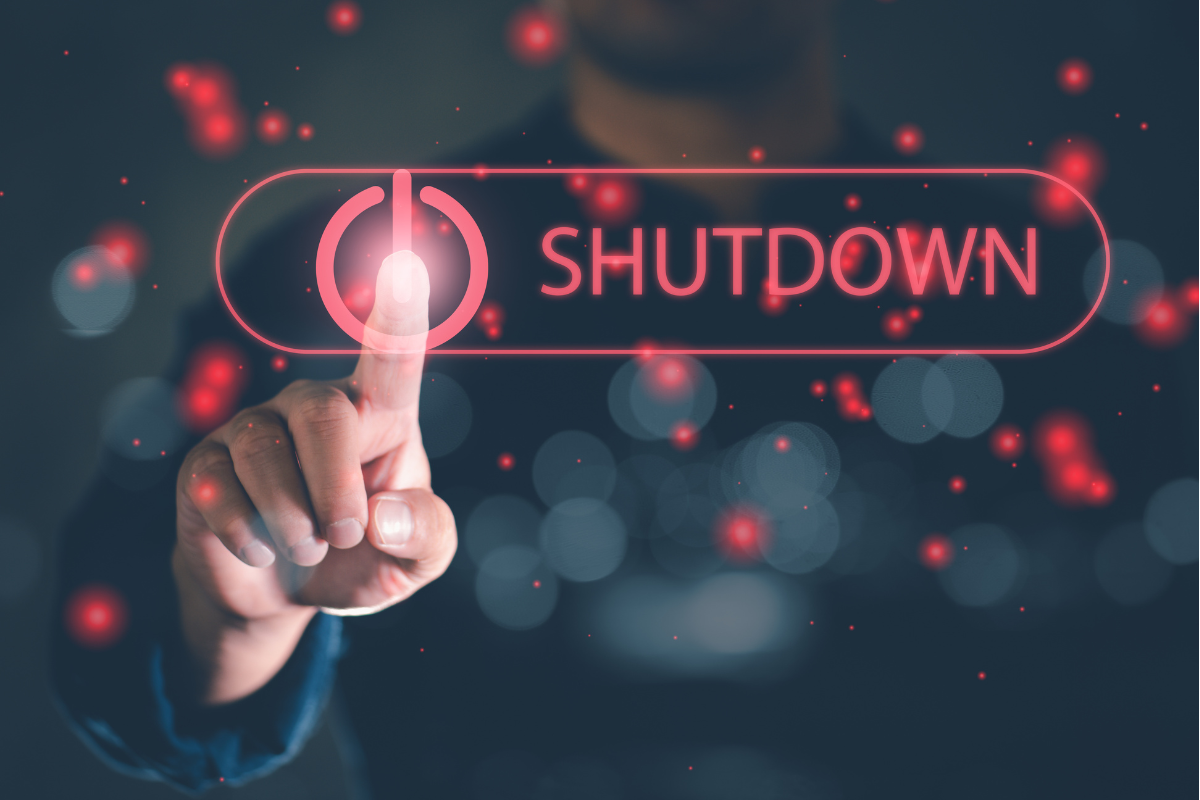
LookerStudio/Shutterstock
Facility closures by Smurfit Westrock drew substantial reader interest last month, alongside stories covering state extended producer responsibility policies and a glass collection pilot project in California.
LookerStudio/Shutterstock
Facility closures by Smurfit Westrock drew substantial reader interest last month, alongside stories covering state extended producer responsibility policies and a glass collection pilot project in California.
A judge favored Brightmark’s parent company over a slightly higher bid, preferring Brightmark’s plan to keep the facility operating over the competing bid’s liquidation plan. | Photo courtesy of Brightmark
Brightmark’s bankrupt Indiana pyrolysis facility has been sold to parent company Brightmark for $14.3 million in a move that will keep the facility operating and retain most or all of its more than 100 employees, a judge ruled this month. The latest development came after a competitive auction process with plenty of twists and turns.
Continue Reading
In March, California Gov. Gavin Newsom rejected SB 54 draft regulations, forcing the rulemaking process to restart. | Brandon Bourdages/Shutterstock
The first public opportunity to comment on California’s latest extended producer responsibility for packaging draft regulations stretched past the allotted time frame, with some speakers saying changes to a chemical recycling regulation section were unlawful. Continue Reading
The report touches on five main topics: recyclability of covered materials, compostability of covered materials, reuse and refill and other source reduction systems, cost coverage for local jurisdictions, and plastic leakage into the environment. | Ratchat/Shutterstock
Members of the California extended producer responsibility for packaging advisory board have identified dozens of barriers to implementation and offered up possible solutions in a recent report.
Sue Beets-Atkinson, global vice president of sustainability at SBM Management Services.
A warm welcome back to “Women in Circularity,” where we shine a light on women moving us toward a circular economy. This month, I was pleased to connect with a leader in zero waste facilities: Sue Beets-Atkinson. Sue is the global vice president of sustainability at SBM Management Services. SBM is a leading global services provider that helps corporations meet their operations-related sustainability goals. Sue has 32 years of experience in business waste minimization. Continue Reading
Containerboard and paper facilities in Georgia and Texas are set to close this year. | Worradirek/Shutterstock
Two major manufacturers of recycled paper products are closing locations in Georgia and Texas, the companies announced earlier this month, though it’s uncertain whether the facilities in question are using recycled fiber. Continue Reading
An April 30 Defense memo echoes recent congressional efforts to allow the military to repair its own equipment, which helps reduce costs. | Bumble Dee/Shutterstock
As part of a broader initiative to increase efficiency, the U.S. secretary of defense has called for the Army to include the right to repair products in its procurement contracts, adding support to previous congressional efforts. Continue Reading
A technology-focused panel at ReMA’s 2025 conference featured Blake Gordon of Georgia-Pacific Recycling, Lisa Kagan of Buddy and Geoff Aardsma of AMCS, and was moderated by Jennifer Betts of Magnar Metals. | Photo by Colin Staub / Resource Recycling
For Blake Gordon, general manager of digital trading at Georgia-Pacific Recycling, defining next-generation technology can be boiled down to a simple question: Does it simplify something that is unnecessarily complex? If so, it’s next-gen. Continue Reading
A MRF in Windham, Connecticut, received upgrades to be more efficient and sustainable. | Courtesy of Casella
Casella Waste Services has reopened its Willimantic MRF in Windham, Connecticut, after renovations to increase capacity and provide more energy-efficient recycling processing. Continue Reading
Residents were already “wishcycling” the cups, so the locally owned recycler decided to pave the way to formal acceptance. | Oasishifi/Shutterstock
The city of Omaha recently added paper take-out cups to its list of accepted items for recycling, with locally owned First Star Recycling leading the way in the resident-driven effort. Continue Reading