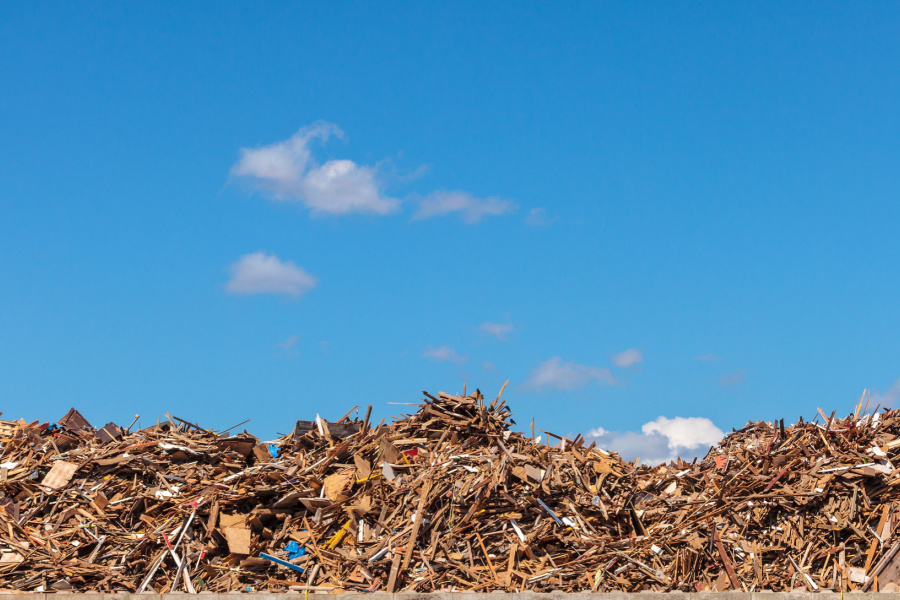
A trio of experts explore the market forces, industry innovations and technological applications that make up the wood recycling landscape. | Martin Bergsma/Shutterstock
This article appeared in the January 2023 issue of Resource Recycling. Subscribe today for access to all print content.
Wood is often an afterthought in recycling discussions, but many industry insiders are keen to heighten the conversation.
A recent webcast,“The Future of Wood Recycling,” gathered three experts, Jose Matas and Murat Sanli from TOMRA and Jan-Olof Fechter of IKEA, to offer perspective on the unique challenges of processing discarded wood into new items.
They also unpacked emerging wood recycling and sustainability opportunities brought on by a changing market.
Market movements
Matas, TOMRA’s wood segment manager, discussed recent global developments that have had an impact on wood markets.
“Of course we should start with this pandemic situation,” Matas said. “We were shut down due to the lockdown, demand has been reduced so a lot of shipping lines were reduced.”
On top of the COVID-related supply chain constrictions, according to Matas, the war in Ukraine is making it difficult to acquire fresh wood. “Russia and Belarus are two of the main wood exporters for the European Union,” he said. “So now with the sanctions … this limitation is putting even more pressure on the wood market.”
“So what is the impact of all that?” he asked. “As you can imagine, raised prices.”
However, Matas sees opportunities among all the doom and gloom. Increased prices for fresh wood, he said, mean that formerly unprofitable grades of recovered wood such as A2, A3 and A4 (treated wood) now have the potential to make wood recyclers money.
“These categories normally, historically,” he said, “had no value, low value or even ‘pay for disposal’ because it was treated material. Nowadays, and due to this situation of lack of wood, even these categories have some value.”
For collectors, this phenomenon means that taking in these types of wood is no longer a losing proposition. And for the wider recycle/reuse industry, it means that recycled wood is now a boon for profit margins.
“If you buy fresh wood,” Matas noted, “it has a higher price than if you buy recycled wood.” This means there is “a direct benefit on cost if you use recycled material instead of fresh wood.”
Matas sees other upsides to using recycled wood over fresh wood. For one, recycled material tends to be dryer.
“By using recycled wood,” he said, “you will use less energy in your process to dry and prepare the material for production, giving you some extra savings.”
What’s more, recycled wood can be sourced locally, circumventing any geopolitical concerns.
