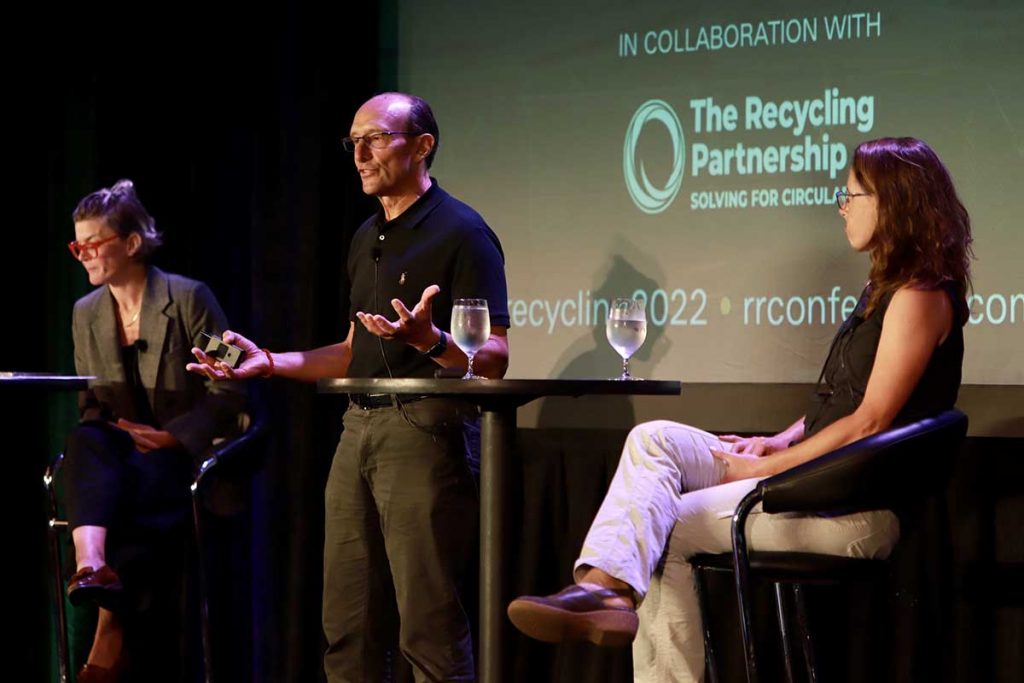
Eric Hartz (center) spoke on a panel with Kate Bailey (right) at the 2022 Resource Recycling Conference. The session was moderated by Sarah Edwards (left). | Big Wave Productions/Resource Recycling, Inc.
Recent years have seen a steady stream of announcements from chemical recycling operators touting technological breakthroughs. But two industry insiders recently issued a stern reminder to the market: Don’t forget about economics.
“You don’t win when you get technology,” Eric Hartz told the audience at a chemical recycling session at last month’s Resource Recycling Conference in Austin, Texas. “Technology brings you to the starting line. You win when it’s economic and when it’s scalable.”
Chemical recycling (sometimes called advanced recycling or molecular recycling) is a broad term covering a variety of processing technologies that break down recovered plastics to the molecular level, with the goal of using that material as the building blocks of new plastics or other chemical products.
However, Hartz, who co-founded the Atlanta-based plastics pyrolysis company Nexus Circular, noted that few companies developing chemical recycling processes have actually found ways to secure feedstock, process material and sell products out the back end in a manner that also leads to consistent profitability.
As community recycling programs, brand owners and other stakeholders look for end-of-life solutions for plastic materials, that notion of economic viability is an important consideration when vetting potential partners.
“Don’t check your brain at the door on this,” Hartz said. “Don’t be fooled by hearing, ‘We’ve come up with something new.’ Follow the money and follow the molecules and you’ll come to the right answer.”
That advice was echoed by Kate Bailey, the second panelist on the session.
Bailey is policy and research director at Boulder, Colo.-based Eco-Cycle, a nonprofit materials recovery facility (MRF) operator that also manages collection and resident outreach. The organization handles roughly 65,000 tons of material annually.
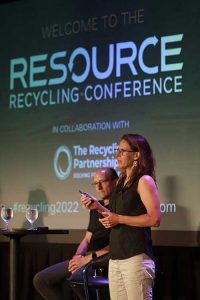
Kate Bailey speaks on stage at the 2022 Resource Recycling Conference. | Big Wave Productions/Resource Recycling, Inc.
She said Eco-Cycle has been approached by a variety of chemical recycling operators. Often, those firms have been looking to source mixed plastic bales, but they’ve also asked about polypropylene loads.
And, with recent pricing downturns, Eco-Cycle has heard chemical recycling inquiries in regards to PET as well.
From Bailey’s perspective, the economics question is critical because public trust in recycling is already dangerously low – MRFs and cities don’t want to get caught sending material to a downstream that goes under or mismanages the plastic.
She said Eco-Cycle has made the decision to only supply material to a chemical recycling operator if that plastic is for certain going into new plastic, as opposed to a fuel or other product.
“We have not found a company that can guarantee it will not go to fuel,” Bailey said. “I can’t take that risk. You as a community and you as a MRF are the ones the public is trying to hold accountable.”
‘In a specialty market’
Market conditions for recycled plastic are constantly changing, a fact that can add complications to determining the economic viability of processors scaling up technology.
Hartz said that as brands continue to look for material to meet sustainability goals, he expects recycled resin to see strong demand.
“We are not in a commodity market right now, we are in a specialty market,” he noted. “Supply is miniscule and demand is huge. We predict for quite some time there is probably going to be that price disparity [between virgin and recycled plastic].”
But Bailey pointed to falling PET prices as an example of the rocky landscape MRF operators and local programs find themselves in. Volatility around PET, a material that has well-established recycling infrastructure, makes it hard for facility operators to make investments, she said.
“We have brands saying they can’t get enough supply, and yet we are seeing bottom-dollar prices,” Bailey said. “It becomes even more complicated when we start adding new technologies.”
And it doesn’t help when companies come knocking with little understanding of on-the-ground realities for MRFs.
“I’ve actually been asked how much I’m going to pay the chemical recycling company to take my loads,” Bailey said. “That’s not how it works. This idea that I’m going to give it to you for free doesn’t recognize that I as a MRF have real costs.”
For Bailey and other operators, the current period is one of asking the right questions to all the processors vying for material. And the hope is that over the long term, economic realities will ultimately prove which companies are viable.
“The industry of advanced recycling, we have to deliver,” Hartz said. “We have to perform. The burden is on us to build plants at scale that work.”
A version of this story appeared in Plastics Recycling Update on August 31.
More stories about markets
- ‘Operational readiness is high’ as Oregon rolls out EPR
- Pizza box demand declining, report says
- Paper operations close in Georgia, Texas