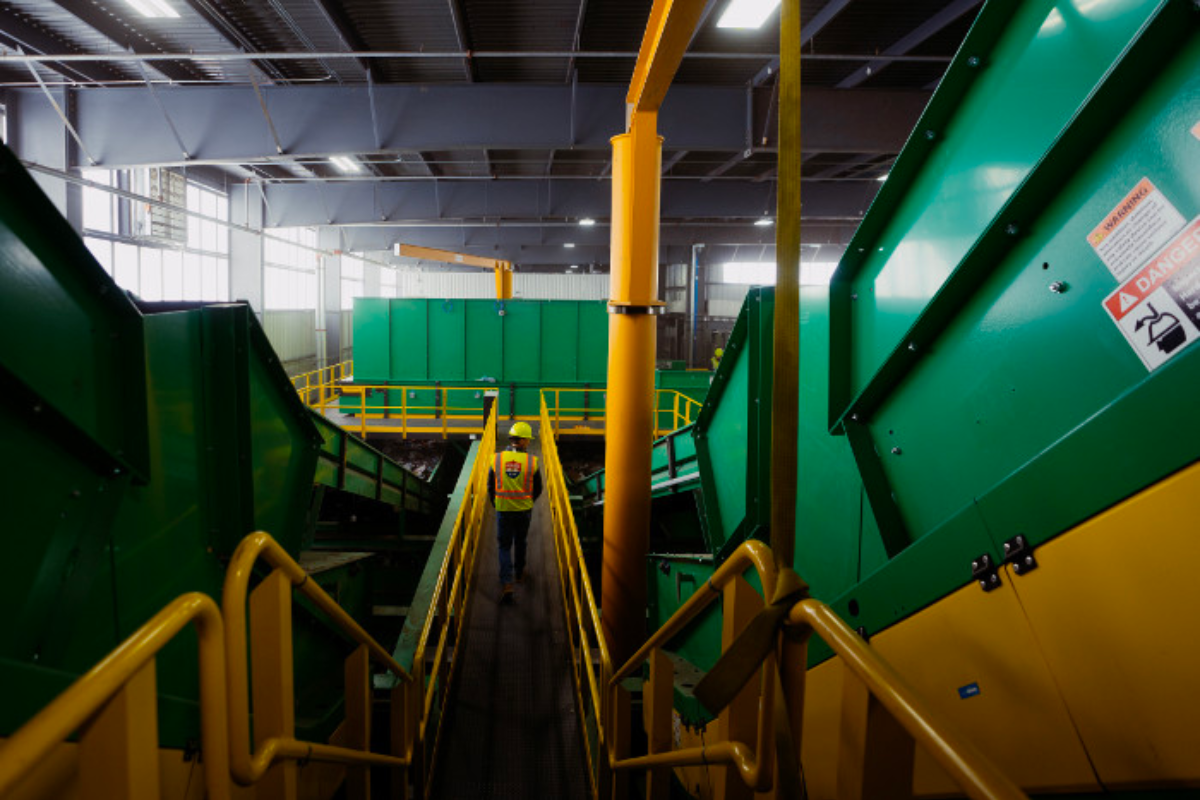
Murphy Road Recycling’s All American MRF recently completed $40 million in upgrades that focused on improved worker safety and fiber recovery. | Courtesy of Van Dyk
The consumer recyclables stream has changed a lot in the last two decades, and a Connecticut MRF recently invested $40 million in an upgrade focused on more granular fiber recovery and worker safety.
Frank M. Antonacci, chief operating officer of Murphy Road Recycling, told Resource Recycling that the Enfield, Conn. MRF’s original system was one of the first single-stream systems in the area when it was installed in 2005.
“It was good at handling the material we got back then, at that volume,” Antonacci said, but as the business grew and technology changes, upgrades were needed.
“We’re really thrilled with the facility we have now, that’s for sure,” he added.
One of the biggest changes to adapt to has been the different size and shape of paper and OCC, Antonacci said: “Everybody focuses on the plastics, but really the size and shape of the paper we get has also changed.”
