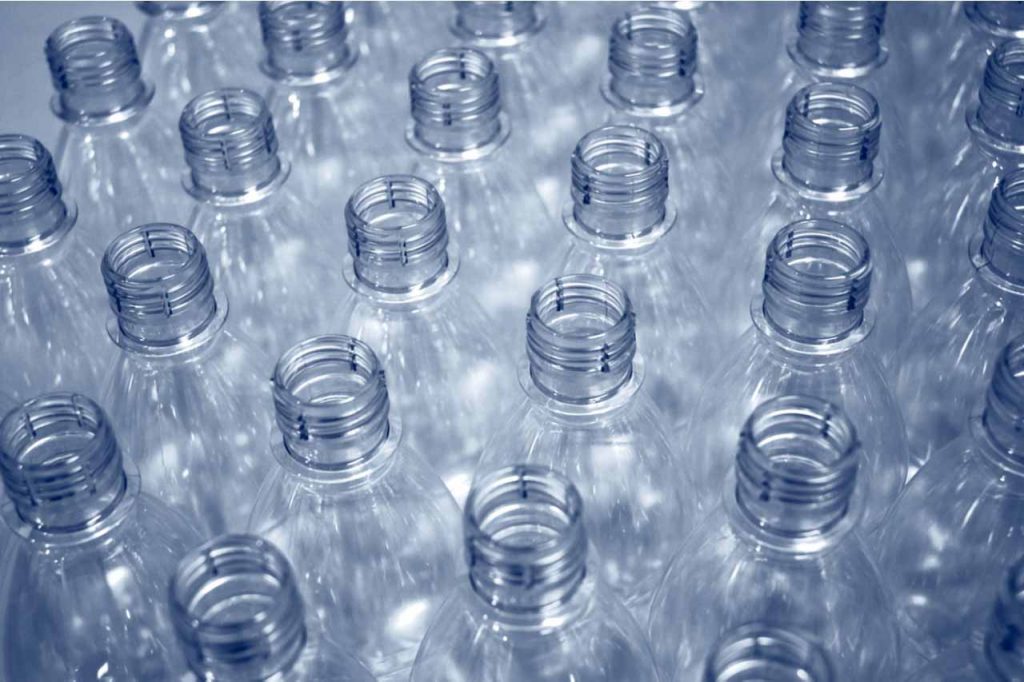
The study looked at mechanical recycling and solvent-based dissolution of PE, PET and PP, as well as enzymatic hydrolysis, glycolysis and vapor methanolysis of PET. | tezzstock/Shutterstock
A study conducted by the National Renewable Energy Laboratory evaluated various PET recycling methods from technical, economic and environmental standpoints to provide a big-picture overview of today’s options.
The research, published by the American Chemical Society, found that mechanical recycling outperformed all other technologies as well as virgin plastic production across economic and environmental considerations, but it ranked lower in technical metrics.
Of several available chemical recycling methods for PET, glycolysis “offered the best economic and environmental performances,” the study found, with areas for future improvement including process yields, consumable reduction or replacement, utility decarbonization and closed-loop recycling for polyolefins.
“Chemical recycling” generally refers to a wide array of processes that use heat, pressure and solvents to break down the molecular chains of polymers into liquids or gasses that can then be processed into fuels, oils, waxes, new plastics or other chemical products.
“This work quantitatively characterized the performances of plastic recycling technologies and established a robust methodology for comparing new recycling processes as they emerge in the future,” the report noted, as well as providing a decision tree to help reclaimers choose the best method for each material.
The study looked at mechanical recycling and solvent-based dissolution of polyethylene (PE), PET and polypropylene (PP), as well as enzymatic hydrolysis, glycolysis and vapor methanolysis of PET, using virgin production as a baseline.
Enzymatic hydrolysis uses hydrolase enzymes to depolymerize PET, glycolysis uses ethylene glycol and methanolysis uses vaporized methanol.
The evaluated metrics were material quality, material retention, circularity, contamination tolerance, minimum selling price, greenhouse gas emissions, energy use, land use, toxicity, waste generation and water use.
Overall, PET mechanical recycling and glycolysis outperformed virgin PET in all metrics, and methanolysis and dissolution scored above virgin levels in the economic and technical sections but scored lower in the environmental and resources sections due to high GHG emissions, toxicity, land use and water use.
Enzymatic PET hydrolysis did not exceed the virgin baseline under any modeled scenario, the study noted.
As for other materials, mechanical recycling of high-density polyethylene (HDPE) outperformed virgin production in the environmental and resources sections but had a low technical and economic score.
Dissolution of HDPE did not reach the virgin threshold for any sections, nor did dissolution of low-density polyethylene (LDPE) or PP, though mechanical recycling of LDPE and PP performed better in economic and technical sections due to lower bale prices, the study reported.
However, lower scores should not mean that technologies are abandoned, the study noted, because “these techniques may not be advantageous across all metrics but could provide benefits in specific priority areas, especially with continued improvements as the technologies mature.”
The study also highlighted improvements for the different methods. Mechanical recycling could benefit from increased bale quality and polymer yield, as well as the addition of advanced sorting technologies such as fluorescent markers or robotic sorting coupled with artificial intelligence, the study noted.
For dissolution, switching to bio-based solvents could improve its environmental score. Enzymatic PET hydrolysis needs increased monomer yields and to use less water to become viable, the study stated.
Glycolysis could also benefit from improved monomer yields as well as new catalysts. PET methanolysis also needs new catalysts, the study stated, and to use less water.
A version of this story appeared in Plastics Recycling Update on Jan. 18.