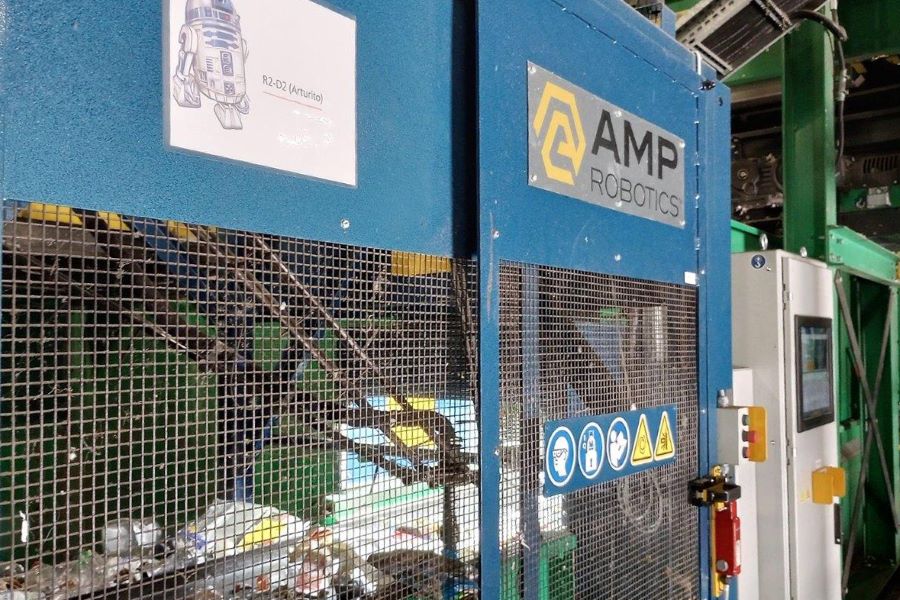
An AMP Robotics unit, nicknamed Arturito, is allowing the city of Dallas to accept cartons at curbside. | Courtesy of FCC Environmental
A recently installed carton-sorting robot at FCC Environmental Services’ Dallas MRF has reduced residue by about 11%, one reason the unit is “going to have a pretty big financial impact for us,” a company manager said.
Bruce Magnuson, senior general manager for Texas recycling operations at FCC, described to Resource Recycling how the grant-funded robot is already yielding numerous financial and materials diversion benefits. He also described how the company paired the sorting technology with a unique materials handling strategy to overcome challenges in recovering a relatively low-volume commodity.
“We’re just really pleased with it so far, and we’re really pleased we can increase the amount of recyclables we’re capturing and reduce the residue,” Magnuson said.
The AMP Robot was installed at the Dallas MRF in the third week of March, he said. According to a press release, funding for the unit came from a grant provided jointly by the Carton Council of North America (CCNA), the Foodservice Packaging Institute (FPI) and the NextGen Consortium, which is an effort led by Closed Loop Partners that focuses on reducing single-use foodservice packaging waste.
From mixed paper to carton bales
FCC’s Dallas MRF sorts residential recyclables collected from the city and its neighboring communities. Prior to installation of the robot, the recycling program didn’t officially include cartons, but residents would often put them in the bin anyway.
At the MRF, if a carton or plastic-lined cup followed other fiber over the sorting screens, it would end up in mixed-paper bales. That’s where a lot of MRFs, if they’re not producing carton-specific grades, sort and sell their cartons. But if the item fell through the screens, it would be disposed of along with other residue.
Now, the AMP Generation 4.3 robot is picking cartons and paper cups from the MRF’s ‘last chance’ line, along with any PET bottles that have liquid in them and were not sorted by optical sorters.
Magnuson, a former MRF manager at Waste Management (WM), said the unit performs much faster than the earlier-generation unit WM used at its Houston MRF. The system normally operates at about 40-60 picks per minute but can work at up to 100 picks per minute, depending on material volumes and separation on the conveyor belts, he said.
