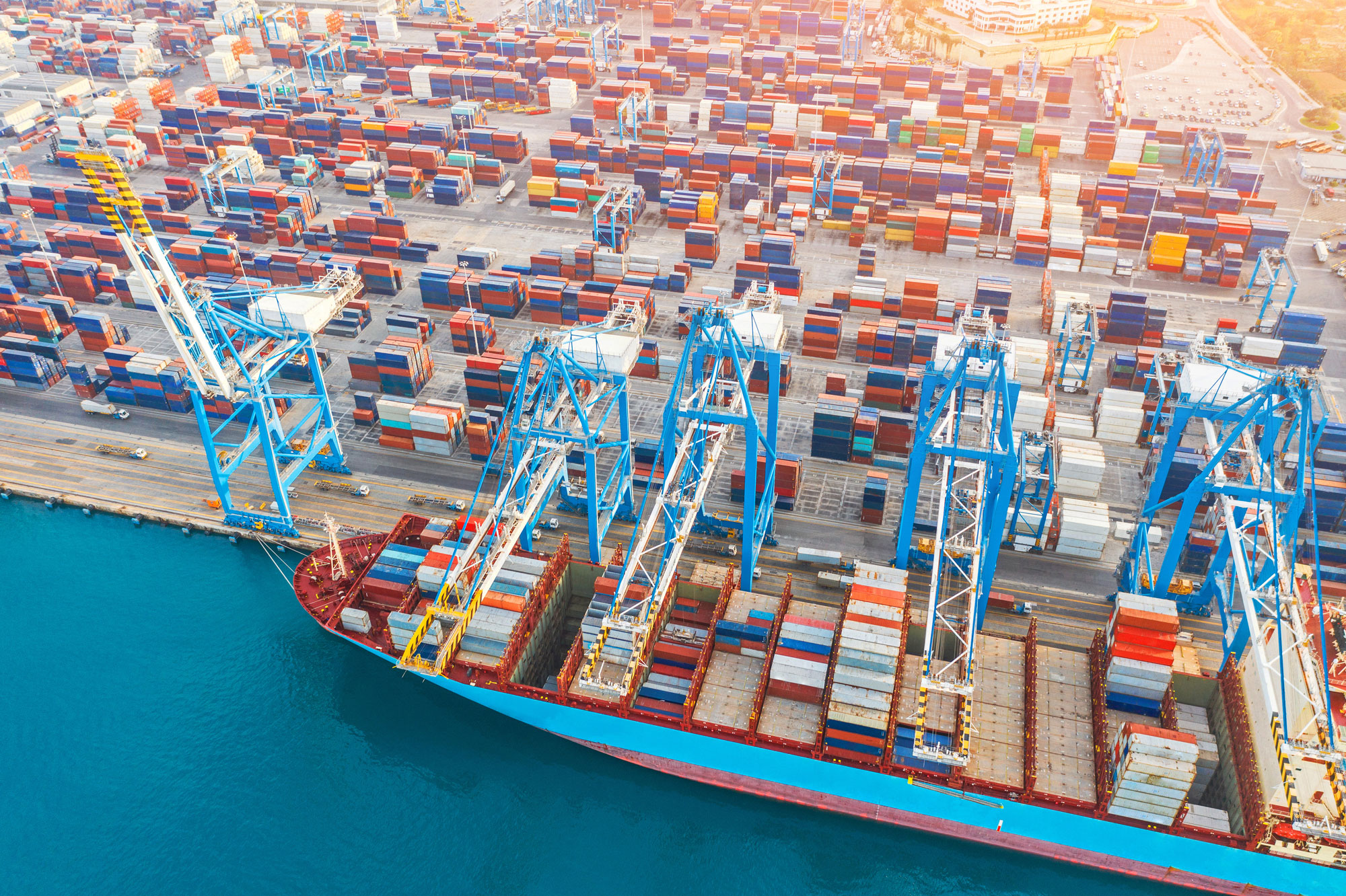
On tariffs and federal spending, the recycling industry confronts uncertainty and adjusts plans across the U.S. | aapsky/Shutterstock
This article appeared in the May 2025 issue of Resource Recycling. Subscribe today for access to all print content.
After many weeks of shifting narratives and uncertainty, participants in recycled commodity markets are working to navigate a new tariff environment, in which buyers and sellers as well as customs officials struggle to align federal mandates with on-the-ground implementation.
