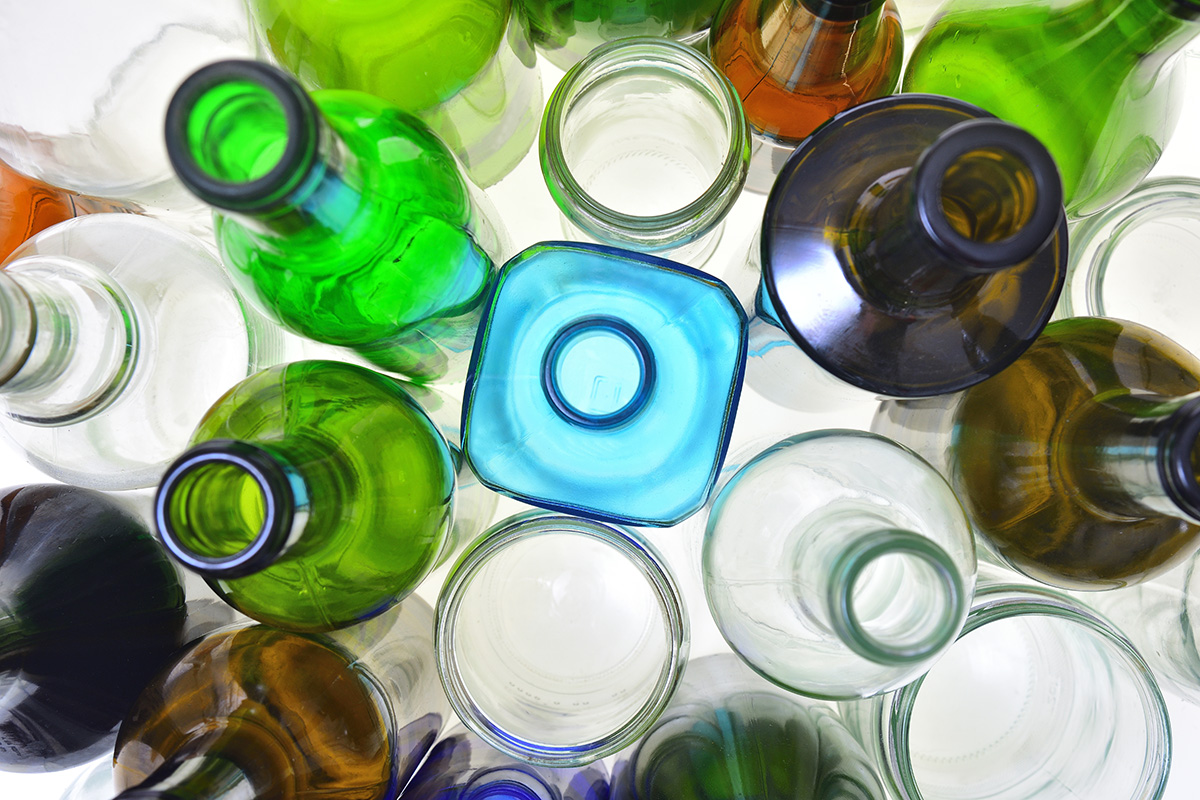
To hit its recycling goals, by 2030 the recycling industry will need to double the amount of glass it recovers nationally compared with where it was in around 2020. | Josep Curto/Shutterstock
Although glass has its share of unique challenges in the recycling system, brand owners in the glass space are facing all-too-familiar hurdles in figuring out how they’ll hit 2030 recycling and recycled content goals.
This was a key topic at a glass-focused session of the Packaging Recycling Summit, held in September in Anaheim, California.
Over the past 20 years, the glass recycling sector has captured about one third of the glass placed on the market each year for recycling into new containers, Scott DeFife of the Glass Packaging Institute told attendees. In 2019, producers set a goal to increase the glass recycling rate to 50% by 2030. DeFife noted that goal was set before the pandemic, and that there have been “a few bumps” in the road, but “we’re still making some progress on incremental tons.”
To hit that goal, by 2030 the recycling industry will need to double the amount of glass it recovers nationally compared with where it was in around 2020, he said.
“There is plenty of glass in the United States to fill that need for the glass container market and for the other end markets,” DeFife said.
The oft-debated question is how to collect that material, and how to ensure it is of high enough quality to use in new container production.
How different collection streams stack up on glass quality
According to the U.S. EPA, the recycling rate for glass was 31.3% in 2018, the most recent year for the agency’s Facts and Figures data. Laura Hennemann, senior vice president of sustainability and corporate affairs at Strategic Materials, noted that “most have said that number is dated and it’s closer to 25-27%, so there is a lot of room for improvement.”
Strategic operates 43 glass processing facilities throughout North America, most of which are in the U.S. It recovers 2.4 million tons of material – primarily glass – per year across North America, making it a huge player in the glass space: Overall, the U.S. recycled 3.1 million tons of glass in 2018, according to the EPA.
The non-glass portion Strategic processes is made up of contaminants included in the MRF glass, such as metals, plastic, fiber and more. Strategic attempts to find markets for that material as well.
Hennemann described the various collection options that are used across the U.S., and she laid out the volume and resulting quality associated with each.
