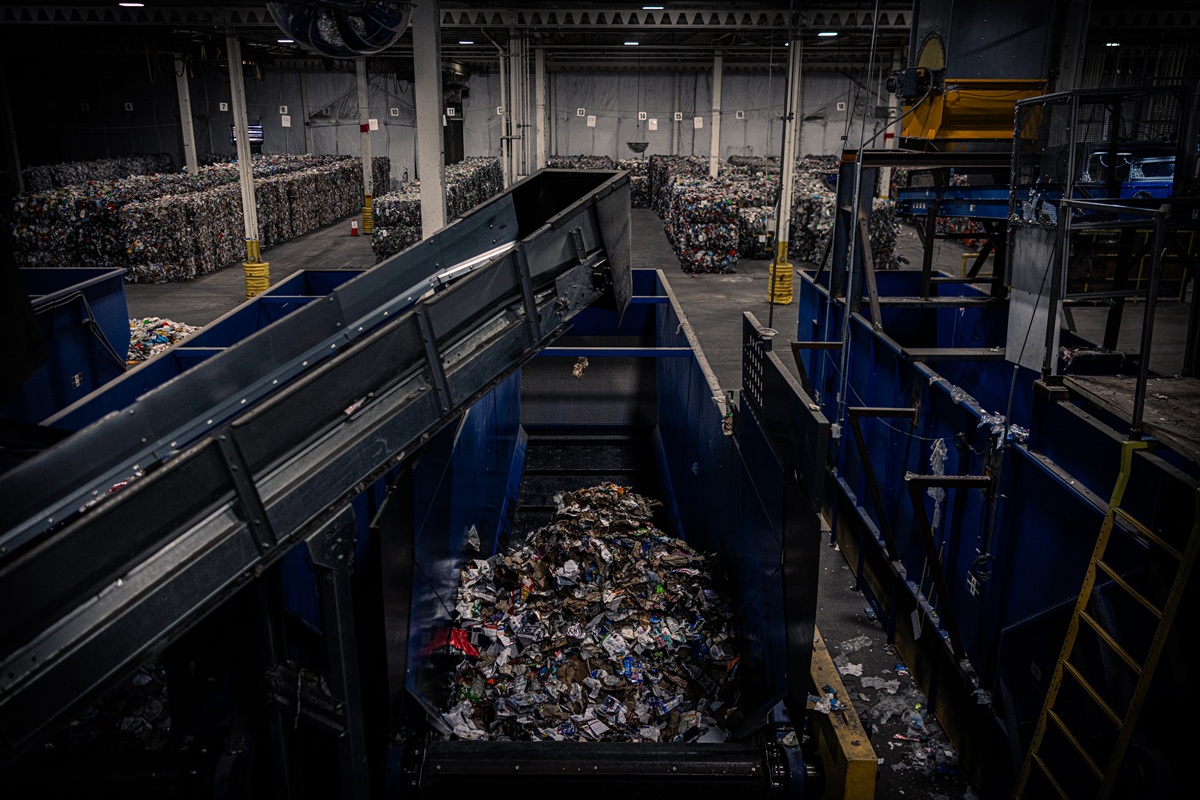
AMP started out producing robotics but now supplies entire sorting facilities with advanced sorting equipment. | Photo courtesy AMP
Emerging extended producer responsibility programs for packaging are creating demand for more accurate data, higher diversion rates and a flexible infrastructure to handle changing material streams. An equipment supplier recently laid out how its artificial intelligence-equipped sorting systems can meet this need.
Louisville, Colorado-headquartered AMP, which started as a robotics company but has expanded to supply entire sorting facility systems, last month hosted a presentation on the opportunity advanced sorting equipment presents in the new world of U.S. packaging EPR.
The company provides a variety of equipment that combines AI with optical sorting systems to identify, track and sort materials in mixed recycling streams with high precision. As materials pass under near-infrared (NIR) camera systems, the technology analyzes each item’s polymer type, color, form factor and size, creating a detailed characterization report. AMP then uses bulk density equations the company has developed to produce composition estimates with a reported 90-98% accuracy. When this data is combined with mass balancing efforts on the finished goods side, AMP gains a full picture of what is getting recycled and what is lost to residue or contamination, said Justin Davis, the company’s director of commercial origination and business development, during the webinar.
Davis described his previous employment with a company that was hired by the city of Fort Wayne, Indiana, to sample some of its collection trucks. The sampling method involved spreading the materials out on the floor and hand-weighing the load. It’s not only a labor- and time-intensive process, but it also exposes facilities to sampling bias due to their inability to characterize the entire stream, Davis said.
In addition to making sampling more efficient, advanced sorting equipment can also provide essential data for EPR compliance.
“Once we have the producer responsibility organization in place, and funded, and the legislation is adopted, how do we know who to charge?” Davis said. “How do we know who to pay and how much? And do we ultimately know if we’re making an impact? Well, that is where the idea of AI helps to assist with compliance.”
Carson Potter, head of product for AMP, added that the company’s sorting systems allow operators to make rapid adjustments, which will be key to meeting EPR requirements. For instance, AMP’s equipment can be quickly reprogrammed to sort different material streams, meaning it can respond to variances in EPR frameworks like quality standards, end-market demands, and recovery rate thresholds, Potter explained.
AMP has also promoted its equipment’s ability to “recirculate” materials on the sorting line, meaning material passes under the cameras several times. That allows the system to choose the best moment to pick the items it is programmed for, to improve bale composition accuracy.
Potter noted the idea of recirculation systems was widely abandoned in the industry due to issues of residue build-up and contamination. But he said AMPs technology can track, sort out and purge residue build-up from the line.
However, recirculation can help existing MRFs increase material recovery rates, Potter said, in turn helping producers meet diversion targets under EPR programs without requiring major facility overhauls.
Potter noted density separation is another component of advanced sorting systems that may be well-suited for meeting the recovery rates needed under EPR systems, because it allows sorting systems to better distinguish two-dimensional materials. That can help address sorting problems that are coming about due to packaging design changes: Potter gave an example of e-commerce giant Amazon’s shift to smaller-format containerboard boxes, noting that older sorting systems have had trouble identifying this type of packaging. Density separation could ease that challenge.