On April 2, President Donald Trump enacted steep tariffs on goods from most other countries, citing inequities in trade relationships. Although Trump has maintained his commitment to tariffs since his inauguration on Jan. 20, throughout February, March and April he threatened, delayed, imposed, suspended and delayed again various measures — in the process removing any semblance of calm from commodity buyers and sellers alike.
Country-specific tariff rates ranging from 11% to 50% were temporarily paused in early April after multiple days of significant stock and bond market turmoil. But plenty of import duties remained in effect as of press time, including a 10% baseline tariff for most countries, a separate 25% levy on aluminum and steel imports and far steeper tariffs on trade between the U.S. and China.
“The big problem right now is there’s not complete clarity,” said James Derrico, vice president of new business at commodity brokerage Cellmark, in an early April interview. For example, for RPET resin making its way to the U.S. from areas that include Southeast Asia and Canada, the back-and-forth tariff dialogue can significantly and unpredictably increase costs.
“We crossed the border with material that had been scheduled that day to cross (before tariff implementation), and then we got billed for it,” he said, adding that the tariff applied to the RPET resin was incorrect when compared to what the administration had previously indicated. “So we don’t even know. We’re like, well, you want the wrong rate. And two, is this real?”
The lack of clarity also is forcing market players to interpret the regulations to the best of their ability. For example, Cellmark believes its commodities are covered under the U.S.-Mexico-Canada Agreement. The Recycled Materials Association has stated that recycled material imports into the U.S. from Canada and Mexico qualify for the USMCA tariff exemption, provided they were collected in North America and that the importer goes through a process of certifying the material’s origin.
Pulp and paper products traded between the U.S. and Canada and Mexico have been exempt, said Ryan Fox, corrugated market analyst at Bloomberg Intelligence. A federal list of exemptions also seems to support this interpretation. However, the cardboard boxes made from the raw materials were subject to tariffs, and demand for the finished product is the driving force, he said.
Raw materials coming from outside North America are also subject to a 20% tariff, and European mills are balking at paying an extra $200 or $300 per ton and want someone else to pay it, Fox said.
Cellmark’s Derrico agreed, saying neither buyers nor sellers are keen to pay more, and it’s unclear who should be paying the added costs. With the previous round of tariffs in 2018-2019, “we got a pretty big slap on paper crossing” between the U.S. and Asia, he said. As a result, all of Cellmark’s supply contracts include clauses to account for tariffs, he said, though the majority of the company’s business is done on a spot basis.
Capacity shuffling?
One upside is that the tariffs could cause producers to leverage domestic production capacity, according to Rabobank’s most recent containerboard quarterly report.
“In the short term, it may lead to producers reshuffling their supply chain to keep fiber within the country borders,” wrote Xinnan Li, senior analyst of packaging and logistics at Rabobank. An example of the implications of shuffling production is evident in the automotive sector. GM recently announced it would temporarily shift some truck production from its Canadian and Mexican plants to one in Fort Wayne, Indiana.
But the full implications of such a shuffle are complex, especially on a local level. For example, the idling of Stellantis plants across the U.S. border as a result of tariffs will also result in temporary layoffs for about 900 U.S. workers making parts that are shipped to the Canadian and Mexican assembly plants, according to the Detroit Free Press.
In addition, shifting production can complicate an accurate assessment of demand, Fox said. Bloomberg’s projections showed box shipments in the first quarter will be lower by 1.5% on the year, he said.
“It’s kind of one thing to talk about what the tariffs could do on paper, but it’s really more of what tariffs are doing to the box buyers, because they’re seeing demand for their product disappear,” Fox said.
For instance, tariffs on American liquor will result in a decrease in shipments outside the U.S., subsequently lowering demand for the boxes the liquor is shipped in.
Bloomberg’s most recent industry survey showed that expectations for corrugated box demand have turned more bearish for demand in April, compared to the beginning of the year. Responses were “relatively positive” at the end of January, but by the end of March “it was much more negative,” with respondents citing on-again, off-again tariffs and customers waiting to purchase.
“I think the most important thing to remember at this point is that some of this stuff is literally changing on a daily basis,” Fox said. “We don’t know if it’s going to or how long it’s going to stick around.”
Comparisons to previous disruptions
Despite weeks of leadup, the administration’s waffling made implementation seem sudden, as the market could not be sure the tariffs were more than threats or “negotiating tools.” In 2019, the first Trump administration gave a 30-day notice for its tariff measures against China. That gave buyers and sellers time to determine how they wanted to proceed, Derrico said.
“It’s a little bit different (now), and it’s kind of scary in that as of today, it’s still not clear if things are exempt or not, and what tariff rate is applied to each shipping lane.” As a result, Cellmark is waiting to ship new loads until the company gains clarity, he said.