Deposit stream glass is high-volume, very clean material and 98% of the material that comes through this stream can be used in producing new containers. More than half of the cullet the glass container industry can use comes from the 10 states with bottle deposits, DeFife added, because of the material’s desirable quality.
Not only does deposit provide the cleanest stream, but it also means simply more glass gets recovered, even if it is just shifting the glass from curbside to redemption centers. In California, for instance, volumes spiked after lawmakers recently expanded the state’s deposit system to include wine and liquor bottles, even though those bottles were largely accepted in curbside systems.
“Bottle bill cleaner streams give us higher yield and more material back than the material that comes through the curbside commingled,” DeFife said.
Hennemann said curbside programs with a glass-on-the-side collection system produce similarly high-quality material – about 92% of it is suitable for container production – but it produces less volume, because there simply aren’t many of these programs anymore. They’re expensive to run, and programs have largely shifted to single-stream, with glass commingled alongside other materials in one bin, Hennemann said.
In community drop-off programs with glass bins, about 60% of the glass is suitable to be processed into new containers, she said.
Finally, there’s single-stream, which Hennemann noted the glass sector has a “love-hate relationship” with. The quality is lower, but it’s tied to convenience, she said, adding that in North America, “convenience is king.”
“That’s where we really see moving the needle the most, is working on how can we divert more volumes from single-stream into the recycling stream and away from landfill,” Hennemann said.
Unique among curbside materials
DeFife laid out the different position glass holds in the single-stream system than materials like paper, plastic and aluminum: “The way that the material is sorted at the facility is just completely different,” he said.
Paper, plastic and aluminum are typically segregated through a positive sort in a single-stream MRF, where optical sorters target those materials specifically. But glass is recovered through a negative sort: The material is broken and collected through a series of screens along with other fractional materials, rather than being specifically targeted and isolated. For processors like Strategic, it means dealing with more contamination than in loads coming from deposit programs.
The lower quality of glass in the MRF system isn’t just a problem for the end users. It creates a financial hardship for the MRFs themselves, DeFife noted, because the end commodity value doesn’t necessarily cover the processing costs. Fortunately, he said, that financial model is shifting.
“The way that it’s been explained is that the commodity price pays for recycling, which has never really been true,” DeFife said. That has been more visible in the glass space over the years, but the market shocks from China’s National Sword policies and the COVID-19 pandemic have meant paper and plastic face similar dynamics periodically.
“MRF fees are now evolving to cover the processing fees and the handling fees for the material that’s in there, not just a commodity price system,” DeFife said.
Hennemann noted some MRFs do a great job sorting glass with low contamination, and the Glass Recycling Coalition has a program to recognize such MRFs. It’s not a formalized certification program, she added, but it’s a way to highlight MRFs that are putting in the effort to produce a higher quality glass stream.
Still, DeFife added, the program has some real benefits: He said there have been multiple cases of MRFs winning municipal contracts in part because of their glass performance being validated by the Glass Recycling Coalition.
Brand owner looks to boost collection with regional programs
The daunting challenge of hitting upcoming target dates has led to some creative initiatives to boost U.S. glass collection, explained Gabriel Opoku-Asare, director of environment, social and governance at major glass end user Diageo North America. The company owns numerous spirit brands, including Crown Royal and Johnnie Walker.
The company’s packaging commitments include ensuring all of its packaging is widely recyclable by 2030, and hitting 60% recycled content across all its packaging by the same year. On the glass side, Opoku-Asare was blunt about the challenge: “We are nowhere near that space,” he said of the 60% goal.
One challenge for Diageo in the U.S. is that the locations where it operates production facilities have relatively low glass recycling rates, Opoku-Asare said. In Chicago, for instance, the recycling rate is less than 30% for glass, and in Kentucky, it’s less than 15%.
The company is trying to improve those rates in several ways, he explained, including joining the “Don’t Trash Glass” partnership. Headed up by the Glass Packaging Institute and GlassKing, the program launched in Phoenix in 2018 and expanded to Illinois in 2021.
Don’t Trash Glass creates a glass-only collection program targeting bars and restaurants, which are high-volume glass generators. The program facilitates placement of indoor and outdoor containers for glass collection at these establishments. The material is collected, sent to a nearby processing facility and then supplied to a bottler, like Diageo.
Diageo joined the program when it reached Chicago, Opoku-Asare said, as a way to boost the amount of recycled glass available for its packaging. Diageo identifies establishments that provide significant volumes of the type of glass it needs, and the Glass Packaging Institute and GlassKing representatives visit those outlets and try to get them to participate in the collection program, and to do it properly.
That involves a lot of work, Opoku-Asare said, particularly when it comes to education and outreach. Behavior change can be hard, especially in a fast-moving environment like a food and drink establishment.
Once the glass is collected, it goes to a sorting facility, he said. In Chicago, that’s a Strategic Materials facility. The glass is sorted, cleaned and sent to a bottle plant, where it is used to make new containers that are shipped to Diageo for bottling. The whole process takes about two weeks, from consumption to new bottle production.
In 2023, the Chicago-area effort collected 2.2 million pounds of glass from 68 establishments.
Diageo joined a similar initiative in Kentucky recently, partnering with other spirits companies and glass giant O-I in an effort to collect production scrap and other end-of-life glass from distilleries. That project has a goal to collect 2.4 million pounds in its first year.