, involving paperwork and separate approvals.
“That’s a hard no” for busy small business owners, Morrigan said. “It’s pretty simple, but it turns out that’s actually a policy impediment in most states in the country to this day.”
An unsurprising ingredient in the reuse formula is the money, Morrigan added. The state and local economic development department provided some funding for Seattle’s work, and the city was on the hunt for more.
“A few weeks ago I was feeling pretty excited about where the EPA was going with their SWIFR dollars,” Morrigan said at the November conference, referring to the general election a few days prior and to the federal Solid Waste Infrastructure for Recycling grant program. “I don’t, unfortunately, think that the federal government is going to be a source of significant funding for any of our work in the near term the way we hoped it might be.”
Her words proved prophetic, as the Trump administration immediately halted billions of dollars of federal spending, including for SWIFR grants, to ensure they all aligned with the president’s priorities. The money had been approved by Congress, and federal law and U.S. Supreme Court precedent previously prevented such an appropriation hold-up. Several courts have since ordered the resumption of much of the funding, but some EPA grant recipients have told Resource Recycling the money is still locked or uncertain in recent weeks.
Zero Waste Sonoma applied for SWIFR’s second round in the fall to continue and expand the cup reuse program, Lukacs said in March. She had little hope of receiving it.
“I’m not quite sure if the SWIFR grant still exists,” she said, adding all of the cups and bins are in storage for the time being. “We’re just kind of pausing until maybe spring to see what happens.”
Whatever funding mechanisms are available, Lukacs reiterated her view that reuse programs must be a shared expense. Local or federal government funding is “part of the solution, but it’s not the full solution,” she told conference attendees.
‘Renormalizing reuse’
Petaluma and Seattle’s examples illustrate the need for broad, systemic, infrastructural changes to allow reuse to reach its full potential, said Crystal Dreisbach, Upstream’s CEO. She pointed to polystyrene containers and trays, which have raised health concerns over contact with hot food and can be replaced with reusable alternatives yet are common in restaurants and schools. Why do we still use those?
“The answer is not because people are dumb or that’s all there is,” she said. “Really we haven’t created a system yet to make anything else possible.”
Interoperable, shareable infrastructure is essential — “It’s washing dishes, it’s transporting dishes, it’s storing dishes,” as Dreisbach put it. Businesses have been reusing pallets, crates and other back-of-house equipment for decades, she added, “and that type of reuse saves corporations an incredible amount of money.”
Upstream, Perpetual, Reloop, a fourth nonprofit called PR3 and many other groups are united in the quest to bring the same norms to customer-facing wares, Dreisbach said.
In her previous work in Durham, North Carolina, for instance, she worked with a network of partners, including a local MRF, to test out curbside collection and reuse for glass containers, the kinds used by distilleries, salsa makers and any number of other local businesses.
“They said the cost of the glass to put their stuff in was more costly to them than making the actual product,” Dreisbach said. And MRFs could benefit from joining reuse programs as well, with revenue streams that aren’t dependent on volatile commodity prices: “They can do what they do best — collect, transport, sort, redistribute — in a whole different way.”
More recently, Upstream last year received a grant from the National Park Foundation to lead a 2.5-year reuse program in Grand Canyon National Park that might be replicated in other national parks. And the Chicago Bears launched a reusable cup program at its stadium in November, which could provide an anchor venue that makes washing infrastructure accessible to schools, hospitals and other establishments, Dreisbach said. Moves like these bring reuse closer to becoming an everyday utility, much as it was decades and centuries ago.
“We’re renormalizing reuse, aren’t we?” she said, adding she prefers the word recirculation. “It creates a visual concept.”