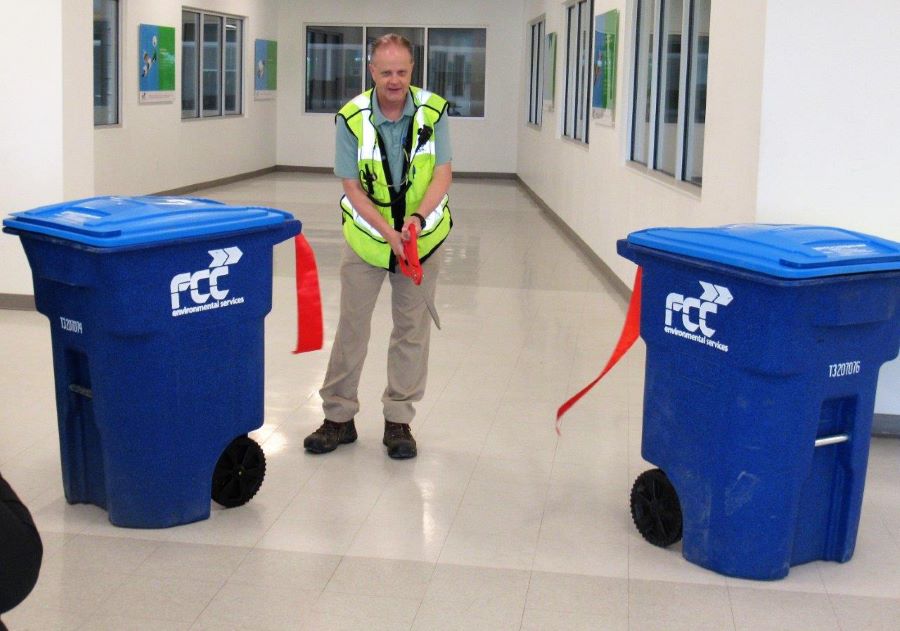
Magnuson at at May 25, 2023, ribbon cutting for the AMP robot at FCC Environmental’s Dallas MRF.
The AMP unit is FCC’s first robot in Dallas, although the company’s Houston MRF uses a RoBB-AQC robot provided by Bollegraaf/Van Dyk Recycling Systems, he noted.
The robot has allowed the Dallas government, which collects recyclables for single-family and duplex homes in the city, to explicitly accept cartons from nearly half a million households. FCC now accepts the materials from other nearby communities served by the MRF, as well.
“It was a big opportunity for the site to try to reduce this out of the waste stream,” Magnuson said.
The Carton Council has been involved in trying to support carton recycling in Dallas before. Over a decade ago, the nonprofit group worked with the city government to help the recyclables processor that held the city contract at that time find end markets for the materials. After winning the 15-year city contract (with the possibility of a decade of extensions) in 2015, FCC built its Dallas MRF, which officially opened in early 2017.
Financial benefits become clear
So far, the robot has driven down residue tonnages by about 11%, Magnuson said.
The MRF is now producing carton-specific bales for sale to a paper mill, Magnuson said. The reduced disposal costs and increased commodity sales revenues are such that payback for the robot would be about six months or so, he estimated.
“It would have been cost effective to do it even without a grant,” said Magnuson, who noted that FCC incurred other minimal electrical and air supply expenses related to the installation.
Some MRFs don’t accept cartons because they lack the bunker space to dedicate to a relatively low-volume commodity such as cartons/cups. Space was initially a concern for FCC, too, Magnuson acknowledged.
To solve the bunker-space problem, FCC has the robot drop materials into a tip hopper, which staff empty a few times a shift into a 30-yard open top container, he explained. That container fills up every couple of days or so, at which point staff members bale the material, getting a couple of bales each time, he said.
Given the capabilities of the robot, Magnuson said, he’s not concerned the system will be unable to keep up once residents begin to widely recognize the materials are now accepted.
“At this point I’m not really worried from a capacity standpoint,” he said. “If we get to that point, I guess it would be a good problem to have and we’ll figure it out.”
More stories about MRFs
- Recycling facility fires expected to reach new high
- Haulers feel effects of lower recycled commodity prices
- WM report suggests 2025 goal is out of reach