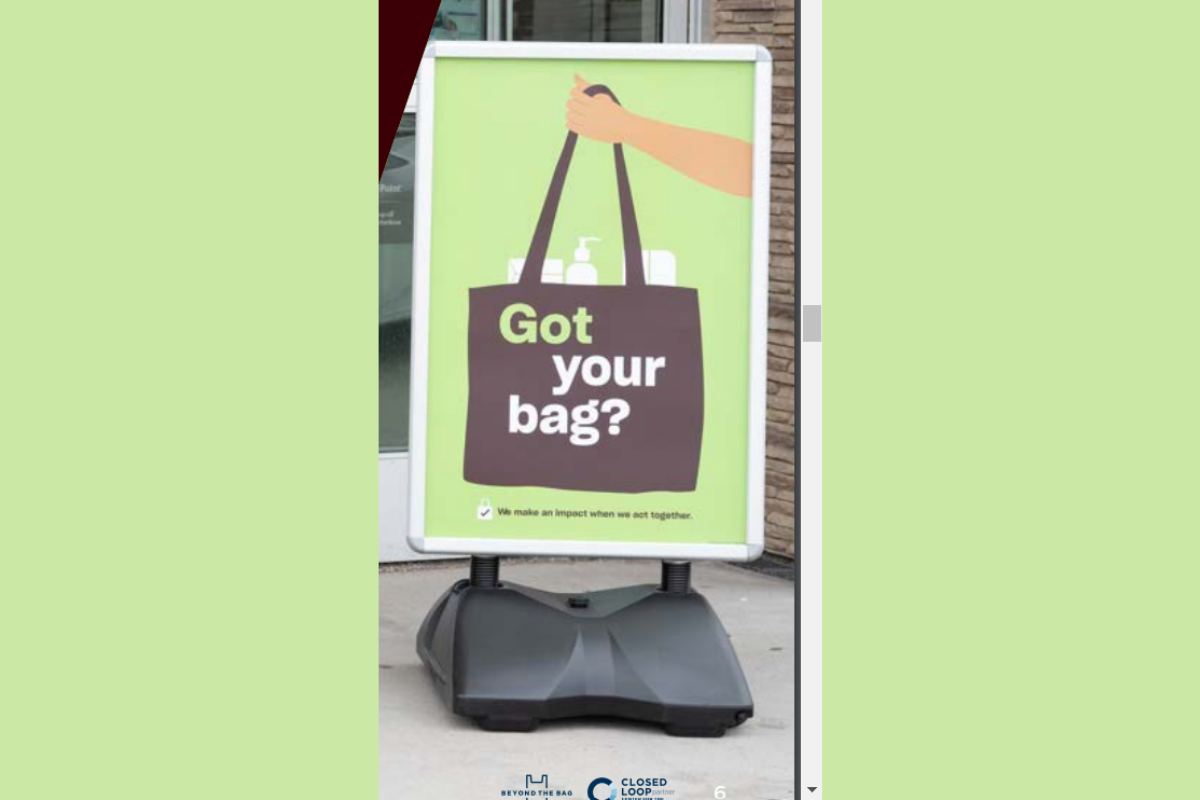
The industry-led Consortium to Reinvent the Retail Bag conducted a three-month pilot project that implemented store signage, enlisted employees to help effect behavior change and included out-of-store marketing. | Photo by Nick Pizzolato
When retail stores encouraged consumers to bring their own bags or opt out of using one, nearly 5% fewer single-use plastic bags were used, according to a report from the industry-led Consortium to Reinvent the Retail Bag. Continue Reading