In a recent blog post for Canada’s Paper and Paperboard Packaging Environmental Council, Executive Director Rachel Kagan also compared the current developments to previous market disruptions. “We have seen before how external policy decisions can have impacts on local markets,” she wrote, citing China’s 2018 National Sword policy that restricted imports of materials considered to be waste.
But China’s policy presented an upside, as evidenced in a Q&A PPEC conducted with Paulina Leung, chief sustainability officer at member company Emterra: “It opened up new markets in new countries and highlighted the need to ‘onshore’ recycling in Canada and in North America,” and “the need for recyclers to have a diversified customer base can never be underestimated.”
In addition to adding another layer of complexity to brand owners’ progress on incorporating recycled materials, even a threat of tariffs creates uncertainty that stymies short- and long-term planning, which “could impact or even delay progress or investments in corporate waste reduction and sustainability initiatives,” Kagan wrote, echoing the complaints of market players who declined to comment publicly, due to the constantly shifting market conditions and fear of retribution.
Uncertainty hits recycling projects
Dramatic federal funding cuts have affected at least two plastics recycling efforts, contributing to a major project being canceled in Pennsylvania and forcing an accelerated timeline for self-sufficiency at an Alaska composite lumber operation.
In Pennsylvania, International Recycling Group canceled plans for its Erie plastics recovery plant, according to a recent press release.
The company said a freeze of unspecified duration on federal funding commitments was among the financial challenges that contributed to the cancellation. The U.S. Department of Energy’s Loan Programs Office had guaranteed IRG up to $182.6 million in loans last summer, more than half of the $300 million required for the project.
Other financing challenges included tariffs on materials and equipment made outside the U.S., which increased anticipated costs “substantially,” according to the release. The company also cited difficulty in securing offtake agreements for recycled plastics from manufacturers and brand owners, “many of whom are cutting back on sustainability pledges.”
“I am personally devastated after 18 years of working to bring this vision to a reality that we have failed to overcome these challenges,” said Mitch Hecht, IRG founder and CEO.
The Erie Regional Chamber and Growth Partnership “is frustrated by the financial pressure building due to economic uncertainty at the federal level, which IRG cited as the reason to cancel plans for its Erie plastics recycling plant project,” said CEO Brandon Mendoza in a written statement. “We recognize the significant economic opportunities it could have brought to Erie. This project had significant support at the state and local level, across public and private sectors, and to see it pulled is a significant loss.”
The plant would have converted 160,000 tons per year of post-consumer plastics into about 100,000 tons per year of recycled resin, and would have produced about 20,000 tons a year of CleanRed feedstock for steelmaking furnaces.
IRG also discontinued its newBin collection service in Erie, and the company will remove any remaining collected material and attempt to find a buyer.
Alaska Plastic Recovery had likewise been receiving funding from the U.S. EPA for collecting recyclable plastics to use in its Grizzly Wood composite lumber. But under the Trump administration, such funding is uncertain.
“We were using grant income to subsidize our collection efforts, and that funding is no longer available,” said CEO Patrick Simpson in an interview.
In a recent letter to customers, Simpson said, “Due to recent changes in federal funding, we now need to accelerate our timeline and achieve breakeven within the next 9 months,” instead of the originally planned 18 months. The company also is raising prices for its lumber, and sales of Grizzly Wood also will need to double in 2025 to meet sustainability goals.
Residents also will be asked to pay $5 per visit to the community collection center to reach the financial breakeven point, Simpson said. The company partners with the city of Anchorage for recycling collection.
“We are transitioning more quickly from a subsidized or partially subsidized business to a completely sustainable business as a result of this,” Simpson said. “I don’t think any of that is necessarily bad. I think we’re a small business, and we need to learn to adapt. Things are going to happen, whether it’s in the political climate or something in the environment.
“Instead of a gentle glide path to full sustainability, it’ll be a little bit more of an abrupt climb, but we’ll get there,” he added.
Despite the funding loss, the company could benefit from the new administration’s emphasis on oil and gas exploration, which is key to Alaska’s economic health. Simpson’s company collects and recycles plastic thread protectors for the metal fittings used in such projects as a proposed 800-mile trans-Alaska pipeline to move natural gas from the state’s North Slope to its southern ports for export, likely to Asia.
As for what’s ahead, “no one has a crystal ball that good,” Simpson said. “But for today and for right now, we’re going to figure it out. We think that’s a good plan, and I think we’re going to get through this.”