“Due to the COVID situation and struggles with the supply chain,” Matas said, “it was difficult to import material. Now we can secure our supply thanks to the local supplier. We don’t need to depend on overseas countries in order to get our raw material.”
On top of these pros on the business side, Matas argued that recycled wood addresses environmental concerns as well. “We are saving the forest because now we don’t need to cut any more trees in order to get it,” he said.
Reuse and circularity
Jan-Olof Fechter, material and technique engineer at IKEA, echoed Matas’ message about the multifaceted benefits of wood recycling, saying the furniture giant is “talking about affordability and sustainability at the same time.”
“IKEA is committed to transforming into a circular business,” he said, noting that there are multiple approaches to achieving this end.
One such method, Fechter said, “has to do with buying back the furniture, reselling it, refurbishing it,” adding that his company offers this option in all of their operating markets.
“When you don’t like your IKEA furniture anymore,” he said, “you just bring it back to us and you receive an offer – we pay for it, buy it back and we try to sell it to somebody else if it is in good shape.”
He also used the example of leasing as another way to achieve circularity. By selling furniture for a set period of time, primarily to businesses, IKEA can then take the furniture back and lease it again.
Fechter said his company is also highly interested in using recycled wood to make new furniture.
“What we’re also doing is recycling material to make furniture again,” he noted. “This has been done for many, many years in the particleboard industry already. It’s a quite straightforward process.”
According to Fechter, IKEA has big plans for growing its recycling work in the future.
“At the moment,” he said, “we are already at a 25% share of recycling particle board,” noting that particle board is IKEA’s most-used material (particle board is an engineered material made from wood chips and a binding agent, and it typically carries lower costs than traditional wood).
“But our goals are more ambitious,” he continued. “The 2030 goal is set to 80% for particle board because we see the advantages.”
To put things in perspective, Fechter noted that IKEA reused about 2,300 metric tons worth of furniture in 2021, but that amount pales in comparison to the roughly 800,000 metric tons of recycled material used by the company.
“So reusing is the future, but recycling is what we can do today for the environment,” he said.
Driven by technology
The webinar’s third and final speaker, TOMRA sales engineer Murat Sanli, capped things off by explaining some of the technology that makes wood recycling possible, starting with sorting equipment used to create a homogenous stream of material.
“Pre-treatment requirements are mainly for mixed waste,” he said. “To sort it in a successful way, we need a shredder to shred the material into small pieces. For example, a chair – it’s not that easy to sort a chair at all. Of course, when you shred it into smaller pieces, it will be easier.”
The next step, he said, is screening the material. This entails separating metals, which can be done using an overbelt magnet to remove ferrous metals and an eddy current to extract non-ferrous metals.
Finally, the stream must use a wind sifter to divide the heavy components from the light ones. “For example,” Sanli said, “the light material will be films and papers, and the wood will be separated.”
Once a homogenous stream has been achieved, it needs to be cleaned, he said. At this point, processors can use either traditional or modern methods.
Traditionally, wood streams have been cleaned using air separators, which remove impurities the same way they removed films and paper, and sink-swim separators, which make wood float to the top while unwanted materials fall to the bottom.
Both of these have limitations, however. With air separators, Sanli said, “you have not only wood chips, you have massive wood, which will be a loss for you.”
In the case of sink-swim separation, he said, impurities such as wood with nails will “swim” along with the desired materials.
However, he noted, “now we have the answer for that with the modern systems.”
Those modern systems consist of varying combinations of three key components: X-ray sorters, near-infrared (NIR) sensors and electromagnetic sorters.
X-ray sorters, Sanli said, “will sort the material by atomic density, and even the wood with nails will be sorted out,” making up for the deficiencies of sink-swim separation.
Using spectrographic information, NIR sorters can be utilized, he said, “to sort wood from non-wood.” Then, he said, “you can combine it with an electromagnetic sensor to sort out the last pieces of metal.
Used in conjunction with each other, these components can create a homogenous stream containing only the materials needed to meet a client’s given specifications.
The “extra mile,” according to Sanli, is to apply deep learning software “that uses a massive library of images to identify and differentiate between wood chips and wood chip types.”
Dan de la Vega is the copy editor at Resource Recycling and can be contacted at [email protected].
This article appeared in the January 2023 issue of Resource Recycling. Subscribe today for access to all print content.