Everything has gotten smaller, with many boxes under 12 inches in surface area, he said. Older systems were set up to look for much larger material.
“We had a lot of high-value cardboard getting mixed in with the mixed paper and a lot of the mixed paper buyers did not necessarily want the brown in their mixed paper, so you ended up devaluing both the mix paper and cardboard,” he said. “So we focused on getting as much of the small OCC out of the mixed paper streams. We have the fiber recovery set to a much finer level in general.”
Leaning in on technology
The upgrades for the Connecticut All American MRF began in 2020 and were initially estimated at $30 million. By the time the facility came on-line in December 2022, the cost was closer to $40 million, Antonacci said.
That investment expanded the facility from 50,000 square feet to 110,000 square feet and increased processing capacity from 350 tons per day to over 1,000 tons per day. That’s a new speed of 60 tons per hour compared with 25 tons per hour, Antonacci said.
Those speeds are possible thanks to the level of automation in the new MRF. There are 13 optical sorters spread throughout the facility, along with a laser sensor, Deep Laiser, that positively picks black plastics and film from the fiber line.
“The system is based on tried-and-trusted, best-in-class mechanical separation with optical polishing,” Antonacci said. “That layer is on top of some human intervention on the quality-control side. We’re very much a believer in utilizing the best new technology – new and true technologies.”
The container line has fully automated quality control using optical sorters, and a glass benefication system was added to improve glass sorting.
The MRF’s glass previously had to be shipped out of state, because it was not clean enough for local end markets. The upgrade changed that, allowing all the glass All American processes to stay in Connecticut as an ingredient for concrete or for use in insulation and containers.
The new facility was built adjacent to the old facility, which ran normal operations throughout the build process. In a press release, Joe Farese, operations manager at the All American MRF, said the parallel work took a lot of focus and care.
“We couldn’t really let our guard down,” Farese said. “We still had to maintain a high level of safety and maintenance on the old system, even though we knew it was coming to the end of its useful life.”
The older building now houses the improved glass sorting operations and provides warehouse space.
Antonacci said he and the company spent a lot of time in the design phase to make sure the upgrade was a success. He chose Van Dyk Recycling Solutions because the company has a 30-year history and is also based in Connecticut.
“We really engaged our people at our existing facilities to help design the system and I think that does a lot of positive things for the outcome,” he said. “You get buy-in at the operations level, you get real expertise from the people that are dealing with these materials every day and that’s something that is invaluable. You can’t recreate that in any boardroom or any spreadsheet.”
Batteries and worker safety
Another main push in the design process was to “turn a challenging work environment into a much better one,” Antonacci said. There’s better climate control and lighting, and he said everything was arranged so “there was no reason for any people to be under the system during any operation.”
“The system was laid out for the employees,” he said. “We were able to reduce the amount of people that were not positively picking any material by hand. The people are really there for quality control and then pre-sort and we’ve integrated climate controlled and environmental controlled sorting stations for everybody.”
The upgrade also addressed lithium-ion batteries, which Antonacci called a “total nightmare.”
“It’s the No. 1 risk to the solid waste infrastructure in the entire country and I think it’s getting worse by the day,” he said.
The All American MRF has the infrared FireRover remote monitoring system, a sprinkler system underneath the belt system and a deluge system in the drum feeders, but the risk of battery fires “still keeps me up at night,” Antonacci said.
“We need to do better public service announcements, like Smokey the Bear is for forest fires,” he suggested. “There needs to be a national public service campaign to educate people.”
More to come
The new MRF is done, but the upgrade ideas keep coming for Antonacci. The facility was constructed with the space and flexibility to add more equipment, and the technology in place can be reprogrammed easily to adapt to changes in the material streams.
He said the team is already considering the first changes to it, including adding even more optical sorters.
“It’s all good stuff,” he said. “We’re able to see the stream better than ever and make even more educated decisions on what to do next.”